Introduction:
injection shaping is an essential assembling process known for its accuracy and Generation. This guide investigates the four vital phases of injection shaping, featuring its importance in current creation. As businesses advance, the requirement for financially savvy production processes develops.injection molding process has become fundamental for delivering unpredictable parts with negligible material waste, serving different areas from auto to shoppers’ gadgets. Understanding the injection-shaped interaction requires knowledge in its mind-boggling stages, each critical for accomplishing ideal outcomes. From clipping to discharge, meticulousness and trend-setting innovation are fundamental for faultless execution. With the ascent of Industry 4.0 innovations, for example, computerised reasoning and IoT coordination, injection shaping has seen critical progressions, improving its accuracy and proficiency.
Clamping:
The injection molding process excursion starts with clipping, an important stage where molds are safely situated to endure the afflictions of assembling. Accuracy rules here, with even minor misalignments gambling with the uprightness of the end result. State of the art innovation, including CNC hardware and progressed bracing components, works with exact shape arrangement and fixing. Past apparatus, talented professionals carefully screen the interaction, guaranteeing ideal execution customised to different venture needs. This versatile methodology ensures solidness and accuracy, recognizing makers as trust accomplices ininjection molding process arrangements. In the present cutthroat saving scene, the clasping stage fills in as the bedrock of fruitful injection molding process tasks. With headways in CNC hardware and mechanical technology, makers can accomplish exceptional degrees of accuracy and repeatability in shape bracing, limiting the gamble of deformities and guaranteeing steady part quality. Additionally, the incorporation of constant checking frameworks takes into consideration proactive changes, further upgrading the effectiveness and unwavering quality of the bracing system. Moreover, the flexibility of clipping methods assumes a pivotal part in obliging the different prerequisites of present day fabricating projects. Whether it’s high-volume creation runs or custom models, makers should fit their clipping methodologies to suit the particular requirements of each venture. This adaptability improves productivity as well as empowers makers to convey redid arrangements that meet or surpass client assumptions. Past guaranteeing part uprightness, the clipping stage additionally holds suggestions for in general creation productivity and cost-adequacy. By streamlining bracing boundaries like strain, speed, and power dissemination, makers can limit process durations and expand throughput, at last decreasing creation costs and upgrading seriousness at the lookout. Moreover, the utilisation of energy-proficient clipping frameworks adds to maintainability endeavors, lining up with the developing interest for eco-accommodating assembling rehearsals. In outline, the clasping stage fills in as the foundation of effective injection molding process activities, establishing the groundwork for accuracy, productivity, and unwavering quality all through the assembling system. By utilizing state-of-the-art innovation, versatile systems, and a guarantee to greatness, makers can hoist their injection molding process capacities, situating themselves as pioneers in the business.
Injection:
Accuracy Designing in Real Life Subsequent to clipping, the injection stage starts, infusing liquid material into the shape cavity under high tension. Accuracy designing and control are basic to accomplish uniform material dispersion and forestall absconds. Intensive investigation of material properties and shape configuration illuminates the interaction, directing exact control of injection boundaries. Cutting edge apparatus with cutting edge control frameworks guarantees trustworthy part arrangement and efficiency. Today, the injection stage addresses a basic point where accuracy and innovation meet. With complex part calculations and materials, imaginative methodologies guarantee uniform conveyance and deformity relief. Understanding material ways of behaving and form improvement alleviate difficulties like stream limitations and upgrading part quality. High level apparatus empowers fastidious command over injection boundaries, guaranteeing that part quality norms are met reliably. Embracing progressive shaping strategies extends makers’ capacities, offering inventive answers for different ventures’ requirements.
Cooling:
Guaranteeing Ideal Quality and Execution After the injection stage, the basic cooling stage follows, where the formed material goes through the essential course of cementing to achieve the ideal shape. Accuracy cooling arises as a foundation in this stage, essential for moderating imperfections, for example, distorting or shrinkage that could think twice about uprightness of the eventual outcome. Utilizing progressed cooling methodologies and best-in-class temperature control frameworks, producers maintain predictable cooling conditions across the sum of the part, in this way limiting the likelihood of imperfections and ensuring layered exactness. Besides, the usage of inventive cooling procedures, for example, conformal cooling and quick cooling strategies, improves cooling proficiency and speeds up process durations, advancing generally speaking creation throughput. These high level cooling procedures guarantee uniform cooling conveyance, which is especially profitable for unpredictable parts with fluctuating thicknesses, bringing about better part quality and decreased creation costs.
Opening and Launch:
Smoothing out Tasks for Consistent Outcomes As the injection forming process moves toward its decision, the critical phases of shape opening and part launch become possibly the most important factors. Accuracy taking care of becomes basic during these last stages to forestall any harm to the parts or forms and to work with a consistent launch process. Utilizing progressed computerized launch frameworks and the aptitude of prepared experts, makers guarantee that parts are shot out without a hitch and productively, without any trace of any flaws. Additionally, ongoing checking and input components incorporated into the launch frameworks consider prompt changes in accordance with be made, guaranteeing reliable discharge powers, and limiting the gamble of part twisting or harm. Each shot out part goes through thorough examination conventions to check its quality and accuracy, supporting the obligation to convey perfect items to clients. Taking everything into account, the cooling and launch phases of the injection forming process exemplify the obligation to accuracy, effectiveness, and quality that makers endeavor to maintain. By saddling progressed cooling procedures and accuracy discharge frameworks, makers can streamline creation processes, upgrade part quality, and eventually convey predominant items that fulfill the thorough needs of present-day ventures.
Conclusion:
All in all, injection forming contains four fundamental stages, each requesting accuracy and fastidious meticulousness. Makers focus on strength, accuracy in designing, and severe quality control measures, laying out a norm of greatness in the business. The business’ devotion to natural maintainability is shown through drives like the utilization of biodegradable materials. At last, the injection forming area thrives through its obligation to accuracy, development, and a resolute quest for greatness.
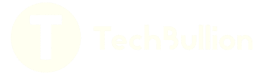