Introduction
In modern manufacturing, die-casting technology, known for its high efficiency, precision, and cost-effectiveness, has become a key manufacturing process. Its history dates back to the late 19th century, initially used mainly in the printing industry. However, with the rapid development of industry, die casting has evolved into a method of manufacturing that is applicable across multiple domains and is known for its high precision.
Die casting, a metal casting process, involves injecting molten metal into a mold cavity under high pressure, quickly cooling and solidifying to form precise metal parts. The advantage of this technology lies in its ability to produce parts with precise dimensions and complex shapes, with smooth surfaces, reducing or eliminating the need for further processing. Due to its efficient production capabilities and outstanding product quality, die casting has been widely applied in various fields such as automotive, aviation, and electronic devices.
With continuous technological advancements, die casting technology is constantly developing and innovating. The emergence of new materials and processing technologies enables die casting to meet more complex and stringent design requirements. From the early use of single metals to the current application of various alloys and high-performance materials, this technology has become an integral part of precision manufacturing.
This article aims to delve into various aspects of die casting technology, including its working principles, material selection, process optimization, and applications in various industrial fields. By analyzing its developmental history and current technological innovations, we can foresee the significant role of die casting technology in the future of manufacturing and its potential development trends.
Die Casting Fundamentals
Die casting technology, an efficient method of metal casting, fundamentally utilizes high pressure to push molten metal into a precisely manufactured mold cavity. The high pressure in this process ensures that metal flows into every corner of the mold, forming intricate and complex designs. Once the metal cools and solidifies, it forms a cast piece with the desired shape, characterized by precise dimensions and a smooth surface, usually requiring no further processing.
Types and Features of Die Casting Machines
Die casting machines are mainly divided into two categories: hot-chamber and cold-chamber die casting machines. Hot-chamber die casting machines are used for low melting point metals like zinc and magnesium alloys, characterized by fast cycle speed and high efficiency. In contrast, cold-chamber die casting machines are suitable for high melting point metals, such as aluminum and copper alloys, capable of processing high melting point materials, but with a relatively slower cycle speed. 188channel.
Working Principle
Whether it’s hot-chamber or cold-chamber die casting machines, the core principle involves quickly and under high pressure injecting molten metal into the mold. This process includes closing the mold, injecting molten metal, cooling and solidifying, and opening the mold to remove the cast piece. These actions are typically completed within a few seconds, making die casting an ideal choice for mass production.
Advantages of Die Casting
The main advantage of die casting is its ability to rapidly produce a large number of parts with precise dimensions and complex shapes. Due to the precision design of molds, the cast pieces have smooth surfaces and clear details, reducing the need for subsequent processing. Additionally, die casting also provides good dimensional stability and strength, making it an ideal choice for producing high-performance parts.
Material Selection and Processing
In the die casting process, the selection of materials is crucial as it directly affects the quality, performance, and cost-effectiveness of the final product. Different metals and alloys are suited to different applications based on their physical and chemical properties.
Commonly Used Metal Materials
Common metals used in die casting include aluminum alloys, zinc alloys, magnesium alloys, and copper alloys. Aluminum alloys, known for their light weight, high strength, and good corrosion resistance, are particularly popular in the automotive and aerospace industries. Zinc alloys, due to their excellent flowability and ease of casting, are commonly used to manufacture small precision parts. Magnesium alloys are favored in lightweight applications for their extremely low density and high strength-to-weight ratio. Copper alloys are widely used in electronics and electrical fields for their excellent electrical conductivity and wear resistance.
Material Preprocessing
To ensure the smooth progress of the die casting process and high-quality output of cast pieces, appropriate preprocessing of metal materials is an essential step. Preprocessing includes melting, alloying, removing impurities and gases, etc. These steps help improve the fluidity of the metal, reduce porosity and inclusions, thereby enhancing the mechanical properties and surface quality of the cast pieces.
Criteria for Material Selection
The choice of suitable materials depends not only on their physical and chemical properties but also on cost-effectiveness, processing difficulty, and specific requirements of the final application field. For example, aluminum and copper alloys are preferred in applications requiring high strength and heat resistance; whereas, for cost-effectiveness and ease of processing, zinc and magnesium alloys might be better choices.
