Introduction
Die casting plays a significant role in the automotive sector, enabling the efficient production of top-notch and intricately crafted components. This article offers an expert’s viewpoint on the utilization of die casting in automotive manufacturing, shedding light on its importance and profound influence within the industry.
Efficient Production of Complex Components
Die casting is widely employed in the automotive sector to efficiently manufacture components with complex geometries. The die-casting process empowers the manufacturing of complex shapes and structures with thin walls, which are often difficult to achieve using alternative production methods. This unique capability facilitates the creation of lightweight components that maintain their strength and durability. Automotive applications commonly rely on aluminum alloys in die casting due to their well-known strength-to-weight ratio.
Die castings, sometimes known as pressure die casting, are used in automotive housings, appliance components, and toys.
Engine Components
Die casting plays a vital role in producing various engine components for automobiles. Parts such as cylinder heads, engine blocks, and transmission housings can be efficiently manufactured through die casting. The process ensures the production of parts with precise dimensions, excellent surface finishes, and intricate internal features. The high heat resistance and mechanical strength of die-cast engine components contribute to the overall performance, reliability, and efficiency of automotive powertrains.
Structural Components
Die casting is instrumental in the production of structural components in the automotive industry. These components include chassis parts, suspension components, and brackets, among others. The ability to create complex shapes and maintain tight tolerances makes die casting an ideal choice for manufacturing lightweight yet robust structural components. Aluminum alloys, with their superior strength and corrosion resistance, are commonly utilized in this application, allowing for the development of reliable and safe automotive structures.
Electrical and Electronic Components
Die casting is extensively employed in the production of electrical and electronic components for automobiles. These components encompass connectors, housings for sensors and control modules, and heat sinks. Die casting enables the precise formation of intricate shapes, ensuring optimal fit, performance, and durability of these critical components. The use of die casting ensures reliable electrical connections, electromagnetic compatibility, and effective heat dissipation in automotive electronic systems.
Advantages in Quality and Cost-Efficiency
Die casting offers significant advantages in terms of quality and cost-efficiency in automotive manufacturing. The process ensures excellent dimensional accuracy, tight tolerances, and repeatability, resulting in the consistent production of high-quality components. The streamlined production workflow, combined with the ability to create complex shapes directly from the mold, reduces the need for additional machining operations, thereby saving time and cost. Additionally, die casting facilitates high-volume production, making it a cost-effective choice for the automotive industry.
Conclusion
Die casting plays a vital role in the automotive industry, enabling the efficient production of high-quality and intricately designed components. From engine parts to structural and electrical components, die casting offers numerous advantages, including the ability to manufacture complex shapes, lightweight structures, and precise tolerances. By leveraging the capabilities of die casting, the automotive industry can achieve improved performance, fuel efficiency, and overall quality in vehicles.
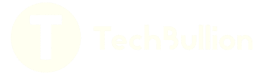