Introduction: What is Welding?
Have you ever wondered what is welding and why is it so essential to modern manufacturing? At its core, welding is the process of joining materials, typically metals or thermoplastics, by applying heat, pressure, or a combination of both to create a seamless bond. This seemingly straightforward process is the foundation of countless industries, particularly automotive manufacturing, where durability, precision, and efficiency are paramount.
In the automotive world, welding is vital for constructing everything from lightweight electric vehicles to robust high-strength steel frames. It ensures safety and structural integrity while accommodating modern demands for efficiency and sustainability. As technology advances, welding has evolved into a sophisticated practice that incorporates robotics, artificial intelligence, and advanced materials, redefining the possibilities of what vehicles can achieve.
Welding in Automotive Manufacturing
The automotive industry relies heavily on welding to create vehicles that are not only safe but also durable, efficient, and aesthetically appealing. With the increasing complexity of modern vehicles, welding has adapted to meet new challenges, especially with the widespread use of advanced materials and the rise of electric vehicles (EVs).
Key Applications in Automotive Welding
- Body-in-White (BIW):
The BIW phase involves constructing the vehicle’s basic frame before painting and assembly. Spot welding is the go-to technique here, with robotic arms performing thousands of welds in rapid succession to create a strong and consistent structure.
- Chassis and Suspension Components:
For critical load-bearing parts like the chassis and suspension, techniques like MIG (Metal Inert Gas) and TIG (Tungsten Inert Gas) welding are preferred. These methods provide the precision and strength required to handle the stresses these components endure.
- Electric Vehicles (EVs):
EV manufacturing introduces new challenges, particularly with battery packs and powertrains. Welding plays a critical role in ensuring the structural safety of these components, as well as effective thermal management to prevent overheating.
Material Innovations in Automotive Welding
Modern vehicles demand materials that are lightweight yet robust to improve fuel efficiency and safety. This shift has led to the adoption of advanced high-strength steels (AHSS), aluminum alloys, and composites. However, these materials often have differing thermal and mechanical properties, making traditional welding techniques less effective.
Innovations like laser welding and friction stir welding have emerged to address these challenges, enabling seamless joints in even the most complex material combinations. The ability to join dissimilar materials has become especially critical with the rise of multi-material car designs aimed at achieving optimal weight and strength ratios.
Welding’s central role in automotive manufacturing is evident, from forming the vehicle’s skeleton to assembling intricate components. As vehicles continue to evolve, welding technologies must stay ahead, ensuring they meet the ever-growing demands for efficiency, safety, and innovation.
Advanced Welding Techniques in the Automotive Industry
Now that you know what is welding and where it is used, let us dive into the details of some advanced welding techniques. As the automotive industry grows increasingly complex, traditional welding methods alone can no longer meet the demands for precision, speed, and versatility. Advanced welding techniques have emerged as indispensable solutions, enabling manufacturers to join modern materials, streamline processes, and create innovative designs that push the boundaries of engineering.
1. Laser Welding
Laser welding is revolutionizing automotive manufacturing with its ability to deliver unmatched precision and speed. This method uses concentrated laser beams to create narrow, deep welds with minimal heat input, reducing distortion and ensuring clean finishes. It is particularly effective for lightweight materials like aluminum and for joining intricate components in electric vehicles, such as battery housings and motor assemblies.
2. Friction Stir Welding (FSW)
Friction stir welding is a solid-state process that joins materials without melting them. A rotating tool generates frictional heat to soften the material, which is then mechanically stirred to form a joint. This technique is especially suited for aluminum alloys, making it ideal for lightweight vehicle structures. Its ability to produce high-strength welds with excellent fatigue resistance is critical in applications like EV battery enclosures and body panels.
3. Robotic Welding
Automation has brought a new level of efficiency and consistency to automotive welding. Robotic welding systems, guided by advanced software and sensors, ensure uniform welds even in high-speed production environments. These systems are increasingly equipped with artificial intelligence (AI), allowing them to adapt to variations in joint geometry and improve quality assurance in real-time.
4. Hybrid Welding
Hybrid welding combines laser welding with traditional arc welding, offering the best of both worlds. The laser component provides speed and precision, while the arc adds strength and flexibility. This technique is particularly valuable for thicker materials and complex assemblies, making it a versatile choice for diverse automotive applications.
