Introduction to Custom Circuit Board Design
Custom circuit board design is an essential skill for anyone interested in electronics and electrical engineering. Whether you’re a hobbyist, a student, or a professional, understanding the basics of circuit board design can help you create more efficient, reliable, and cost-effective electronic devices. In this comprehensive guide, we’ll walk you through the fundamentals of custom circuit board design, from the initial concept to the final product.
What is a Custom Circuit Board?
A custom circuit board, also known as a printed circuit board (PCB), is a specially designed board that connects electronic components using conductive tracks, pads, and other features. Unlike generic circuit boards, custom circuit boards are tailored to meet specific requirements, such as size, shape, and functionality. This allows for greater flexibility and optimization in the design process.
Advantages of Custom Circuit Boards
Custom circuit boards offer several advantages over generic boards, including:
- Improved performance and reliability
- Reduced size and weight
- Lower manufacturing costs for large quantities
- Increased design flexibility and customization
Types of Custom Circuit Boards
There are several types of custom circuit boards, each with its own unique characteristics and applications: - Single-layer PCBs: These boards have conductive tracks on only one side and are suitable for simple, low-density designs.
- Double-layer PCBs: With conductive tracks on both sides, double-layer PCBs offer more design flexibility and higher component density than single-layer boards.
- Multi-layer PCBs: These boards have multiple layers of conductive tracks, allowing for even greater design complexity and component density.
- Flexible PCBs: Made from flexible materials, these boards can bend and conform to various shapes, making them ideal for applications with limited space or unusual geometries.
- Rigid-flex PCBs: A combination of rigid and flexible sections, these boards offer the best of both worlds, providing stability and flexibility where needed.
The Custom Circuit Board Design Process
Step 1: Concept and Schematic Design
The first step in custom circuit board design is to develop a concept and create a schematic diagram. This involves defining the board’s purpose, identifying the required components, and determining how they will be interconnected. Schematic design software, such as Eagle or KiCad, can help you create a visual representation of your circuit and catch potential errors early in the design process.
Step 2: Component Selection and Placement
Once you have a schematic, the next step is to select the appropriate components and determine their placement on the board. This involves considering factors such as component size, power requirements, and signal integrity. Component placement software can help you optimize the layout for manufacturing and assembly.
Step 3: Routing and Trace Design
After placing the components, you’ll need to design the conductive tracks (traces) that connect them. This involves determining the appropriate trace width, spacing, and layer assignment to ensure proper signal integrity and minimize interference. Routing software can automate much of this process, but it’s essential to understand the underlying principles to create an optimal design.
Step 4: Design Rule Check (DRC) and Verification
Before finalizing your design, it’s crucial to perform a design rule check (DRC) to ensure that your board meets all manufacturing and assembly requirements. This includes checking for minimum trace widths, spacing, and drill sizes, as well as verifying that all components are properly connected. Many PCB design software packages include built-in DRC tools to help you catch and correct errors.
Step 5: Prototyping and Testing
After verifying your design, it’s time to create a prototype and test its functionality. This involves generating Gerber files (the industry standard format for PCB manufacturing) and sending them to a PCB fabrication service. Once you receive your prototype boards, you can assemble the components and test the circuit to ensure it performs as expected.
Step 6: Iteration and Optimization
Based on the results of your prototype testing, you may need to iterate and optimize your design. This could involve adjusting component values, modifying trace routing, or even redesigning certain sections of the board. It’s essential to document any changes and maintain version control throughout the iteration process.
PCB Material Selection
Choosing the right material for your custom circuit board is critical to its performance and longevity. The most common PCB materials are:
- FR-4: A glass-reinforced epoxy laminate, FR-4 is the most widely used PCB material due to its low cost, good mechanical properties, and reasonable dielectric constant.
- High-frequency laminates: For applications requiring higher frequencies or lower dielectric constants, materials such as Rogers RO4000 series or Isola IS410 may be used.
