Manufacturing plants are dynamic environments where efficiency and reliability are paramount. Within these facilities, the integrity of piping systems is crucial for ensuring the smooth flow of materials and the operation of various processes. In recent years, stainless steel has emerged as a preferred material for piping solutions in manufacturing plants due to its exceptional properties and performance benefits. This article explores the significance of stainless steel piping in enhancing reliability and performance across diverse industrial settings.
Understanding Stainless Steel Piping
Stainless steel is a corrosion-resistant alloy composed primarily of iron, chromium, and other elements such as nickel and molybdenum. This unique composition gives stainless steel its distinctive properties, including resistance to corrosion, high strength, durability, and aesthetic appeal.
These characteristics make stainless steel an ideal choice for piping systems in manufacturing plants, where exposure to corrosive chemicals, high temperatures, and harsh environments is common. Stainless steel piping offers longevity and reliability, reducing the risk of leaks, failures, and maintenance issues associated with traditional piping materials.
Challenges in Manufacturing Plants
Manufacturing plants face several challenges related to piping systems, including corrosion, degradation, and operational failures. Conventional piping materials such as carbon steel, PVC, and cast iron are susceptible to corrosion from chemicals, moisture, and abrasive substances, leading to leaks, contamination, and downtime.
The failure of piping systems can disrupt production schedules, result in costly repairs, and pose safety risks to personnel and the environment. Additionally, compliance with regulatory standards and environmental regulations adds further complexity to managing piping infrastructure in manufacturing plants.
Importance of Reliable Piping Solutions
Reliable piping solutions are essential for maintaining the continuous operation, productivity, and safety of manufacturing plants. Stainless steel piping addresses these requirements by offering superior corrosion resistance, durability, and longevity. By minimizing the risk of leaks and failures, stainless steel piping helps ensure regulatory compliance, environmental integrity, and worker safety.
Moreover, the reliability of stainless steel piping contributes to overall operational efficiency, reducing downtime and maintenance costs associated with repairs and replacements.
Applications of Stainless Steel Piping in Manufacturing Plants
Stainless steel piping finds diverse applications across various industries, including chemical processing, food and beverage production, pharmaceutical manufacturing, petrochemical plants, power generation facilities, and water treatment plants. In chemical processing plants, stainless steel piping is used to transport corrosive chemicals safely and efficiently. In the food and beverage industry, stainless steel piping maintains hygiene standards and prevents contamination of products.
Similarly, in pharmaceutical manufacturing, stainless steel piping ensures the integrity and purity of medicinal products. In petrochemical plants and power generation facilities, stainless steel piping withstands high temperatures and pressures, while in water treatment plants, it resists corrosion from harsh chemicals and environmental factors.
Factors Influencing Performance of Stainless Steel Piping
Several factors influence the performance of stainless steel piping systems, including material selection, design considerations, installation techniques, and maintenance practices. Proper material selection involves choosing the appropriate grade of stainless steel based on the specific requirements of the application, such as corrosion resistance, temperature tolerance, and mechanical strength.
Design considerations focus on optimizing flow efficiency, minimizing pressure losses, and preventing issues such as erosion and vibration. Installation techniques, including welding and joining methods, must adhere to industry standards and best practices to ensure the integrity and reliability of the piping system.
Emerging Trends and Innovations
The stainless steel industry is continually evolving, driven by advancements in manufacturing technologies, innovative designs, and sustainability initiatives. Advanced manufacturing techniques, such as additive manufacturing and laser welding, enable the production of complex and customized stainless steel components with improved properties and performance. Innovative piping designs, such as corrugated and spiral-welded pipes, optimize flow characteristics and reduce pressure losses, enhancing overall efficiency.
Integration of IoT (Internet of Things) and smart technologies enables real-time monitoring, predictive maintenance, and optimization of stainless steel piping systems, minimizing downtime and maximizing uptime. Moreover, sustainability initiatives, such as recycling and life cycle assessments, promote the use of stainless steel pipe fittings as an environmentally friendly and resource-efficient material in manufacturing plants.
Best Practices for Implementing Stainless Steel Piping Solutions
Implementing stainless steel piping solutions requires a holistic approach that encompasses collaboration, planning, quality assurance, and training. Manufacturers, engineers, and end-users must work together to assess project requirements, select suitable materials, and design efficient piping systems that meet regulatory standards and industry specifications.
Comprehensive risk assessment and planning are essential to identify potential hazards, mitigate risks, and ensure compliance with safety and environmental regulations. Quality assurance measures, including material testing, inspection, and certification, guarantee the integrity and reliability of stainless steel piping throughout its lifecycle. Furthermore, training and education programs equip personnel with the knowledge and skills required for proper installation, operation, and maintenance of stainless steel piping systems, thereby enhancing safety, efficiency, and performance.
Conclusion
Stainless steel piping solutions play a vital role in enhancing reliability and performance in manufacturing plants across various industries. By offering superior corrosion resistance, durability, and longevity, stainless steel piping addresses the challenges associated with traditional piping materials, ensuring continuous operation, productivity, and safety. As industries continue to evolve, embracing stainless steel piping solutions will be essential for achieving sustainable and efficient manufacturing processes. Moreover, ongoing innovations in manufacturing technologies, design practices, and sustainability initiatives will further enhance the performance and value of stainless steel piping in the years to come.
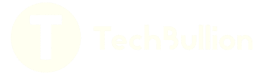