Understanding the Quality Control Process for All-Terrain Vehicles in North America
All-Terrain Vehicles (ATVs) have become a popular choice for adventurers and outdoor enthusiasts in North America, where the vast and exciting trail systems provide opportunities for thrilling off-road experiences. However, ensuring the safety and reliability of these vehicles is of paramount importance. This article explores the quality control process implemented by manufacturers to ensure ATVs meet safety standards.
The Importance of Safety in All-Terrain Vehicles
ATVs are unique vehicles designed for rugged terrains, featuring four wheels, handlebars for steering, and non-pneumatic or low-pressured tires. Due to their powerful engines and low-centered gravity, they lack conventional safety mechanisms such as seatbelts or airbags. Manufacturers must prioritize safety during production.
Addressing the Dangers
Recognizing the potential risks associated with ATV usage, regulatory bodies like the Consumer Product Safety Commission (CPSC) in North America have established stringent safety standards for manufacturers to follow. These standards aim to prevent accidents and protect riders from harm by addressing common causes of ATV-related fatalities, such as overturning and collisions.
The Consumer Product Safety Commission’s Role
The CPSC plays a vital role in setting and enforcing ATV safety standards. It collaborates with organizations like the Specialty Vehicle Institute of America (SVIA) to develop American National Standards for ATV manufacturing. Manufacturers are required to comply with these standards and provide supporting documentation to demonstrate adherence.
Setting Industry Standards
The ANSI/SVIA 1:2017 is the latest version of the SVIA ATV standards. These standards cover various aspects, including ATV design, configurations, parts performance, clutch and gear shift controls, suspension, speed capability, throttle, stability, lighting and tire requirements, sound levels, and more. Each component undergoes rigorous testing to ensure compliance and reliability.
The Importance of Metal Testing and the Role of Tensile Testing
Metal testing is critical to ensuring the quality, strength, and reliability of various metal components and structures. From manufacturing industries to construction projects, understanding metal mechanical properties is essential for safety and performance. Tensile testing is an important test of metals, which measures the material’s response to force.
Tensile testing involves subjecting a metal sample to controlled tension until it breaks. This test helps determine various mechanical properties such as yield strength, ultimate tensile strength, elongation, and modulus of elasticity. By analyzing these properties, manufacturers and engineers can evaluate the suitability of metals for specific applications, ensure compliance with industry standards, and assess structural integrity.
To perform accurate tensile testing, it is crucial to have specialized equipment like flat tensile test sample preparation machines. These machines offer precise and efficient sample preparation for tensile testing. They can precisely cut and shape metal samples to the required dimensions and ensure consistent specimen preparation, eliminating potential variations that may affect test results.
By utilizing flat tensile test sample preparation machines, manufacturers and testing laboratories can achieve increased accuracy, repeatability, and efficiency in their metal testing processes. These machines handle a wide range of metals, including steel, aluminum, copper, and more, accommodating various sample sizes and shapes.
The benefits of specialized equipment for metal testing, such as flat and round tensile specimen preparation machines, extend beyond precise sample preparation. These machines often incorporate advanced features like computer numerical control (CNC) technology, which allows for automated and programmable cutting and shaping processes. Automation saves time, increases productivity, and reduces human error risk, ensuring consistent and reliable test results.
Furthermore, specialized equipment offers enhanced safety measures, as they are designed to handle high forces involved in tensile testing. They provide secure clamping and gripping mechanisms, ensuring the stability of metal samples during testing and minimizing the risk of accidents or sample failure.
Vehicle Action Plan
Manufacturers and distributors are obligated to create a vehicle action plan, which outlines their commitment to ATV safety. This plan includes age recommendations, dealer monitoring, safety training, labeling, advertising guidelines, and proper operation guidelines. The CPSC reviews and approves these plans to ensure safety standards compliance.
Certifications and Compliance
Manufacturers must obtain certifications to demonstrate compliance with standards and regulations. This includes obtaining a General Conformity Certificate for ATVs manufactured overseas, indicating compliance with U.S. standards. Additionally, ATVs should bear labels certifying compliance with the CPSC-approved vehicle action plan.
Monitoring and Reporting
Manufacturers are responsible for continuously monitoring their compliance with safety standards and the approved vehicle action plan. This involves conducting onsite inspections, offering safety training courses, and ensuring dealers adhere to the guidelines. Compliance monitoring results must be reported to the CPSC biannually.
Importance of Safety Labels
Safety labels inform riders about age appropriateness, passenger capacity, tire pressure warnings, and other safety precautions. These labels are essential for compliance and help consumers make informed ATV usage decisions.
The quality control process for All-Terrain Vehicles in North America is a comprehensive and vital aspect of rider safety. Through safety standards, certification processes, and continuous monitoring, manufacturers strive to produce reliable and compliant ATVs. By adhering to these processes, manufacturers demonstrate their commitment to providing safe and enjoyable off-road experiences for ATV enthusiasts across North America.
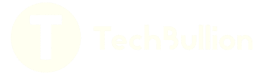