5. Resistance Spot Welding (RSW)
While not new, resistance spot welding remains a staple in automotive manufacturing, particularly in Body-in-White (BIW) assembly. Advances in RSW technology, including better control systems and improved electrode designs, have made it more efficient and reliable than ever.
Why Advanced Techniques Matter
The adoption of these advanced welding methods is driven by the need to balance efficiency, quality, and cost-effectiveness in an industry where precision and innovation are paramount. These techniques enable manufacturers to work with cutting-edge materials, meet stricter safety standards, and optimize production for the growing demand for lightweight, fuel-efficient, and electric vehicles. As automotive designs become more complex, advanced welding processes will remain critical to achieving the perfect union of form and function.
Role of Advanced Technologies in Welding
The integration of advanced technologies has significantly transformed the welding process, particularly in the automotive industry. Innovations like artificial intelligence (AI), machine learning (ML), digital twins, augmented reality (AR), and sustainable practices are revolutionizing how welding is performed, improving everything from precision and efficiency to safety and environmental impact.
1. Artificial Intelligence (AI) and Machine Learning (ML)
AI and machine learning are reshaping welding by enabling real-time adjustments and predictive capabilities. AI-driven welding systems can monitor the welding process, adjusting variables such as heat, speed, and pressure to maintain optimal weld quality. Machine learning algorithms learn from past welding data, allowing systems to predict potential issues and optimize welding parameters without human intervention. This not only reduces the risk of defects but also enhances overall production efficiency, making it ideal for high-volume manufacturing.
AI’s impact extends beyond the welding process itself. Predictive maintenance powered by machine learning helps anticipate equipment failures, reducing downtime and improving the longevity of welding machines. By continually learning from historical data, AI ensures that welding operations run smoothly and cost-effectively, particularly in high-stakes automotive applications.
2. Digital Twins
A digital twin is a virtual replica of a physical system or process. In welding, digital twins are used to simulate and optimize welding techniques before they are implemented in production. Manufacturers can test different parameters, materials, and welding methods virtually, ensuring that the final product meets quality standards without the risk of trial and error on the production floor. This leads to better resource utilization, faster development cycles, and reduced waste.
Digital twins also enable manufacturers to monitor the performance of welding machines in real time, allowing for continuous improvements and adjustments to maintain high-quality standards. This innovation is particularly valuable in the automotive industry, where precision and consistency are crucial.
3. Augmented Reality (AR) for Training and Assistance
Welding requires high levels of skill, and training new welders can be both time-consuming and costly. Augmented reality (AR) has emerged as a powerful tool to enhance training programs by providing immersive, hands-on learning experiences. AR tools can overlay digital instructions on the physical workspace, guiding trainees step by step through the welding process. This can improve safety, reduce errors, and accelerate the learning curve for novice welders.
In addition to training, AR is used in the automotive industry for real-time assistance during the welding process. Workers equipped with AR headsets can receive on-the-job guidance, improving accuracy and reducing mistakes. AR can also be used for remote support, allowing experts to provide assistance from a distance, which is especially beneficial in complex or hazardous tasks.
4. Sustainability Innovations
As environmental concerns grow, sustainability has become a key focus in the automotive industry, and welding technology is no exception. New welding techniques, such as cold metal transfer (CMT) and other low-energy processes, are helping to reduce energy consumption while still delivering high-quality welds. These processes minimize heat input, which not only reduces energy use but also prevents material distortion, leading to higher quality and less waste.
Additionally, innovations in welding materials and processes are helping to reduce the environmental impact of automotive manufacturing. For instance, more sustainable welding wires, eco-friendly shielding gases, and recyclable welding consumables are being developed to minimize the carbon footprint of the welding process. As the industry moves toward electric vehicles (EVs) and greener manufacturing practices, sustainable welding technologies will play a key role in achieving these goals.
Conclusion
The integration of AI, machine learning, digital twins, augmented reality, and sustainable welding practices marks a new era for the automotive industry. These advanced technologies not only enhance the quality and efficiency of welding but also contribute to the overall evolution of the manufacturing process. As automotive designs become more complex and environmental concerns take center stage, the continued innovation in welding technologies will ensure that the industry remains at the forefront of both performance and sustainability.
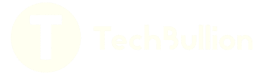