The complete process of metal fabrication is comprised of multiple processes. Cutting, bending and assembling are the essential components of this process. Therefore, aligning with the needs of each of these processes will help shape the metal to a desired size and shape.
It doesn’t matter if the metal sheet is used in 4 wheeler parts or a generator, the sheet needs to go through these processes to ensure that it is fit for usage. Let’s begin this article by defining and taking you through all these processes and providing you with reasons to choose and advantages.
Defining Metal Fabrication: What is it and where is it used?
Metal fabrication is the meticulous art of crafting metal structures and components through cutting, shaping, and assembling. These structures find their homes in a plethora of industries, ranging from aerospace and automotive to architecture and manufacturing.
The sheer versatility of metal fabrication makes it indispensable. It’s used to create everything from massive steel beams that support architectural wonders to tiny precision components found within medical devices. Metal fabrication can range from simple tasks, like cutting a steel plate, to highly complex operations, such as constructing a custom-designed machine.
Reasons to Choose Laser Cutting in Metal Fabrication
Within the vast spectrum of metal fabrication methods, laser cutting has emerged as a shining star. Its popularity is not without reason. Here are some compelling reasons to opt for laser cutting in metal fabrication:
1. High-Precision and Accuracy
Laser cutting is the epitome of precision in metal fabrication. It employs a focused laser beam to make fine, intricate cuts with impeccable accuracy. This process is instrumental when working with intricate designs or materials that demand exact specifications. The laser’s precision reduces material wastage, making it an environmentally friendly option as well.
2. Automated Process
Laser cutting is an automated process, that enhances efficiency and consistency. Computer-controlled systems guide the laser, ensuring that cuts and patterns are replicated with minimal variance. This automation minimizes human error, resulting in high-quality, consistent results.
3. Damage Prevention
Traditional cutting methods can subject materials to heat damage due to the generation of high temperatures. Laser cutting uses a non-contact method which has no physical interaction between the laser and the material. This results in a reduced risk of material damage, warping, or distortion.
4. Relatively Low Cost
Laser cutting technology might sound high-tech and expensive. However, the technology can actually be cost-effective in the long run for metal sheet production for four wheeler parts. The precision and automation of laser cutting reduce labour costs and material wastage. Additionally, it allows for the cutting of various materials, making it a versatile choice.
5. Compatible With Most Materials
Laser cutting goes beyond a single type of metal. The laser-cutting process can be applied to stainless steel, aluminum and copper. This adaptability for laser metal fabrication is a significant advantage in industries that require working with different materials for various applications.
What are the Advantages of Metal Fabrication?
Metal fabrication offers a multitude of advantages that make it a preferred choice across industries. Let’s explore these advantages in detail:
1. High-Precision and Accuracy
Metal fabrication, particularly when employing techniques like laser cutting, delivers high precision and accuracy. This is vital in industries where even the slightest error can lead to catastrophic consequences. With such precision, manufacturers can create components with tight tolerances, ensuring seamless compatibility and functionality.
2. Automated Process
Automation is a hallmark of modern metal fabrication. Computer-aided design (CAD) and computer-aided manufacturing (CAM) systems have revolutionized the process. These technologies allow for the creation of detailed, accurate blueprints and the seamless translation of those blueprints into physical structures. Automated processes also reduce the risk of human error, ensuring consistency and reliability.
3. Damage Prevention
Damage prevention is a critical advantage, especially in applications where the structural integrity of the fabricated components is paramount. Traditional cutting methods, like abrasive cutting, can generate substantial heat, causing warping or even material failure. In contrast, techniques like laser cutting are non-contact, reducing the risk of heat-related damage. This ensures that the fabricated parts maintain their structural integrity.
4. Relatively Low-Cost
Metal fabrication, despite its high-tech processes and precision, is often cost-effective. The automation of many fabrication processes reduces labour costs. Additionally, the ability to work with a wide range of materials means that manufacturers can choose cost-effective options without sacrificing quality.
This cost-efficiency extends to the maintenance of equipment. As modern machines work on the principle of enhanced durability and longevity cost-efficiency will come as a major support.
5. Compatible with Most Materials
The versatility of metal fabrication is a significant advantage. Manufacturers can work with a wide range of materials, from common metals like steel and aluminum to exotic alloys. This compatibility allows for the creation of diverse products for various industries. Whether it’s a delicate medical device or a heavy-duty industrial machine, metal fabrication can adapt to the material requirements of the task.
Conclusion
In the ever-evolving landscape of modern industry, metal fabrication remains a cornerstone of progress. Its precision, automation, and damage prevention capabilities make it an invaluable asset in the manufacturing of Honda Genset spare parts, bikes & cars spare parts, and much more. Furthermore, its relatively low cost and compatibility with various materials ensure its continued relevance in an ever-changing world.
By choosing metal fabrication, manufacturers opt for a proven method that shapes the future of innovation. Whether constructing the next architectural marvel or engineering the latest technological breakthrough, metal fabrication is there, silently but profoundly supporting progress in all its forms.
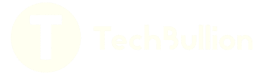