Die casting refers to a metal casting process where molten metal is poured into a cavity and allowed to cool. The molten metal, usually brass or zinc, is heated at approximately 660° Fahrenheit and cast into the die cavity with a force of around 10 tons per square inch.
1. How it Works
In this process, molten plastic rubber, or metals are poured into a die. Molten metal is poured into the die (the part of the casting machine that holds the design), and the two are allowed to cool to solidify. When the pieces have cooled, they are removed from the mold and inspected for imperfections. They can be melted in another location and remolded if any need to be fixed. The molded part can then be formed into whatever shape you desire.
2. Specific Uses
With the vast array of materials available and the ability to create nearly any shape, finding something a die-cast cannot do is almost impossible. Toy manufacturers often use die castings for mechanical or movable parts on toys, such as working wheels and axles. These parts have proven so reliable that children sometimes believe that these components are the actual physical part rather than traditional molded plastic.
3. Types of Die Castings
There are two general types of die-casting, low-pressure and high-pressure.
Low-pressure die casting pumps air into the mold to blow the molten metal out. This process of Low-pressure casting allows for an excellent amount of detail to be knocked into a final product.
High-pressure die-casting works by applying a vacuum to the melt before it is poured into the cavity. Due to this vacuum, the metal is forced down into the die at a higher velocity. This imparts more force onto the metal, making it harder and stronger. The parts are then removed from the mold and inspected for imperfections before being remolded if necessary.
High-pressure die castings, such as vacuum meters and shuttle rods, are used in industrial applications. These have a higher level of precision and need to be stronger than low-pressure die castings.
4. How it Affects the Environment
In general, die-casting has a very low impact on the environment. The process of melting and heating plastic is similar to many other plastics manufacturing processes, and all of these are generally considered to have a low environmental impact.
5. Cost
The cost of die casting depends on the complexity of the part and the materials used. Low-pressure die castings are much cheaper than high-pressure dies and consume less metal, so they are generally cheaper to produce over many items.
High-pressure die castings have higher production costs but make for more vital parts, so that they will be in demand for specific applications. Regardless of their price, all die castings are a desirable option for objects that must be strong and accurate.
Die-casting is one of the enormous technological advances in modern plastic manufacturing, and it will continue to be used for many years. The versatility of the process has made it one of the most versatile manufacturing processes used in modern society.
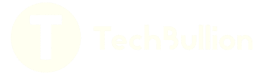