We are surrounded by electronic devices that have become a vital part of our daily life in the modern world. From smartphones and laptops to medical equipment and automotive systems, intricate circuitry is required for these gadgets to function correctly.
The printed circuit board (PCB), a critical component that links and supports numerous electronic components, is at the heart of these sophisticated circuits.
PCB fabrication is the process of creating these key circuit boards, and comprehending its complexities is critical for anyone working in electronics.
Overview of PCBs
A printed circuit board (PCB) is a flat board constructed of non-conductive material, usually fiberglass, with thin copper-laminated layers. A printed circuit board’s (PCB) role provides mechanical support and electrical connections between various electronic components such as resistors, capacitors, and integrated circuits. The design and arrangement of the copper traces on the board determine the circuit’s functionality.
PCB Fabrication Process
Several critical phases are involved in the PCB production process, which converts a design concept into a working circuit board. The trip begins with designing the PCB layout using specialist software, which translates the schematic diagram into a physical representation of the board. The fabrication process can start once the layout has been finished.
The First Stage
It starts with preparing the substrate, which entails choosing an appropriate base material and cutting it into the necessary shape. FR-4, or fiberglass epoxy laminate, is the most often used material, which provides excellent insulation and mechanical strength.
The Second Stage
A coating of copper is applied to the substrate. This is accomplished by a technique known as copper foil lamination, in which copper sheets are glued to the substrate using heat and pressure. After applying the copper layer, the extra copper is etched away, leaving only the needed copper traces to construct the circuit.
The Third Stage
Drilling and plating are necessary procedures in PCB construction. Small holes are drilled into the board to enable component installation and interconnection. To establish good electrical connections between the layers of the PCB, these holes are subsequently coated with a conductive substance.
A solder mask is put on the board to shield the copper lines and avoid short circuits. This layer serves as an insulator and gives the PCB a distinct color. A silkscreen layer is also applied to include component labels, logos, and other markings for identification and assembly.
The Fourth Stage
Another critical factor in PCB manufacture is surface polish. It entails applying a protective coating to the copper traces to prevent oxidation and maintain good solderability. Hot air solder leveling (HASL), electroless nickel immersion gold (ENIG), and organic solderability preservative (OSP) are all surface finish alternatives.
Quality Control and Testing
Strict quality control methods are performed throughout the PCB fabrication process to guarantee the finished product fulfills the needed standards. Visual inspection and automated optical inspection (AOI) are often utilized to discover production flaws or anomalies. Electrical and functional tests are also conducted to ensure the PCB’s functionality and reliability.
Conclusion
The manufacture of PCBs is critical in creating modern electronic gadgets. Every stage in the fabrication process, from the initial design to the final testing, necessitates precision and attention to detail.
As technology advances, PCB fabrication will change to meet the industry’s changing needs. Thus, understanding the complexities of PCB fabrication is critical for engineers, designers, and manufacturers working in electronics since it serves as the foundation for our linked world.
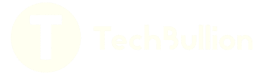