Tensile testing, often referred to as the determining test for material reliability, guarantees the robustness of every industrial product we encounter in our daily lives. Whether it’s the car we drive, the bridges we cross, or the equipment we use, the level of strength and durability comes from stringent testing methods, like tensile testing, employed during manufacturing.
Tension testing is a mechanical test where a material is stretched until it breaks. This test offers a detailed account of its strength, ductility, and ability to withstand stress and strain. Testing such materials is not only a scientific procedure but also a vital source of information that guides engineers and designers in choosing materials and ensuring they meet high quality and safety standards.
The important role of tension testing extends into every aspect of industrial manufacturing, ensuring that the materials used, whether metals, polymers, or composites, conform to specified standards and can withstand loads and stresses. Products manufactured conform to quality benchmarks, safeguarding consumer interests and elevating industrial standards globally.
The following sections will analyze the complex relationship between tensile testing and industrial manufacturing standards, examining the connection between global standards, manufacturing practices, and the achievement of material excellence through rigorous testing and innovation.
The Interconnection Between Tensile Testing and Manufacturing Standards
Tensile testing provides a rich repository of data essential for setting and validating manufacturing standards. This safeguards products’ integrity, safety, and durability across numerous industries. It is crucial to comprehend that manufacturing standards are deeply intertwined with insights derived from rigorous material testing. This understanding, underscored by tensile tests, reveals materials’ behavior under different stress conditions, ensuring functionality and reliability in real-world applications.
Manufacturing standards, such as those developed by global entities like ISO, necessitate a robust, data-driven framework to assure universal adherence to quality and safety benchmarks. These standards, synthesized from extensive material testing data, provide a comprehensive method to ensure that materials and products, regardless of their origin, satisfy a global measure of reliability and effectiveness.
Therefore, tensile testing becomes a crucial component of the establishment, validation, and evolution of manufacturing standards, ensuring that materials are not only compliant with but also potentially exceed these benchmarks. As a result of maintaining a uniform quality standard across borders, every material used and every product manufactured is subject to a rigorous, universally accepted norm, reinforcing consumer trust and facilitating international trade. A symbiotic relationship between tension testing and manufacturing standards supports and propels the global manufacturing industry toward higher levels of quality assurance and consumer safety.
Practical Implications of Tensile Testing in Industry
Putting the test of tensile strength into practice in industries helps to guarantee that the things we use and rely on daily are safe and dependable. Think about the wide variety of products around us – cars, bridges, machines, and even simple household items. Each of these things is made of materials that need to be strong and reliable, and that’s where the tensile test comes in.
When industries make something, they want to know it won’t break easily. To achieve this, they need to understand the strengths and weaknesses of the materials they use. So, they pull, stretch, and bend materials, testing them with the help of the special testing equipment, to see when and how they fail. This isn’t just about avoiding breaks. It’s also about understanding how to use materials most effectively and economically in creating durable products.
Testing for tensile strength helps industries pick the right materials and use them in a way that provides assurance that our vehicles, buildings, appliances, and more are safe. This provides peace of mind that they will last a long time. The practical application of tensile test, therefore, plays a significant role in maintaining quality, ensuring safety, and promoting trust among consumers in the range of products they use daily. We rely on this simple but impactful testing process to ensure the reliability of the myriad of materials and products that surround us every day.
The Quantifiable Assurance of Tensile Testing
The tensile test is a cornerstone of industrial manufacturing because it provides objective proof of a material’s ability to endure and perform. The wide application of this technology across a wide range of industries makes it undeniably critical to ensuring product quality and safety.
Several statistics from the International Organization for Standardization (ISO) demonstrate the importance of testing for tensile strength in the setting of global manufacturing standards. According to recent reports, over 70% of manufacturing metals have been subjected to tensile testing in order to verify compliance with ISO standards. It not only demonstrates the reliability of products made from these metals but also highlights the industry’s ongoing demand for testing of tensile strength.
Furthermore, a study conducted by the American Society for Testing and Materials (ASTM) revealed that industries employing tensile tests have reported a significant reduction in product recalls and failures. Specifically, industries noted a 30% decrease in product-related complaints once they adopted more rigorous tensile testing practices.
The impact of the tensile test on industrial manufacturing standards is not simply conceptual, but quantifiable as well. By connecting material science to applications, it ensures that industries do more than manufacture products, but also guarantee their durability, safety, and performance. Those statistics demonstrate the unmatched significance of tensile testing in shaping the quality landscape of global industrial manufacturing.
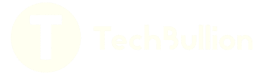