Sheet metal manufacturing is the process of shaping and forming thin, flat pieces of metal into a variety of products and components. This fabrication method involves cutting, bending, stamping, and assembling sheet metals to create structures and parts used in diverse industries.
Sheet metal manufacturing holds immense significance across industries due to its versatility, precision, and cost-effectiveness. In automotive, aerospace, construction, electronics, and more, it serves as a foundational process for creating components vital to product functionality. From intricate electronic enclosures to structural elements in architecture, sheet metal manufacturing plays a pivotal role in bringing designs to fruition with efficiency and durability. Its adaptability to different metals and the ability to produce complex shapes make it indispensable in meeting the diverse needs of modern manufacturing.
A Journey Through sheet metal Manufacturing
Tracing its roots back through time, sheet metal manufacturing has evolved from rudimentary handcrafting to today’s precision-driven processes. Technological leaps have transformed sheet metal from a humble material to a versatile cornerstone of engineering.
Historical Context of sheet metal Manufacturing
sheet metal manufacturing has ancient origins, dating back to civilizations such as the Egyptians and Greeks. Early metalworkers utilized basic techniques like hammering and hand rolling to shape thin sheets of metals like copper and bronze for various applications.
Industrial Revolution Impact
The advent of the Industrial Revolution in the 18th and 19th centuries marked a transformative era for sheet metal manufacturing. Steam-powered rolling mills and hydraulic presses mechanized the process, enabling mass production of sheet metal for construction, transportation, and industrial applications.
Late 20th Century Automation
In the latter half of the 20th century, automation and computerization revolutionized sheet metal manufacturing. CNC (Computer Numerical Control) machines brought unprecedented precision, efficiency, and repeatability to cnc cutting, bending, and forming processes.
21st Century Integration
The 21st century sees sheet metal manufacturing deeply integrated into global supply chains across diverse industries. Advanced technologies like laser cutting, 3D printing, and robotics continue to redefine the landscape, enabling intricate designs and cost-effective production.
Type of Materials used in Sheet metal Manufacturing
Sheet metal manufacturing involves various types of materials, each chosen for its specific properties and suitability for the intended application. Commonly used materials include:
● Steel
Carbon steel, stainless steel, and galvanized steel are frequently used in sheet metal manufacturing. Carbon steel is known for its strength, while stainless steel offers corrosion resistance, making it suitable for various applications.
● Aluminum
Aluminum is valued for its lightweight properties, corrosion resistance, and versatility. It is commonly used in industries like aerospace and automotive for components where weight is a critical factor.
● Copper
Copper sheets are utilized for their excellent conductivity and corrosion resistance. They find applications in electrical components, roofing, and decorative elements.
● Brass
Brass, an alloy of copper and zinc, combines the corrosion resistance of copper with the durability of zinc. It is often chosen for decorative purposes, musical instruments, and certain hardware applications.
● Titanium
Titanium sheets are known for their high strength-to-weight ratio, corrosion resistance, and biocompatibility. They are commonly used in aerospace, medical implants, and chemical processing.
● Nickel Alloys
Nickel-based alloys, such as Inconel and Monel, are known for their high temperature and corrosion resistance. They find applications in aerospace, chemical processing, and marine industries.
The choice of material depends on factors such as the application’s requirements, desired properties (e.g., strength, weight, corrosion resistance), and cost considerations. Sheet metal manufacturers carefully select the appropriate material to meet the specific needs of the project or product they are fabricating.
Various Sheet Metal Forming Processes
Stamping, bending, Deep drawing, hydroforming– these are the brushstrokes of sheet metal fabrication. Unraveling the intricacies of these processes reveals the artistry behind creating precise components that power industries.
Stamping
Stamping is a sheet metal forming process that involves cutting, bending, or shaping sheet metals using a press and a die. The process begins with a sheet metal placed between the die and a punch. The press exerts force, causing the metal to deform and take the shape of the die. Stamping is commonly used for mass production of components with consistent shapes, such as automotive body parts, appliance panels, and electronic components.
Bending
Metal Bending is a process that involves deforming a sheet metal workpiece along a straight axis. A press brake is commonly used to apply force on a specific point, causing the metal to bend. Various bend angles and shapes can be achieved by adjusting the tooling and controlling the material’s positioning. Bending is employed in the creation of structural components, brackets, and other parts requiring angular shapes in industries such as construction and manufacturing.
Deep Drawing
Deep drawing is a process used to form complex shapes with significant depth from a flat sheet of metal. In this process, the sheet is clamped over a die and a punch is used to draw the material into the die cavity. Deep drawing is commonly employed in the production of cylindrical or box-shaped components, such as kitchen sinks, beverage cans, and automotive parts like car body panels.
Hydroforming
Hydroforming involves shaping sheet metal using fluid pressure. The sheet metal is placed over a die, and high-pressure fluid is introduced, forcing the sheet into the die cavity. Hydroforming allows for the creation of complex shapes with reduced tooling wear. It is commonly used in the aerospace, automotive, and bicycle industries for producing lightweight and structurally efficient components.
These sheet metal forming processes showcase the versatility of manufacturing techniques, allowing for the creation of a wide range of components with varying shapes and sizes to meet the demands of diverse industries.
Technological Advancements
In the dynamic landscape of sheet metal manufacturing, the integration of automation, robotics, and artificial intelligence (AI) stands as a transformative force, ushering in unprecedented levels of efficiency, precision, and scalability.
