Injection moulding is a cornerstone of modern manufacturing, utilized to produce a vast array of products across various industries, from automotive components to consumer electronics. At the heart of this versatile process is the injection moulding machine (IMM), a sophisticated piece of equipment that shapes molten material into precise and complex parts. Understanding the basics of injection moulding machines is crucial for anyone involved in manufacturing or considering entering the industry. This comprehensive guide will explore the fundamentals of injection moulding machines, including their components, operation, types, and factors when selecting the right machine for your needs.
What is Injection Molding?
Injection moulding is a manufacturing process used to produce parts by injecting molten material into a mould. The material is typically a thermoplastic or thermosetting polymer, but other materials, such as metals and glass, can also be used. The process involves several key steps:
- Melting: The material is heated until it becomes molten.
- Injection: The molten material is injected into a mould cavity under high pressure.
- Cooling: The material cools and solidifies in the mould, taking the shape of the cavity.
- Ejection: The solidified part is ejected from the mould.
Injection moulding machines are designed to perform these steps efficiently and accurately, producing high-quality parts with tight tolerances and complex geometries.
Key Components of Injection Molding Machines
Injection moulding machines comprise several critical components, each playing a specific role in the moulding process. Understanding these components helps grasp the machine’s operations and the factors influencing its performance.
Injection Unit
The injection unit is responsible for melting and injecting the material into the mould. Key parts of the injection unit include:
- Hopper: The hopper is where the raw material (in pellet form) is loaded into the machine. It feeds the material into the barrel for melting.
- Barrel: The barrel is a heated chamber where the material is melted. It typically contains a heating element and a rotating screw.
- Screw: The screw, which rotates within the barrel, mixes and melts the material. It also helps to inject the molten material into the mould.
- Nozzle: The nozzle ends the injection unit, where the molten material exits the barrel and enters the mould.
Clamping Unit
The clamping unit holds the mould in place during injection and opens and closes it for part ejection. Key components of the clamping unit include:
- Clamping Mechanism: This mechanism provides the force to keep the mould closed during the injection. It can be hydraulic, mechanical, or electric.
- Mould Platens: Mold platens are the large, flat surfaces that support the mould and are part of the clamping unit. They provide stability and alignment.
Mould
The mould is a crucial component that determines the shape and detail of the final part. It consists of two halves:
- Cavity: The cavity is the interior part of the mould that forms the shape of the part.
- Core: The core is the exterior part of the mould that fits with the cavity to form the complete mould assembly.
Control System
The control system manages the operation of the injection moulding machine, including temperature, pressure, and timing. Modern machines often feature advanced control systems with:
- Touchscreen Interfaces: Allow for easy input and monitoring of machine parameters.
- Programmable Settings: Enable the storage and recall of specific moulding recipes and settings.
Types of Injection Molding Machines
Injection moulding machines come in various types, each designed to meet specific manufacturing needs. The primary types include:
Hydraulic Injection Molding Machines
Hydraulic injection moulding machines use hydraulic pressure to operate the clamping and injection units. They are known for their robustness and ability to handle large, complex moulds. Key characteristics include:
- High Clamping Force: Suitable for large and heavy moulds.
- Versatility: Can handle a wide range of materials and part sizes.
- Power Consumption: Typically less energy-efficient compared to other types.
Electric Injection Molding Machines
Electric injection moulding machines use electric motors to drive the clamping and injection units. They offer precise control and energy efficiency. Key characteristics include:
- Energy Efficiency: Lower power consumption compared to hydraulic machines.
- Precision: Provides accurate control over the moulding process.
- Lower Noise Levels: Quieter operation due to electric motors.
Hybrid Injection Molding Machines
Hybrid injection moulding machines combine hydraulic and electric technologies to benefit from both. They offer:
- Energy Efficiency: Improved energy efficiency compared to traditional hydraulic machines.
- Precision and Speed: Enhanced precision and faster cycle times.
- Flexibility: Suitable for a wide range of applications and materials.
Factors to Consider When Choosing an Injection Molding Machine
Selecting the right injection moulding machine involves evaluating several factors to ensure it meets your manufacturing requirements. Key considerations include:
Clamping Force
The clamping force is the amount of force required to keep the mould closed during the injection. It is crucial to determine the size and complexity of the moulds that the machine can handle. Larger parts and moulds require higher clamping forces.
Injection Capacity
The injection capacity refers to the amount of material the machine can inject per cycle. Choosing a machine with adequate injection capacity is important to meet production and part size requirements.
Material Compatibility
Different machines are designed to handle various materials, including thermoplastics, thermosets, and composites. Ensure that the machine you choose is compatible with the materials you plan to use.
Cycle Time
Cycle time is the total time required to complete one moulding cycle, including injection, cooling, and ejection. Shorter cycle times can improve production efficiency and reduce costs.
Precision and Control
The precision and control offered by the machine impact the quality and consistency of the moulded parts. Look for machines with advanced control systems that provide precise temperature, pressure, and timing adjustments.
Energy Efficiency
Energy efficiency is an important consideration, especially for high-volume production. Machines with lower power consumption can reduce operating costs and contribute to environmental sustainability.
Maintenance and Service
Consider the ease of maintenance and service support availability when selecting a machine. Reliable maintenance and support can minimize downtime and ensure smooth operation.
Advantages of Injection Molding Machines
Injection moulding machines offer several advantages that make them a preferred choice for manufacturing high-quality parts:
High Production Efficiency
Injection moulding machines can produce large quantities of parts quickly and efficiently. This makes them ideal for high-volume production runs.
Consistency and Quality
The precise control over temperature, pressure, and timing ensures that each part is produced consistently and with dimensional accuracy.
Complex Geometries
Injection moulding machines can produce complex and intricate parts with high levels of detail, making them suitable for a wide range of applications.
Material Versatility
Injection moulding machines can handle a variety of materials, including plastics, metals, and composites, allowing for flexibility in product design and manufacturing.
To summarize, take a look
Injection moulding machines are a critical component of modern manufacturing, providing the precision, efficiency, and versatility needed to produce high-quality parts across various industries. Understanding the basics of these machines, including their components, types, and key considerations, is essential for making informed decisions and optimizing your manufacturing processes. Manufacturers can achieve consistent quality, meet production demands, and stay competitive in the ever-evolving market by selecting the right injection moulding machine and leveraging its capabilities.
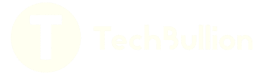