What is a hot melt adhesive web and how does it work?
Deciphering the Structure of Hot Melt Adhesive Webs
Hot melt adhesive webs are made of thermoplastic polymers that are frost-sensitive and retain a solid state at ambient temperature but undergo phase transition when being heated. The precursor polymers of these thermoplastic elastomers are usually ethylene, polyethylene, polypropylene, ethylene-vinyl acetate (EVA) or other related polynomials. The web format is created by extruding the molten adhesive formed via a die, which snaps to a rapid solid state upon cooling to obliterate die cuts of bonding webs by themselves, forming continuous and thin structures. This structural composition provides the adhesive web with the capacity to coalesce with other substrates when heated to a certain degree, thus providing the element to form strong connections.
View Hot Melt Adhesive Web – Hengning details to get into the details
Applying the Bonding Process: The Mechanism Through Which Hot Melt Adhesive Webs Works
Hot melt adhesive webs bond using quick and effective methods. After applying hot melt adhesive webs, applying heat on it will loosen the webs making the connection tacky. The tackiness allows the adhesive web to flow across the substrate making it possible for the surfaces to coalesce together after cooling down. The coalescing further establishes the substrate and the adhesive web bond, enhancing the connection. The requirement of the heat and quick setting conditions enable unscrambling hot melt webs to be used quickly for mass production.
View Hot Melt Adhesive Web – Hengning for More Details
Evaluation of Hot Melt Adhesive Webs with Other Types of Adhesives
Hot melt adhesive webs are unique from other forms of bonding. Out of all the hot mix of vision, formulations, clad, and sealing branches, one working with hot melt adhesive webs is the fastest to dry. Also, hot melt adhesive webs do not contain any moisture, which is in contrast with water-based adhesives, making hot melt adhesive webs moisture contamination-free. Finally, hot melt adhesive webs bond remarkably to a wide variety of surfaces such as textiles, sprays, polymers, and many more, thus making it efficient for a range of bonding requirements.
Thus, having knowledge of hot melt adhesive webs formulation, processes that the bonding undergoes, and advantages of hot melt webs over other adhesive solutions, where hot melt adhesive webs have for bonding applications, can be freely harnessed.
What are the different types of hot melt adhesive webs available?
Exploring various thermoplastic polymers used in hot melt adhesive webs
Using hot melt adhesive webs, various thermoplastic polymers are utilized, each having distinct characteristics as well as applications. A little knowledge about these polymers would assist in selecting the most appropriate adhesive web for the bond in question. Some of the most common thermoplastic polymers in hot melt adhesive webs include the following:
- Polyamide (PA): Polyamide hot melt adhesive webs are used in applications where bond strength and resistance to high temperatures are required, such as in the interior parts of automobiles and textiles.
- Polyester (PET): Polyester hot melt adhesive webs can be applied to electronic, automotive, and packaging industries because they act as coats and excellent protection against moisture and chemical attacks.
- Ethylene vinyl acetate (EVA): One reason EVA hot melt adhesive webs are so versatile is because of their flexibility, permeating them into textile, foam bonding and general assembly applications.
- Polyurethane (PUR): Polyurethane hot melt adhesive webs have one of the best adhesive combinations that have great bond strength, heat resistance, and flexibility; thus, these adhesives can find usage in automotive, foot wear and construction industry.
Specialized hot melt adhesive webs for specific applications:
In addition to the polymers mentioned, there are specialized hot melt adhesive webs tailored for specific applications. To name a few:
- Pressure-Sensitive Adhesive (PSA): What distinguishes the PSA hot melt adhesive webs is their unique tackiness that allows them to be bonded instantly when slight pressure is applied. Such adhesives are applied in the bonding of labels, tapes and dressing for medical use.
- Low VOC: High bond strength and durability can be achieved with hot melt adhesive webs with low VOC emisson which are designed to meet stringent requirements on the emission of haps VOCs. These types of adhesives are also suitable for those application where environmental regulation is strictly adhered.
You can increase the known experiences you’ve gotten by familiarizing yourself with the various thermoplastic polymers and specific hot melt adhesive webs so that you make an informed decision in choosing the right adhesive web to meet the requirements of your project.
What materials can be bonded using hot melt adhesive webs?
Adhesive Solutions for Aligning Textiles and Non-Woven Fabrics: The efficacy of Hot Melt Adhesive Webs
It can be concluded that an efficient thermal adhesive web is produced when attempting to bond any type of fabric together because of its positive quality reinforcement. In other words, the webbing provides sturdiness and durability to the fabrics which are subjected to rough conditions. Hot melt webs can bond textiles made out of cotton, polyester nylon, and other synthetic and natural fibres. The combinations of the fibres along with the hot melt adhesive webbing’s versatility allow it to be used in a wide range of garments, upholstery, and automotives.
