Aluminum alloy die casting or alu die casting is a manufacturing process used to produce complex and detailed parts and components made of aluminum alloys. In this process, molten aluminum is injected into a high-pressure steel mold, known as a die, to form the desired shape. Once the aluminum solidifies, the mold is opened, and the finished part is ejected. This method is called “die casting” because the mold, or die, is a permanent, reusable tool.
Aluminum die casting technology process that has been at the heart of manufacturing for many years. In recent times, but, this age-old method has seen a fresh wave of innovation. From stronger, lighter materials to sustainability efforts, the industry is embracing change and redefining how products are made.
In this article, we will explore these exciting innovations in aluminum alloy die casting, and the trends shaping 2023 and beyond.
Lighter and Stronger Alloys
The creation of strong and lightweight alloys is among the most notable developments in aluminum alloy die casting. Because they combine durability with decreased weight these modern materials are especially important to sectors like aerospace and automotive. Their ability to endure severe settings and improve fuel efficiency is revolutionizing the construction sector.
Type aluminum alloys usedin die casting
Aluminum alloys used in die casting are specifically formulated to meet the requirements of the die casting process. These alloys offer a combination of good casting properties, mechanical strength, and corrosion resistance. Here is a list of some common aluminum alloys used in die casting:
- A380: A380 is one of the most widely used aluminum alloys for die casting. It offers excellent fluidity and is well-suited for complex, thin-walled parts. A380 has good mechanical properties and is used in a variety of applications, including automotive components, household appliances, and electrical enclosures.
- A383: A383 is a modified version of A380, featuring improved resistance to hot cracking and better thermal stability. It is commonly used in die casting applications where higher temperatures are involved, such as engine components and heat exchangers.
- A360: A360 is known for its high corrosion resistance and excellent pressure tightness. It is used in applications where exposure to harsh environments or chemicals is a concern, such as pumps, valves, and marine components.
- A384: A384 is designed for applications that require improved machinability. It offers good die castability and can be used in parts that need post-casting machining.
- A390: A390 is an alloy known for its excellent castability and mechanical properties. It is used in a wide range of applications, including automotive components and various industrial parts.
- AlSi10Mg: AlSi10Mg is an alloy that includes silicon (Si) and magnesium (Mg). It is commonly used in high-temperature applications, such as components in the automotive and aerospace industries.
- AlSi12: AlSi12 is another aluminum-silicon alloy used in die casting. It offers good castability and is suitable for components that require a balance of strength, ductility, and corrosion resistance.
- AlSi9Cu3: AlSi9Cu3 is an alloy that includes silicon and copper (Cu). It provides good mechanical properties and is used in a variety of applications, including automotive parts.
- AlSi7Mg: AlSi7Mg is an alloy with high silicon and magnesium content. It is used in applications where high-temperature resistance and thermal stability are essential.
- AlSi8Cu3: AlSi8Cu3 is another alloy with a combination of silicon and copper. It offers good mechanical properties and is used in a wide range of die-cast components.
These are some of the commonly used aluminum alloys and other alloys in die casting, such as magnesium die casting, bronze die casting, zinc die casting, etc. and the choice of alloy depends on the specific requirements of the application, such as strength, corrosion resistance, thermal properties, and castability. It’s essential to select the most appropriate alloy to ensure the successful and efficient production of die-cast parts.
Precision Casting for Reduced Waste
Innovation is driving a more efficient and precise casting process. Advanced Alu die casting technologies are helping manufacturers cut waste and streamline production. These improvements encompass enhancements in mold design, controlled metal flow, and cooling systems. The result? Here are some of the ways in which the aluminum die casting process contributes to waste reduction:
- Near-Net Shape Casting: Aluminum die casting is known for its ability to produce casting parts that are very close to their final dimensions. This minimizes the need for additional machining or finishing processes, reducing the generation of machining waste and material waste.
- Reduced Material Usage: The die casting process is highly efficient in terms of material usage. Aluminum is injected into the mold to create the desired part with minimal waste. Unlike machining processes, where material is cut away from a solid block, die casting starts with just the necessary amount of aluminum.
- Recyclability: Aluminum is a highly recyclable material, and scrap or excess material generated during the die casting process can be collected and recycled. This minimizes the environmental impact and reduces the need for raw aluminum production.
- Complex Geometries: Die casting is well-suited for producing complex and intricate parts with fine details, thin walls, and undercuts. This means that components that would be challenging to produce through other methods are manufactured with minimal waste.
- Multi-Cavity Molds: Multi-cavity molds allow for the production of multiple parts in a single casting cycle. This not only optimizes material use but also increases production efficiency, reducing waste related to setup and changeover times.
- Minimal Post-Processing: Due to the near-net shape capabilities of die casting, there is less need for extensive post-processing, such as grinding or finishing. This results in less waste generated during part finishing.
- Lean Manufacturing Practices: Lean manufacturing principles can be applied to the die casting process to streamline workflows, reduce inefficiencies, and minimize waste. By optimizing the process, manufacturers can reduce waste and increase overall efficiency.
- Quality Assurance: Proper quality control measures can help reduce the production of defective or non-conforming parts. Fewer rejected parts mean less waste generated during the production process.
- Energy Efficiency: Modern die casting machines are designed for energy efficiency, reducing the overall environmental impact of the process.
- Inventory Management: Efficient inventory management practices help reduce excess or obsolete parts and raw materials, minimizing waste related to overstock or disposal.
Aluminum die casting is a sustainable and environmentally friendly manufacturing process that aligns with waste reduction goals. It not only minimizes the material waste generated during production but also contributes to energy savings and reduced environmental impact. Manufacturers can further enhance the waste reduction benefits by continuously improving their processes and implementing sustainable practices.
New Applications andRising Demand
- The continuous innovations in aluminum alloy die casting are sparking rising demand.
- New applications are emerging in industries before untouched by die casting, such as consumer electronics and renewable energy.
- The versatility of aluminum alloy die casting is drawing attention and proving its worth across various sectors.
Sustainability at the Forefront
Environmental concerns have spurred innovation in aluminum alloy die casting. With initiatives to lessen the casting process’ carbon footprint, manufacturers are embracing sustainability. Materials recycling, energy efficiency, and casting process adoption are some of the innovations in this field.
Complex Geometry and Fine Detail
Producing components with complicated and sophisticated shapes is another innovative breakthrough.
Refinements are being made to high-pressure die-casting techniques to produce components with intricate features and difficult designs. This opens up new possibilities for various industries from electronics to medical devices.
Data-Driven Optimization
Another creative step is to incorporate sensors and data analytics into the die-casting process. The process is optimized and becomes more consistent and efficient with the use of real-time data collecting and analysis. This trend aligns well with the principles of Industry 4.0.
Summary
The driving forces behind this revolution in aluminum die casting are financial benefits sustainability and superior performance. The sector is advancing thanks to innovations and since technology develops quickly fascinating discoveries ought to happen next. These advancements are revolutionizing industrial processes and opening up previously unimaginable new uses.
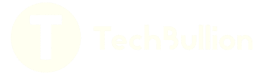