Pressure die casting is known as a manufacturing process in which molten metal (including Zinc, copper, aluminum, etc.) is injected into a mold cavity under certain pressure. The molten metal quickly solidifies to form a complex-shaped part with high accuracy and consistency. Die casting has wide-ranging applications in various industries. Whether you want to manufacture parts for automotive, aerospace, electronics, medical equipment, or any other consumer goods industry, die casting is a way to go. This article will introduce and compare the two types of die casting for you to further understand this versatile processing method.
What Are High Pressure and Low Pressure Die Casting?
Die casting has two types: High-Pressure die casting (HPDC) and Low-Pressure die casting (LPDC). The main difference between the two methods lies in the pressure used and how molten metal is introduced into the die.
High-pressure die casting involves injecting molten metal at high pressure, typically into a steel mold or die cavity. High pressure is necessary to quickly and accurately fill the mold cavity and solidify the molten metal in seconds. HPDC is commonly used for producing small to medium-sized parts with not-so-complex shapes and high dimensional accuracy, such as automotive engine components, housings for consumer electronics, and medical device components.
On the other hand, low-pressure die casting involves introducing molten metal into a partially evacuated die cavity through a refractory tube or riser. The pressure used is much lower, and the molten metal is introduced in a controlled manner, allowing for a slower and more even filling of the mold cavity.
High Vs. Low-pressure Die Casting
Here are some of the top differences in high and low-pressure die castings:
- Liquid Flowing Speed: In high-pressure casting, the flow speed of metal liquid can be as fast as 60 m/sec. However, this speed is reduced to 150mm/sec in low-pressure casting.
- Mold Cavity Requirements: High-pressure casting requires high-quality material, usually made up of metal. But when you are using low-pressure casting, you can easily use a material like sand that can endure the applied pressure.
- Cavity Complexity: You can expect to fill complex cavities in low-pressure die casting, but high-pressure die casting cavities are primarily simple.
- Production Scale: Due to the complexity of the process, high-pressure die casting is mainly done in small batches, while low-pressure die casting can be done in bulk.
- Porosity: In porosity die casting, no porosity is present. But in high-pressure casting, porosity can be present, and you must follow specific requirements to make an airtight casting.
- Availability of Heat Treatment: Low-pressure die casting can be heat treated, but this is usually not the case in high-pressure die casting.
- Surface Smoothness: In the case of low-pressure casting, the surface smoothness of the casting is typically average. But the surface of the high-pressure casting is mostly smooth.
- Casting Cycle: The casting cycle is long in low-pressure casting, which slows down the production speed. However, production speed in high-pressure casting is fast, which means that the casting cycle is also short in this case.
- Finished Product Rate: Usually, you can expect to have a finished product rate of 80-95% in the case of low-pressure die casting. But in high-pressure casting, this rate drops to 60-90%.
- Cost: Due to easier operating conditions, the low-pressure casting process has a low cost. On the other hand, high-pressure casting can be cost-intensive.
Applications of High & Low-pressure Die Castings
Both high-pressure and low-pressure die casting has their own pros and cons. You can choose the process based on your needs. Some examples of both processes are listed below:
High-pressure die casting is best for:
- Automotive industry: The automotive industry is one of the most significant users of high-pressure die casting. It is used to produce a wide range of automotive parts, such as engine blocks, transmission cases, steering components, and suspension parts.
- Aerospace industry: It includes the production of aircraft engines, landing gear, and other components.
- Medical Equipment: High-pressure die casting is used to produce medical equipment such as surgical instruments, orthopedic implants, and dental devices.
Low-pressure die castings can be used in the following:
- Aerospace Industry: Low-pressure die casting is used in the production of structural parts for aircraft, including wing spars, wing ribs, and fuselage frames.
- Electrical Industry: It can be seen in the production of switchgear, electrical connectors, and motor housings.
- Lighting Industry: Some lighting components, such as lamp housings and reflectors, adopt this processing method.
Why HordRT
HordRT provides professional die-casting services to solve your manufacturing problems. They employ a wide variety of materials for pressure casting purposes based on your production needs. They are famous for maintaining high-quality products without compromising on cost. Since they do not require any MOQ (Minimum Order Quantity), they are fit for many business needs.
Wrapping Up
Established in 2013, HordRT is a professional rapid tooling manufacturer. They provide efficient services in pressure die casting, CNC machining, plastic injection molding, aluminum extrusion, and silicone heat compression. Their ability to provide efficient services stands them out of the crowd. Contact them for the smoothest rapid tooling services!
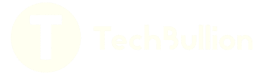