Bonds between Foams and Laminates Patched Together with Hot Melt Adhesive Webs
Another function of hot melt adhesive webs is the joining together of foam padding and laminates. From covering padding that cushions furniture through to attaching laminates onto a variety of surfaces and materials, the versatility of the hot melt web adhesive allows for this – all with ease. These adhesive webs are sturdy and all-accommodating, with no limitations on their seam offerings, as they can be firmly affixed with polyurethanes foam, expanded styrene foam and polyethylene foam to name but a few. Moreover, a position of strength is reinforced with the hot melt web where firmness is required: wood veneer, a plastic laminate, or a metal foil.
Integrating Hot Melt Adhesive Webs Across Plastics and More.
The important quality that hot melt adhesive webs possess is bonding with whatever portraying high bonding strength, and these rewrite hot melt workers get to bond with plastics and other substrates too. Whether it is bonding the plastic parts in electronics or even the paperboard in packaging, these adhesives allows you to have a trustworthy bond. Hot melt adhesive webs bond over a wide range of plastics such as polypropylene (PP), polyethylene (PE), polystyrene (PS), and many more. Aside that, they can stick to paper, cardboard, metals as well as some woods. Always with the ability to stick, hot melt adhesive webs can be used in many applications across many industries.
Taking into consideration the specific bonding needs of your works and taking the proper hot melt adhesive web allows you to comfortably achieve desired natural bonding which assists you in boosting the performance of your work and the end product.
How do you choose the right hot melt adhesive web for your project?
The factors below play a critical role while selecting the right adhesive web for your hot melt project, factoring in bonding performance.
- Substrate Compatibility: Check the adhesives’ bonding requirements to the materials. Analyze the surface energy, porosity, and temperature resistance of the substrates involved in order to select an adhesive that will form strong and durable joints.
- Bond Strength Requirements: Determine the operational strength required for your bond in a particular application. There are different hot melt adhesive webs with different bond strength; one should select adhesive suitable for the nature of the project.
- Viscosity and Open Time: When trying to locate a glue leg, the first thing to remember is that many glues have the appropriate amount of viscosity but are not suitable for the amount of time the device will be used. It is worthwhile to check the glue’s viscosity along its open time for ease of application.
- Temperature Performance: Identify the temperature range in which your application is to be utilized. The hot melt adhesive web should be able to sustain the operational temperatures that might be found in the process of manufacturing, storing, and even using the product without losing the integrity of the bond.
- Environmental Considerations: Take account of any special environmental factors, such as moisture, chemicals or UV radiations. Opt for an adhesive that provides sufficient stability as well as strength to endure these peculiar climatic effects.
This helps to ensure that you select as per informational, performance and technical requirements such as project specifications, materials and environmental conditions, the specific hot melt adhesive web type required.
What are the advantages of using hot melt adhesive webs over other bonding methods?
Benefit from Hot Melt Adhesive Webs in Terms of Speed and Efficiency
Combining speed and efficiency is the notable aspect of Hot melt adhesive webs which makes them among the top choices in most production processes. Below, are some of their key benefits:
- Rapid Assembly and Joining: The properties of hot melt adhesive web allow it to turn from liquid into solid form within a short time span making assembly and bonding faster hence lowering the production period while boosting efficiency.
- Elimination of Drying or Curing Time: Apart from the melting of the substrate, there are no other heating procedures making hot melt adhesive webs a great solution since it does not require any curing or expanding time between bonding processes.
- Increased Production Speed: Hot melt adhesive webs boost the production speed as their setting process is quite fast and there is no expansion time allowing the manufacturing processes to keep operating unhindered.
- Applicable to High-Volume Automation: Hot melt adhesive webs can be employed in high volume manufacturing machines because of their ability to bond in under pressure. They can be easily incorporated into mechanized systems, increasing productivity and reducing production constraints.
Adaptability to the requirements of the different manufacturing industries
Hot melt adhesive webs are highly applicable in almost all industries making them highly capable of meeting various manufacturing requirements. Some examples include:
- Automotive Industry: Hot melt adhesive webs are critical in automotive manufacturing as they can be utilized in providing strong bonds used in the assembly of interior trims, headliners, wire harnesses, as well as in carpeting.
