Fabricating machinery and structures through sheet metal is collectively referred to as sheet metal fabrication. It’s not uncommon for this to be a lengthy procedure requiring many specialists’ expertise. Fabrication shops, or fab shops, are businesses that specialize in fabricating metal structures. Therefore, whether you’re in the market for sheet metal fabrication in Europe, the Americas, or anywhere else, there are service providers such as Metaline that can meet your demands and provide assistance on manufacturing processes and best practices.
Sheets of metal, hammered by hand, have been employed in building construction since ancient times. In the latter 17th century, hammering was replaced by rolling mills driven by water. Metal was pressed into sheets by rolling it between two enormous iron cylinders. Lead, copper, iron, zinc, and, later on, steel were the metals used. Metal sheets made of iron or steel were commonly tinned to avoid corrosion. The term “tinplate” was used to describe this kind of tin-coated metal.
The 1870s saw the widespread use of sheet metal in the United States for applications as varied as shingle roofing, stamped ornate ceilings, and outside façades. Middle-class consumers were eager to buy sheet metal after technological developments in the 1890s made it inexpensive, long-lasting, simple to install, and fireproof. This article will concentrate on the industries and applications as well as the processes and materials that are relevant to sheet metal fabrication. So, let’s get started.
Materials Used in Sheet Metal Fabrication
Sheet metal comes in many forms, and it may be shaped via fabrication to serve a range of functions. Metals like these are frequently utilized in sheet metal fabrication:
Steel
Although the metal comes in many forms—from stainless steel to carbon steel to galvanized steel—it is universally recognized for its strength and durability. Steel with a low carbon content is used for railings and fences. On the other hand, steel with a medium carbon level is used in the production of automobiles and home appliances. Steel wires typically have the greatest carbon content of any common kind of sheet metal. Stainless steel is a versatile metal that has various applications, including but not limited to kitchenware and medical equipment.
Aluminum
Despite its reduced weight, aluminum has a similar strength as steel. Use in aircraft and refrigeration is based, in part, on its performance at low temperatures. Aluminum sheet metal has several applications, including in the automobile, electronics, and kitchenware industries.
Magnesium
Magnesium is a low-density structural metal that provides rigidity. It’s been utilized for automotive components and as a structural metal in the shipping industry since World War II.
Brass
Brass’s acoustic qualities make it a valuable material, but it is also widely utilized for structural components and fixtures. Metal with great tensile strength, low weight, and corrosion resistance.
Bronze
Sheet metal made of bronze has a low melting point and is far more durable than copper; common uses for bronze sheet metal include coinage, cookware, and turbines.
Copper
Copper has several desirable properties: corrosion resistance, ductility, and electrical conductivity. Electrical parts, conductors, decorations, and jewelry are a few common copper metal sheet uses.
Processes Involved in Sheet Metal Fabrication
Forming, cutting, and joining are the three primary methods used in sheet metal manufacturing.
Forming
Stamping, bending, stretching, and roll forming are all examples of operations that fall under the category of “forming.” In contrast to cutting, which removes material from a piece of sheet metal, the process of forming merely reshapes the metal to conform to the required contours.
Cutting
There are two types of cutting: cutting with a shear and cutting without a shear. Shearing, cutting, and blanking are all examples of procedures that fall under the umbrella of “shear cutting.” Since these sorts of cuts are less accurate than methods that do not include shearing, they are more typically utilized for producing end goods that are used in the nonindustrial sector.
On the other hand, industrial items such as aircraft wings are cut using a method called non-shear cutting, which is considered to be more precise. In addition to machining, these procedures include cutting services performed using laser beams, plasma, and waterjets.
Joining
Welding, brazing, riveting, and the use of adhesives are all forms of sheet metal manufacturing that fall under the category of joining. After the sheet metal has been manufactured, it may next undergo a variety of finishing operations to improve its physical attributes. These processes may include sandblasting, deburring, annealing, and coating.
Industries and Applications of Sheet Metal Fabrication
Sheet metal fabrication is a highly adaptable process; as a result, it may be utilized in almost any industry to manufacture a wide variety of products, from components to vehicle bodywork. The aerospace, construction, automotive, heating, ventilation, & air conditioning (HVAC), consumer products, robotics, agricultural, electrical, and energy sectors are just some of the industries that depend on it. However, this is by no means an entire list. This is because there is a widespread need for industrial items made from metal, including housings, gears, and containers.
Most electronic enclosures and component pieces are prototyped using fabrication techniques that include sheet metal. Because it is a cheap procedure, prototypes may be inspected and evaluated at a cheaper cost. Any alterations can be conducted quickly and cost-effectively.
Small sheet metal pieces, such as brackets and cable connections, may be fabricated from sheet metal. Alloys made of steel, aluminum, stainless steel, and copper are strong enough to prevent bigger pieces of metal or plastic from splitting apart while holding them together. Suppose corrosion-resistant metals are utilized, such as stainless steel sheet metal or components that have been plated or coated. In that case, the parts will be protected against moisture and corrosion.
Flashing and rain gutters are two roofing components that may be fabricated from sheet metal. Sheet metal may be used to construct ducts and furnaces that are found inside structures. In addition, the sheet is used in the production of equipment used in surgery and dentistry, as well as MRI scanners, medical implants, and bone pins and plates.
Final Words
Now that we’ve emphasized information on what materials and techniques sheet metal fabrication utilizes, we always suggest that you discover the most dependable and trustworthy providers of sheet metal fabrication in the market. This can be done by searching online or on the local yellow pages. Nevertheless, we here recommend that you give Metaline a go, regardless of the size or complexity of the sheet metal production job you’re working on.
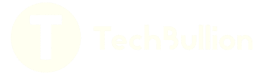