Printed Circuit Boards (PCBs) are the backbone of modern electronics, providing the connectivity and organization of components essential for electronic devices. As technology advances and electronic components become more powerful and compact, the issue of thermal management in PCB design has become increasingly critical. The heat generated during the operation of electronic components can lead to reduced performance, decreased lifespan, and even catastrophic failures if not managed effectively.
-
Component Placement
One of the fundamental thermal management strategies is the components’ strategic placement on the PCB. Components that generate significant heat, such as processors and power amplifiers, should be located in areas with good heat dissipation. Placing these heat-generating components near the PCB’s edge can allow for more efficient heat transfer to the surroundings. Additionally, arranging components to minimize heat buildup between them can also help reduce thermal issues.
-
Heat Sinks
Heat sinks are common solutions for dissipating heat generated by electronic components. These passive devices are designed to absorb and spread heat away from components and come in various shapes and sizes. Heat sinks are often attached to hot components, such as CPUs and voltage regulators, using thermal paste or pads to ensure efficient heat transfer. Proper selection and sizing of heat sinks are crucial for effective thermal management.
-
Thermal Vias
Thermal vias are small holes in the PCB that help conduct heat away from the board’s surface and into inner layers. The heat can be dissipated more effectively by connecting the component’s thermal pad to these vias. Careful consideration of thermal vias’ number, size, and placement is essential to optimize heat transfer. Multiple vias can form a thermal path to carry heat to an outer layer of the PCB, where it can be dissipated through a heat sink or the PCB itself.
-
Copper Pour
Copper is an excellent thermal conductor, and using copper pour techniques can help distribute and dissipate heat across the PCB. A solid copper plane on one or more PCB layers can be a heat spreader, efficiently carrying heat away from hotspots. By strategically designing copper pours around critical components, designers can ensure that heat is evenly distributed, reducing the risk of localized overheating.
-
Active Cooling Solutions
Active cooling solutions such as fans, heat pipes, and Peltier coolers can be employed when passive cooling methods are insufficient. Fans are commonly used to increase airflow and enhance heat dissipation. Heat pipes use phase-change principles to transport heat efficiently, making them a viable solution for some applications. Peltier coolers are thermoelectric devices that heat and cool, allowing precise temperature control.
-
Thermal Analysis and Simulation
Before finalizing PCB design tools, thermal analysis and simulation are invaluable tools for assessing and optimizing thermal performance. Using specialized software, designers can model the behavior of heat within the PCB and identify potential hotspots. This analysis helps make informed decisions regarding component placement, heat sink design, and thermal management strategies.
-
Material Selection
The choice of PCB materials can significantly impact thermal management. Materials with high thermal conductivity, such as metal-core PCBs, are better suited for applications with stringent thermal requirements. The selection of the right material should be based on the design’s specific needs, considering factors like cost, weight, and electrical properties.
-
Adequate Power Distribution
Efficient power distribution can also contribute to better thermal management. The risk of overheating due to voltage fluctuations can be minimized by ensuring that components receive stable and regulated power. Properly designed power planes and voltage regulation circuits can help maintain consistent operating conditions for components.
In conclusion, effective thermal management is crucial for ensuring the reliability and performance of electronic devices. By implementing strategies such as component placement, heat sinks, thermal vias, copper pours, active cooling solutions, thermal analysis, material selection, and power distribution, PCB designers can mitigate the risk of overheating and thermal-induced failures. As technology advances, the demand for innovative thermal management solutions will persist, driving further research and development in this critical aspect of PCB design.
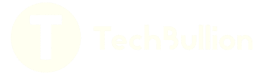