- Textile and Apparel Manufacturing: The hot melt adhesive webs are also highly used in the textile and apparel sector for seam sealing, fabric lamination, hems and attaching labels to fabric. Because of their flexibility and ease of use, they are ideal for sewing together textile fabrics.
- Packaging and Product Assembly: In both packaging and product assembly applications, hot melt adhesive webs are quite extensively used providing strong bonds in the sealing of cartons, box making and assembling case trays and for attaching labels and tags.
With their speed, effectiveness and diversity hot melt adhesive webs increase the productivity of processes in all sectors while ensuring accurate bonds and reliability in the quality of the end product.
How do you properly apply and use hot melt adhesive webs?
You are always reminded to apply hot melt adhesive webs correctly to allow seamless bonding and adequate performance. Use the following steps for the successful application hot melt adhesive webs:
- Surface Preparation: The surfaces that are to be glued together should be dry, clean and free from contaminants, dust, and debris. This will assist in obtaining a strong and lasting bond.
- Warm Up the Adhesive: Increase the temperature of the hot melt adhesive systems as directed by the manufacturer. This is to make sure that it is molten and ready to be used.
- Bonding Process: Choose a thin, even surface of one of the substrate surfaces along the other surface with a dependable hot melt adhesive applicator or dispenser which you will be using with caution so as to avoid excess glue application. Exceeding in amount of glue can cause weak bonding strength and waste.
- Add the Substrates: As soon as the adhesive is set into place, press the two substrates together aligning them with utmost care. Also, Uh, uh, it’s mesmerizing. Then apply even pressure over the entire bond area to facilitate proper contact and bonding.
- Set aside sufficient time for bonding: Allow the adhesive to cure, shrink and completely fill the gap between the two substrates. Avoid modifying the applied adhesive, as this could possibly weaken the bond. Bi-directional shear stresses can also be applied, in accordance with the manufacturer’s specifications.
The most common mistakes to avoid when working with hot melt adhesive webs
- Heating the adhesive more than normal: The weak points of thermoplastic materials are thermal and chemical degradation, and hence, sticking to the application recommended temperatures is crucial.
- Lack of proper cleaning: It is crucial for the surface which needs to be adhered to be cleant and effectively dried as there is a possibility of low adhesive strength otherwise.
- Using an inappropriate adhesive: Different types of glue effect differently when intermixed so it is best to use glue that best suits the application that you seek to bond.
- Too much adhesive being applied: If an excessive amount of glue is used the bonding strength may weaken as well as there being overuse of glue. The recommended amount of adhesive to be used is what’s stated by the manufacturers.
- Low bonding pressure: If proper pressure is not used when gluing, very weak bonds are likely to be formed. Adequate pressure should be ysed to ensure that strong contact forms at all the necessary bond domains.
While observing these steps and evading typical mistakes, you stand a better chance of achieving, successful bonding results and therefore be able to fully realize the merits of hot melt adhesive webs in your applications.
What are some popular applications for hot melt adhesive webs in different industries?
The use of hot Melt adhesive forms is very relevant in not only the automotive, textile and apparel manufacturing, packaging, and product assembly services.
The Uses of Hot Melt Adhesive Webs in the Automotive Industry:
Interior Trim Assembly: These webs are used to adhere the headliners, door panels, seating materials and any interior parts of a vehicle during the assembly process. This guarantees a steady, strong adhesion point to the part in question.
Wire harnessing: Hot Melt adhesive Webs are handy as they hold wire harnesses which are susceptible to factors such as moisture, vibration and mechanical stress.
Foam Lamination: These adhesive webs are appropriate for foam so lamination in regards to automotive seating and insulation as they fill in cracks and provide easy and fast manufacturing.
Other Uses in Textiles and Apparels:
Seam sealing: For waterproof seams in fabric manufacturing these webs are used as they are cost effective.
Embroidery: To use machines for embroidery, fabric bonding webs are used in order to minimize the fabric movement during the sewing.
Fabric sewing: These webs are used to bond two fabrics bonding the fabrics together eliminating the need for needle and thread.
Using Hot Melt Adhesive Webs In the Packaging and Product Assembly:
Box and Carton Sealing: Adhesive webs are effective in sealing boxes and cartons as they help in providing secure closures without leaving evidence of tampering.
Product Assembly: The in-demand adhesive webs suffice to meet the needs of industries in areas such as assembly of electronics and woodworking, as well as general manufacturing.
By employing hot melt adhesive webs industries are able to increase effectiveness within the different production processes, as well as improve the products, and obtain better bonds in various applications.
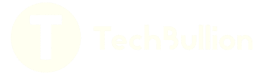