If you’ve ever been to a hardware store, you’ve probably seen sheet metal. It’s that thin, flat metal used for various purposes, from roofing to ductwork.
What is sheet metal fabrication?
Simply put, sheet metal fabrication is the process of shaping sheet metal into desired shapes using tools like presses, rollers, and dies. The sheet metal is first cut to size and then formed into the desired shape.
There are a variety of ways to form sheet metal, and the choice of method depends on the desired final shape of the product. For example, if you need to create a 90-degree bend, you would use a press brake. If you need to create a circular shape, you would use a roller.
Sheet metal fabrication is used in a variety of industries, from automotive to aerospace. And because there are so many different ways to fabricate sheet metal, the possibilities for products are endless.
So, next time you see a piece of sheet metal, think about all the steps that went into its fabrication and appreciate the workmanship that went into creating it.
What is the Metal Fabrication process?
If you are in the business of creating metal products, it is important to understand the metal fabrication process. This process can be used to create a variety of metal products, including metal doors, windows, and even furniture. The Metalpie metal fabrication process is complex, but understanding the basics can help you create quality products.
- Design
The metal fabrication process begins with a design. This design can be created by an engineer or architect. Once the design is complete, it is sent to a metal fabricator. The fabricator will then create a prototype of the product. This prototype will be used to test the product before it is sent to the customer.
- Cutting
There are several ways to cut sheet metal, but the most common method is to use a shearing machine. This machine uses blades to cut the metal into the desired shape.
- desired shape
After the metal has been cut, it’s time to bend it into the desired shape. This is done using a press brake. The press brake has a die that is the same shape as the desired final product.
- Welding
After the welding is complete, the final step is to finish the product. This can be done by painting or powder coating the metal.
Once the prototype is approved, the fabricator will begin production. This product can be done in a variety of ways, depending on the product. For example, some products may be stamped out of sheet metal, while others may be cut and welded together. The fabricator will use a variety of tools to create the product, including saws, presses, and welding torches.
Sent for the customer approval
After the product is created, it will be sent to the customer for approval. If the customer is satisfied with the product, they will sign a contract and the product will go into production. If the customer is not satisfied with the product, they may request changes or cancel the order altogether.
The metal fabrication process is complex, but understanding the basics can help you create quality products. By working with a qualified fabricator, you can ensure that your products meet your exact specifications.
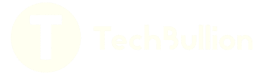