Precision Engineering
Automation systems, guided by sophisticated algorithms, ensure precise control over cutting, bending, and forming processes.
Robotics equipped with advanced sensors can adapt to variations in material thickness and properties, maintaining consistent quality in every manufactured piece.
Increased Efficiency
Automated workflows minimize human intervention in repetitive and time-consuming tasks, reducing production time and costs.Robots equipped with AI algorithms can optimize the manufacturing process by making real-time adjustments, resulting in faster and more efficient operations.
Scalability and Flexibility
Automated systems provide a scalable solution, allowing manufacturers to adjust production volumes quickly in response to market demands.
Flexible robotic arms, programmed with AI, can switch between different tasks and adapt to varying product specifications, enhancing overall production flexibility.
Quality Assurance
AI-driven quality control systems utilize machine vision to inspect products with unparalleled precision, identifying defects and ensuring that each component meets exacting standards. Automation reduces the risk of human error, contributing to a higher overall quality of the manufactured sheet metal products.
Collaborative Robotics (Cobots)
Collaborative robots, or cobots, work alongside human operators, enhancing the synergy between automation and human skills. This collaborative approach combines the precision of robots with the adaptability and creativity of human workers.
In essence, the marriage of automation, robotics, and AI in modern sheet metal manufacturing not only accelerates the pace of production but elevates the entire industry to new heights of precision and adaptability. As technology continues to evolve, the symbiotic relationship between human expertise and automated systems promises a future where sheet metal manufacturing achieves unparalleled efficiency, quality, and scalability.
Common challenges in sheet metal Manufacturing
Sheet metal manufacturing, while versatile and essential, faces several common challenges that manufacturers must navigate to ensure optimal efficiency and product quality. Some of these challenges include
Material Selection and Variability
Choosing the right material is crucial, and variations in material properties can impact the manufacturing process. Inconsistent material thickness, strength, or composition can lead to quality issues.
Precision and Tolerance Control
Maintaining tight tolerances is critical in sheet metal manufacturing. Variations in processes, tooling, or material properties can lead to deviations from specified dimensions, impacting the overall quality of the product.
Ensuring the quality of each manufactured component is paramount. Implementing effective quality control measures, including inspections and testing, can be demanding but is essential to prevent defects and meet industry standards.
Complexity of Designs
Intricate designs or tight tolerances may pose challenges during manufacturing. Achieving precision in complex geometries can be time-consuming and may require advanced equipment and skilled operators.
Waste Minimization
Minimizing material waste is a constant concern. Efficient nesting of parts on sheet metals and optimizing cutting paths help reduce waste, contributing to cost-effectiveness and environmental sustainability.
Diverse Range of Industries benefiting from Sheet Metal Components
Sheet metal’s ubiquity in everyday products is a testament to its versatility and widespread application. From the structural components of buildings to the sleek casings of electronic devices, sheet metal plays a crucial role in shaping the world around us. Here’s a glimpse into its omnipresence:
● Automotive Marvels
Car bodies, chassis, and various components rely on sheet metal for strength, durability, and design flexibility.
● Architectural Foundations
Roofing, gutters, and façades often feature sheet metal weather resistance and malleability.
● Aerospace Engineering
Aircraft fuselages, wings, and critical structural elements utilize sheet metal for its lightweight yet robust properties.
● Furniture Framework
Chairs, tables, and shelving units often incorporate sheet metal for its strength and modern aesthetic
● Medical Equipment
Surgical instruments, diagnostic devices, and medical furniture benefit from sheet metal’s hygienic properties and precision manufacturing
● Consumer Goods Packaging
Cans, containers, and packaging materials often involve sheet metal, showcasing its versatility in various industries.
Sheet metal’s ability to seamlessly integrate strength, durability, and aesthetic appeal makes it an unsung hero in the creation of countless products that shape our daily lives.
Environmental considerations in sheet metal Manufacturing
In sheet metal fabrication, it’s crucial to consider the environment to reduce the impact on our planet. This includes minimizing waste by efficiently using materials and recycling scrap metal. Choosing eco-friendly materials and processes helps lower the carbon footprint. Additionally, implementing energy-efficient practices and technologies reduces overall energy consumption. By adopting sustainable manufacturing methods, such as water-based coatings instead of harmful chemicals, the industry can contribute to preserving the environment for future generations. Environmental responsibility in sheet metal manufacturing involves a commitment to resource efficiency, waste reduction, and embracing technologies that prioritize the well-being of our planet.
Adaptation to Technological Changes
Technological changes in sheet metal manufacturing is crucial for staying competitive and efficient in today’s fast-evolving landscape. With the continual advancements in automation, robotics, and artificial intelligence, manufacturers must embrace new technologies to enhance precision, speed, and overall productivity. Integrating modern machinery and software solutions not only streamlines production processes but also improves product quality. Training the workforce to operate and understand these technologies becomes essential. This adaptation ensures that the industry keeps pace with innovation, meeting market demands and maintaining high standards.
In summary, creating sheet metals is like an evolving art that combines old and new techniques. From traditional craftsmanship to modern machines, the industry has adapted well. The precision, versatility, and ability to make a bunch of sheets at once show how it has changed.
Even though there are challenges, like using different materials and needing skilled workers, the industry cares about the environment. They’re looking forward and trying to be sustainable. sheet metals are used in many things today, especially in making various engineering products.
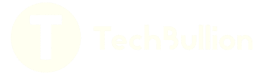