Metal Injection Molding (MIM) is transforming the manufacturing landscape in India. This advanced technique combines the benefits of metalworking and plastic injection molding. It creates high-strength, complex metal parts quickly and efficiently. Businesses across India are turning to MIM to reduce production costs and save valuable time. In this article, we explore how Metal Injection Molding in India is revolutionizing industries by cutting costs and speeding up production.
What is Metal Injection Molding?
Metal Injection Molding is a process that involves mixing fine metal powders with a binder material. This mixture is injected into a mold, just like plastic molding. After molding, the binder is removed, and the metal part is sintered in a furnace to achieve its final strength.
MIM is widely used in industries such as automotive, aerospace, medical, electronics, and more. It allows manufacturers to produce complex shapes with tight tolerances that would be difficult to achieve through traditional metalworking methods.
Why Choose Metal Injection Molding in India?
India is becoming a global hub for manufacturing, and MIM is a key contributor to this growth. Companies in India are adopting MIM to stay competitive in the global market. Here are the key reasons why businesses prefer MIM in India:
- Cost-Effective Production
- Fast Turnaround Time
- High-Quality Precision Parts
- Eco-Friendly Manufacturing
Let’s dive deeper into how these benefits translate into cost savings and time efficiency.
1. Cost-Effective Production
One of the biggest advantages of Metal Injection Molding is cost reduction. Traditional metalworking processes involve machining, casting, or forging, which can be expensive and time-consuming. MIM eliminates many of these steps.
How MIM Cuts Costs:
- Reduced Material Waste: MIM uses only the necessary amount of material, minimizing waste.
- Lower Labour Costs: The process is automated, reducing the need for manual labor.
- No Secondary Operations: MIM parts often require little to no additional machining, saving time and money.
By adopting MIM, manufacturers in India can produce high-quality parts at a fraction of the cost of traditional methods. This makes it ideal for mass production.
2. Fast Turnaround Time
In today’s competitive market, time is money. Businesses need to deliver products quickly to meet customer demands. MIM helps achieve this by speeding up the production process.
How MIM Saves Time:
- Automated Process: The automated nature of MIM reduces production time compared to manual metalworking.
- Quick Setup: MIM requires less setup time, especially for complex parts.
- Batch Production: MIM is perfect for producing large quantities of parts in a short period.
With faster production cycles, companies can bring their products to market sooner. This is a major advantage in industries like automotive and electronics, where product lifecycles are short.
3. High-Quality Precision Parts
MIM allows for the production of intricate and precise parts that meet strict quality standards. Traditional metalworking methods may struggle with complex geometries, but MIM handles them with ease.
Quality Benefits:
- Complex Shapes: MIM can produce parts with complex shapes that would be difficult to achieve through other methods.
- Tight Tolerances: The process ensures that parts meet exact specifications, reducing the need for adjustments.
- Consistent Quality: MIM provides consistent quality across large production runs.
Producing high-quality parts quickly means fewer rejections and less time spent on quality control. This leads to further cost and time savings.
4. Eco-Friendly Manufacturing
Sustainability is a growing concern for businesses worldwide. MIM is a more environmentally friendly option compared to traditional metalworking.
Eco-Friendly Advantages:
- Reduced Waste: MIM produces minimal waste compared to machining.
- Energy Efficiency: The process consumes less energy than many traditional methods.
- Reusable Materials: Excess materials can be reused, reducing costs and environmental impact.
By adopting MIM, companies in India can reduce their carbon footprint while also saving money.
Industries Benefiting from Metal Injection Molding in India
Several industries in India are leveraging the benefits of MIM to improve their operations. Here are some key sectors:
- Automotive: Producing lightweight, high-strength parts.
- Medical: Manufacturing precise surgical tools and implants.
- Electronics: Creating small, intricate components.
- Aerospace: Producing complex parts for aircraft and spacecraft.
These industries require precision, speed, and cost-efficiency, making MIM an ideal choice.
Challenges and Solutions in Metal Injection Molding
While MIM offers many benefits, it also comes with challenges. However, manufacturers in India are finding ways to overcome them.
Common Challenges:
- High Initial Investment: The initial setup cost can be high.
- Binder Removal Process: Removing the binder can be tricky.
Solutions:
- Government Support: The Indian government offers incentives for advanced manufacturing technologies.
- Technological Advancements: New techniques are making the MIM process more efficient.
Conclusion
Metal Injection Molding in India is changing the manufacturing game. It offers cost-effective production, fast turnaround times, high-quality parts, and eco-friendly benefits. By adopting MIM, businesses can stay competitive in the global market while reducing costs and saving time.
As more industries discover the advantages of MIM, it’s clear that this technology will play a significant role in India’s manufacturing future.
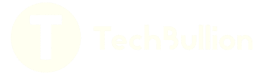