In the demanding world of industrial operations, equipment reliability is not an option but a necessity. Reliability managers and reliability engineers work tirelessly to maintain optimal equipment performance, yet equipment failure remains a persistent challenge.
These failures not only halt production but also incur a wide range of hidden costs that can deeply impact on an organization’s bottom line.
We will explore the hidden costs associated with equipment failure, delving into the roles of elements such as bearing failure, lubrication management, and reliability reports.
Furthermore, we will highlight the crucial role that advanced tools like the lubrication management software from Redlist can play in mitigating these costs.
Understanding Equipment Failure
Equipment failure is a broad term that encompasses any malfunction that disrupts the normal functioning of machinery. Common causes include bearing failure, inadequate lubrication, and wear and tear from regular use.
These failures can have far-reaching consequences, not just limited to repair costs and downtime but extending to a series of hidden costs that can severely impact an industrial business’s financial health.
The Hidden Costs of Equipment Failure
Unplanned Downtime
Unplanned downtime is one of the most immediate and visible effects of equipment failure. When machinery fails unexpectedly, production halts, leading to significant revenue loss. But the costs go beyond lost production hours:
Labor Costs: Workers may still need to be paid even if they are not producing anything.
Penalties and Fines: Missed deadlines can result in contractual penalties.
Customer Dissatisfaction: Delays can lead to customer dissatisfaction, potentially harming future business relations.
Reduced Equipment Lifespan
Frequent equipment failure can drastically shorten the lifespan of machinery. Repeated breakdowns cause wear and tear that accumulates over time, leading to premature failure. This necessitates early replacements, which are significant capital expenditures.
Maintenance Costs
While preventive maintenance is a planned expense, the cost of emergency repairs due to equipment failure can be steep. These include:
Parts Replacement: Emergency procurement of spare parts is often costlier.
Overtime Labor: Emergency repairs usually require technicians to work overtime, increasing labor costs.
Energy Inefficiency
Malfunctioning equipment often operates inefficiently, consuming more energy than necessary. This leads to higher utility bills and increases operational costs.
Safety Risks
Equipment failure can pose serious safety risks to employees, resulting in:
Injury Costs: Medical expenses, legal fees, and potential compensation claims.
Insurance Premiums: Higher premiums due to increased risk.
Quality Control Issues
Failures can compromise product quality, leading to defects that must be addressed:
Rework Costs: Expenses incurred in correcting defects or redoing products.
Scrap Costs: Wastage that cannot be reused or remanufactured.
The Role of Lubrication Management in Preventing Equipment Failure
One of the critical factors in equipment reliability is proper lubrication. Research indicates that a considerable percentage of bearing failures are related to inadequate or improper lubrication.
Effective lubrication management extends the lifespan of equipment, ensures smooth operation, and minimizes the risk of unexpected breakdowns. However, managing lubrication processes manually can be labor-intensive and prone to errors.
Introducing Lubrication Management Software from Redlist
Redlist offers state-of-the-art Lubrication Management Software designed to streamline and optimize lubrication processes. Here is how it can help mitigate the hidden costs of equipment failure:
- Automated Lubrication Tracking: Automated tracking ensures that lubrication schedules are adhered to, minimizing human error, and ensuring timely lubrication.
- Lubrication Program Optimization: By analyzing data on lubrication activities, the software helps optimize lubrication programs, ensuring that machinery receives the right type and amount of lubricant.
- Predictive Maintenance: The software can predict potential issues based on lubrication data, allowing for proactive maintenance before a failure occurs.
- Comprehensive Reliability Report: The software generates detailed reliability reports, offering insights into equipment health and potential failure points. This data is invaluable for making informed maintenance decisions.
Case Study: How Effective Lubrication Management Reduces Hidden Costs
Scenario
A manufacturing plant was experiencing frequent equipment downtime due to bearing failures. The unreliability of the machinery was leading to high maintenance costs, reduced production output, and declining employee morale.
Solution
The plant decided to implement the Lubrication Management Software from Redlist to improve their lubrication processes.
Results
Reduction in Bearing Failures: Proper lubrication schedules and accurate tracking resulted in a significant decrease in bearing failures.
Cost Savings: Reduced downtime and maintenance costs translated into substantial financial savings for the plant.
Increase in Equipment Lifespan: With well-maintained lubrication, equipment lifespans were extended, delaying the need for costly replacements.
Enhanced Safety: Properly lubricated machinery operated more reliably, reducing the risk of accidents, and improving workplace safety.
Check out some other case studies here.
Best Practices for Reliability Managers and Engineers
Regular Inspections
Conduct regular inspections to detect early signs of wear and tear. Use reliability reports to track equipment performance and identify potential issues before they lead to failure.
Implement Predictive Maintenance
Predictive maintenance uses data and analytics to predict equipment failures before they happen. This approach allows for timely intervention and minimizes unplanned downtime.
Proper Lubrication Management
Invest in lubrication management software like the one from Redlist to ensure that your lubrication processes are effective and efficient, reducing the risk of bearing failures and other lubrication-related issues.
Training and Development
Continuously train your team on the latest maintenance practices and the importance of reliability. A well-informed team is better equipped to handle equipment maintenance proactively.
Check this blog on how leadership and management and how these concepts are critical for a successful lubrication management system.
Conclusion
Equipment failures present numerous hidden costs that can severely impact industrial operations and financial performance. For reliability managers and reliability engineers, understanding these costs and adopting effective strategies to mitigate them is crucial.
That is where the lubrication program comes in. It plays a pivotal role in maintaining equipment reliability and preventing failures. By leveraging advanced tools like the Lubrication Management Software from Redlist, you can optimize your lubrication processes.
It extends the lifespan of your equipment, and significantly reduces the hidden costs associated with equipment failure. Embrace these strategies and tools to ensure that your machinery operates smoothly and efficiently, safeguarding both your operational performance and your bottom line. Book a free demo or talk to a lubrication management software expert today!
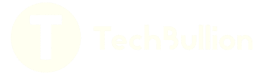