CIP systems provide quick, thorough, and dependable Cleaning for all process plant types. It is a way to clean whole pieces of industrial equipment or piping circuits without taking them apart.
The technical staff of WCSP offers premium quality CIP services. Cleaning in place (CIP) can be a very effective method. Automated CIP systems are often used in the food and beverage industry for routine Cleaning. The automated CIP system includes product transfer lines, processing tanks, homogenizers, mixers, blenders, and fillers. As we see, the Cedar Stone industry provides the best CIP system.
Manufacturing plants may benefit significantly from WCSP Cleaning in-place (CIP) technology.
What to clean, where to clean, how to clean, whom to hire to do the Cleaning, and what degree of competence is needed all make cleaning a highly technical endeavor.
It has improved product quality at a reduced cost via efficient and dependable Cleaning of process equipment and pipelines.
Automation, reproducibility, and dependability in the supply of cleaning solutions, rinse, and wash water to and through process equipment; also known as clean-in-place (CIP) technology. This process of plumbing, in turn, has enhanced the facility’s cleanliness and the final product’s quality.
When a processing system’s tanks, pumps, valves, filters, heat exchange units, and process piping can be cleaned entirely without being taken apart, it dramatically decreases cleaning costs. It limits handling chemicals, making for a safer working environment for plant employees. With manways, process piping valves, and tank-cleaning heads, we are better positioned to clean tanks and piping effectively and efficiently. This will help to prevent downtime, and costly repairs or replacements of equipment.
Preventing microbiological contamination by cleaning equipment surfaces is especially important for biological materials procedures. The importance of clean-in-place (CIP) systems must be balanced. CIP systems do more than keep things sanitary; they also eliminate debris like grit, scale, and organic matter that may impede processing efficiency. Equipment and operational concerns for CIP systems are outlined in this one-page guide for use in bioprocessing plants.
Appliances for removing contaminated water
CIP systems have a fluid supply that travels to an internal spray mechanism and then sprays the solution over the vessel walls. Static spray balls and fluid-driven orbital cleaners are the only examples of spray devices on the market. Tanks with a diameter of fewer than 15 feet are often cleaned using spray balls, which are high-flow, low-pressure devices, whereas larger tanks are cleaned with fluid-driven orbital cleaners and low-flow, high-pressure machines.
Tanks. Both 304L and 316L stainless steel are often used in tank construction. As a rule, CIP vessels do not need their inside polished. Agitators should be used in detergent tanks to facilitate the mixing of detergent solutions.
Pumps. The exact CIP solutions will likely be used throughout several unit operations and storage tanks, each with unique flow and pressure needs. To deal with this issue, parallel pump systems (those with varying flows and heads) or variable-speed drives (VSDs) might be used. Centrifugal pumps are the most common kind, and variable speed drives (VSDs) are commonplace in these machines. As certain CIP fluids must be heated to high temperatures, ensuring that your system meets the necessary net positive suction head (NPSH) criteria are essential. For spray nozzles and other machinery (heat exchangers, sterilizers, and more), it is necessary to calculate hydraulic losses using vendor data.
Piping. The correct design of CIP circuits, the capability to drain CIP lines, and the proper isolation of the CIP system from the process being cleaned are all crucial factors in the pipe design of CIP systems. The ideal length for dead legs is no more than two pipe diameters, and the system should be entirely drained. It’s essential to appropriately size lines for thoroughly turbulent flow. A typical speed range is between 5 and 7 ft/s since this is the norm in practice. Slopes should be added to all horizontal lines and installed in low spots. A pipe should have a pitch of at least 1/16 inch per foot. While choosing a valve, ensure there are no areas that cannot drain or any cracks that will not be cleaned. For pipe diameters 6 inches and less, there are “clean” ball valve styles. Hygienic butterfly-valve designs are an option for bigger sizes. Ideally, a block-and-bleed link or a line break would serve as the interface between the CIP system and the process.
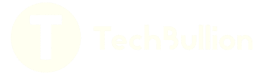