In the realm of healthcare, the production of medical devices is a critical endeavor that demands unwavering attention to quality. These devices play a pivotal role in diagnosing, treating, and managing various medical conditions, directly impacting patient outcomes and safety. The significance of quality in medical device manufacturing cannot be overstated, as it encompasses a spectrum of factors ranging from design and production processes to regulatory compliance and post-market surveillance. This article delves into the multifaceted role of quality in medical device manufacturing, highlighting its importance in ensuring efficacy, reliability, and safety across the healthcare landscape.
Ensuring Product Efficacy and Performance
Quality assurance measures in medical device manufacturing are paramount for ensuring product efficacy and performance. Rigorous testing protocols, adherence the regulatory standards, or continuous improvement initiatives are integral components of this process. Each stage of manufacturing, from initial design conception to final production, must undergo meticulous scrutiny to mitigate the risk of defects or malfunctions. For instance, in the development of implantable medical devices such as pacemakers or artificial joints, rigorous testing procedures are conducted to evaluate biocompatibility, mechanical integrity, and long-term performance. By adhering to stringent quality standards, manufacturers can instill confidence in healthcare professionals and patients regarding the safety and reliability of these devices.
Mitigating Risks and Enhancing Patient Safety
Quality management systems serve as a cornerstone for mitigating risks and enhancing patient safety in medical device manufacturing. Comprehensive risk assessment methodologies, such as Failure Mode and Effects Analysis (FMEA) and Hazard Analysis and Critical Control Points (HACCP), enable manufacturers to identify potential hazards and implement proactive measures to mitigate them. Moreover, adherence to regulatory frameworks, such as the ISO 13485 standard for quality management systems in the medical device industry, fosters a culture of accountability and continuous improvement. By implementing robust quality management systems, manufacturers can minimize the likelihood of adverse events, such as device failures or recalls, thereby safeguarding patient well-being and upholding the integrity of the healthcare ecosystem.
Ensuring Regulatory Compliance and Market Access
The attainment of regulatory compliance a imperative for medical device manufacturers seeking to bring their products to market or maintain market access. Regulatory bodies, such as the U.S. Food and Drug Administration (FDA) and the European Medicines Agency (EMA), enforce stringent requirements to ensure the safety, efficacy, and quality of medical devices. Manufacturers must navigate an complex landscape of regulations, encompassing product classifica pre-market approval processes or post-market surveillance obligations. By aligning with regulatory requirements or obtaining necessary certifications, such as the CE mark or FDA clearance, manufacturers demonstrate their commitment to upholding quality standards and meeting the needs of global markets. Moreover, ongoing compliance efforts, including routine audits and vigilance reporting, are essential for maintaining market access and fostering trust among regulatory authorities, healthcare providers, and patients alike.
Laminating Self-Adhesive Materials
Innovations in manufacturing processes play a pivotal role in enhancing the quality or efficiency of medical device production. One such advancement is the utilization of laminating self-adhesive materials, which offer numerous benefits in device assembly and packaging. By incorporating self-adhesive components into medical device manufacturing, manufacturers can streamline assembly processes, reduce the risk of contamination, and enhance product reliability. Additionally, laminating self-adhesive materials facilitate the integration of complex components, such a sensors or electronic circuits, into medical devices, enabling the development of sophisticated diagnostic or therapeutic solutions. Moreover, these materials contribute to the overall durability and longevity of medical devices, ensuring that they withstand the rigors of clinical use while maintaining their structural integrity. As manufacturers continue to embrace innovative manufacturing technologies, the integration of laminating self-adhesive materials represents a promising avenue for optimizing quality and performance across the medical device industry.
Enhancing Supply Chain Transparency
Supply chain transparency is essential in ensuring the integrity or safety of medical devices throughout their lifecycle. Traceability or serialization initiatives enable manufacturers to track and monitor the movement of components and finished products across the supply chain. By implementing robust traceability systems, manufacturers can quickly identify or address any issues or discrepancies that may arise, mitigating the risk of counterfeiting, diversion, and unauthorized distribution. Serialization, which involves assigning unique identifiers to individual products, further enhances supply chain visibility and facilitates product authentication and recall management. Through the adoption of traceability and serialization technologies, manufacturers can uphold the highest standards of quality and compliance while safeguarding patient safety and maintaining the trust of stakeholders within the healthcare ecosystem.
Embracing Data-driven Quality Management
Data-driven quality management approaches, such as predictive analytics and continuous improvement initiatives, empower manufacturers to proactively identify and address potential quality issues before they escalate. By leveraging big data analytics and machine learning algorithms, manufacturers can analyze vast amounts of production data to identify patterns, trends, and anomalies that may impact product quality. Predictive maintenance strategies enable proactive equipment maintenance or optimization, minimizing downtime or reducing the likelihood of production disruptions. Furthermore, continuous improvement methodologies, such as Lean Six Sigma, foster a culture of innovation and efficiency, driving incremental enhancements in manufacturing processes or product quality. Through the integration of data-driven quality management practices, manufacturers can achieve higher levels of operational excellence, cost-effectiveness, or customer satisfaction, ultimately delivering superior medical devices that meet the evolving needs of patients or healthcare providers.
The role of quality in medical device manufacturing extends beyond traditional quality assurance measures to encompass a comprehensive array of initiatives aimed at optimizing processes, enhancing transparency, and leveraging data-driven insights. From ensuring product efficacy and reliability to navigating regulatory compliance and supply chain complexities, quality serves as a guiding principle throughout every stage of the manufacturing lifecycle. By embracing innovative technologies, such as laminating self-adhesive materials, and adopting data-driven quality management approaches, manufacturers can uphold the highest standards of excellence while delivering safe, effective, and reliable medical devices to patients worldwide. As the healthcare landscape continues to evolve, the importance of quality in medical device manufacturing remains steadfast, driving innovation, efficiency, and continuous improvement across the industry.
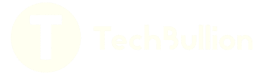