- Metal core PCBs: These boards have a metal core (usually aluminum) to improve heat dissipation, making them ideal for high-power applications.
- Flexible materials: Polyimide and polyester are common materials for flexible PCBs, offering high flexibility and durability.
PCB Layer Stackup
The layer stackup of a custom circuit board refers to the arrangement of conductive and insulating layers. Proper layer stackup design is essential for signal integrity, power distribution, and manufacturability. Some key considerations include:
- Signal layer arrangement: Alternating signal layers with ground or power planes can help minimize crosstalk and improve signal integrity.
- Power and ground plane placement: Dedicating entire layers to power and ground planes can reduce impedance and improve power distribution.
- Dielectric thickness: The thickness of the insulating layers between conductive layers affects impedance and signal propagation, and must be carefully chosen based on the application.
Signal Integrity and Electromagnetic Compatibility (EMC)
Ensuring signal integrity and electromagnetic compatibility (EMC) is crucial for the proper functioning of your custom circuit board. Some key strategies include:
- Impedance control: Matching the impedance of traces to the source and load impedances can help minimize reflections and improve signal quality.
- Crosstalk reduction: Proper trace spacing, routing, and layer arrangement can help minimize crosstalk between adjacent signals.
- EMI reduction: Techniques such as shielding, filtering, and proper grounding can help reduce electromagnetic interference (EMI) and ensure compliance with EMC regulations.
Thermal Management
Proper thermal management is essential for the reliability and longevity of your custom circuit board. Some key strategies include:
- Copper pour: Adding large areas of copper on the board can help dissipate heat from components.
- Thermal vias: Placing vias (conductive holes) near high-power components can help transfer heat to other layers or to a heatsink.
- Airflow and cooling: Ensuring adequate airflow around the board and using heatsinks or fans can help dissipate heat and prevent overheating.
Documentation and Version Control
Maintaining accurate documentation and version control throughout the custom circuit board design process is essential for collaboration, troubleshooting, and future revisions. Some key practices include:
- Schematic and layout version control: Use a version control system, such as Git, to track changes to your schematic and layout files.
- Bill of Materials (BOM): Maintain an up-to-date BOM that lists all components, their quantities, and their specifications.
- Assembly instructions: Provide clear and detailed assembly instructions, including component placement, orientation, and any special handling requirements.
Manufacturability and Assembly Considerations
Designing your custom circuit board with manufacturability and assembly in mind can help reduce costs, improve reliability, and accelerate time to market. Some key considerations include:
- Design for Manufacturing (DFM): Follow DFM guidelines, such as minimum trace widths, spacing, and drill sizes, to ensure your board can be reliably manufactured.
- Design for Assembly (DFA): Consider component placement, orientation, and spacing to facilitate automated assembly processes and minimize the risk of errors.
- Panelization: Group multiple boards into a single panel to optimize manufacturing efficiency and reduce costs.
Testing and Quality Control
Thorough testing and quality control are essential to ensure the reliability and performance of your custom circuit board. Some key strategies include:
- In-circuit testing (ICT): Use automated ICT equipment to verify the presence, orientation, and value of components on the assembled board.
- Functional testing: Perform functional tests to ensure that the board performs as expected under various operating conditions.
- Environmental testing: Conduct environmental tests, such as temperature cycling and vibration testing, to ensure the board can withstand its intended operating environment.
Choosing a PCB Manufacturer
Selecting the right PCB manufacturer is crucial to the success of your custom circuit board project. Some key factors to consider include:
- Capabilities: Ensure that the manufacturer has the necessary equipment, expertise, and certifications to produce your board to your specifications.
- Quality: Look for manufacturers with a proven track record of producing high-quality boards and a commitment to continuous improvement.
- Communication and support: Choose a manufacturer that is responsive, communicative, and willing to work with you to resolve any
Read More From Techbullion And Businesnewswire.com
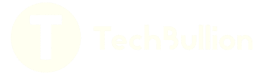