Optimization of Die Casting Process
To ensure the highest quality and production efficiency of die-cast parts, meticulous optimization of the die casting process is essential. This involves not only improving production efficiency but also reducing defects, lowering costs, and enhancing product quality.
Optimization of Mold Design and Manufacturing
The design and manufacturing of molds are crucial to the die casting process. An optimized mold design can improve the flow of metal, reducing defects such as porosity and thermal cracking. Using high-quality mold materials and precise machining techniques can extend the life of the mold, reduce downtime, and increase production efficiency.
Parameter Optimization
Parameters in the die casting process, such as injection speed, pressure, temperature, and cooling time, directly impact the quality of the cast pieces. Precise control of these parameters ensures the uniform distribution of metal in the mold, reducing internal stress and shrinkage. Utilizing modern sensors and control systems for real-time monitoring and adjustment can significantly enhance the consistency and quality of products.
Quality Control Techniques
Implementing stringent quality control is key to ensuring the quality of cast pieces. This includes inspecting raw materials, monitoring the production process, and conducting precision testing of finished cast pieces. Advanced detection technologies like X-ray and computer tomography (CT) scanning effectively identify internal defects, ensuring products meet strict quality standards.
Continuous Improvement and Automation
With technological advancement, continuous improvement of the die casting process becomes increasingly important. Introducing automation technology not only increases production efficiency but also reduces human error, ensuring the consistency of product quality. Simultaneously, by collecting and analyzing production data, the production process can be continuously adjusted and optimized for more efficient and economical production.
Applications of Die Casting in Various Industries
Due to its high efficiency and ability to produce precision parts, die casting technology plays a key role in multiple industries. Below are examples of die casting applications in some main industries, showcasing the technology’s diversity and breadth.
Automotive Industry
In the automotive industry, die casting technology is widely used to manufacture engine components, gearbox parts, and structural elements of the body. Aluminum die cast parts, with their lightweight and high strength, are particularly important in manufacturing energy-efficient and emission-reducing vehicles. The precision and durability of die-cast parts significantly impact the performance and safety of automobiles.
Aerospace
The aerospace industry has extremely high performance requirements for parts, and die casting technology can produce high-quality parts that meet these stringent demands. Aluminum and magnesium die cast parts are often used in aircraft structures to reduce weight, improve fuel efficiency, and enhance flight performance.
Electronics and Communication
In electronics and communication, die casting technology is used to manufacture various precision components, such as mobile phone casings, computer components, and connectors. These parts require precise dimensions and good electromagnetic shielding performance, which die casting technology can provide.
Medical Equipme
In the medical equipment industry, die casting technology is used to manufacture surgical instruments, components of medical diagnostic equipment, and housings. These applications typically require high precision and reliability, which die casting can provide.
Consumer Goods and Household Appliances
Die casting is also widely used in producing various consumer goods and household appliance parts, such as cookware, tools, and decorative items. These applications emphasize die casting technology’s ability to produce products with complex shapes and high-quality surface finishes.
Future Outlook
With continuous technological progress, the die casting industry faces a series of innovations and transformations. With the development of material science, the emergence of new alloys will further enhance the performance and application range of die cast parts. In addition, the integration of digitalization and automation technologies heralds more efficient and intelligent production processes, not only increasing production efficiency but also enhancing product quality and consistency.
Environmental sustainability will also become an important direction for the future development of the die casting industry. With increasing environmental protection requirements, energy saving, emission reduction, and the use of recyclable materials will become key points in industry development. Meanwhile, the combination of advanced manufacturing technologies like 3D printing with traditional die casting may bring new design possibilities and more flexible production methods.
Conclusion
Die casting technology, as a long-standing and continuously evolving manufacturing method, has proven its irreplaceable position in modern industry. From automotive, aerospace to electronics, and medical fields, the application of die casting technology is extensive and profound. With the development of new materials and technologies, die casting will not only continue to meet the modern industry’s demands for efficiency and precision but also lead the manufacturing industry towards higher automation, intelligence, and sustainable development.
In summary, the future of die casting technology is filled with limitless possibilities and opportunities. With continuous innovation in technology and ongoing industry advancement, there is good reason to believe that die casting will continue to be a significant driving force in efficient and precision manufacturing, ushering in a new era for the industry.
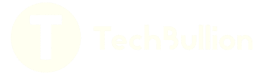