Robotics controls engineering is a critical field that combines principles of engineering, computer science, and robotics to develop control systems that govern the behavior of robots. As robots become more integral to various industries—from manufacturing to healthcare—the need for sophisticated control systems grows. These systems ensure that robots can operate efficiently, safely, and effectively in dynamic environments.
Understanding Robotics Controls Engineering
At its core, robotics controls engineering focuses on how robots are programmed to behave in response to various inputs. This discipline involves the development of algorithms and control strategies that enable robots to perform specific tasks while adapting to changes in their environment. Control systems can range from simple feedback loops to complex artificial intelligence algorithms that allow for advanced decision-making.
The Role of Control Systems
Control systems are essential for the functionality of robots. They help manage the robot’s movements, ensure stability, and enhance precision. There are two primary types of control systems in robotics: open-loop and closed-loop systems.
Open-Loop Control Systems: These systems operate without feedback. They execute commands based on predefined parameters. For example, a simple robotic arm that picks up an object at a set position without adjusting for any changes in the environment operates on an open-loop system.
Closed-Loop Control Systems: In contrast, closed-loop systems utilize feedback to adjust their operations. These systems continually monitor the robot’s performance and make real-time adjustments based on the data received. For example, a robotic vacuum cleaner that adjusts its path based on detected obstacles is using a closed-loop control system.
Key Components of Robotics Control Systems
The design of control systems for robots involves several key components:
Sensors: Sensors collect data about the robot’s environment, including distance, temperature, and motion. They provide the necessary information for the control system to make informed decisions.
Actuators:
Actuators are the components that enable movement in a robot. They convert control signals into physical motion, allowing the robot to perform tasks.
Controllers:
Controllers process the data from sensors and determine the appropriate actions for the actuators. They use algorithms to execute commands, ensuring that the robot behaves as intended.
Feedback Mechanisms:
Feedback loops are crucial for closed-loop systems. They allow the robot to compare its actual performance against desired outcomes, enabling real-time adjustments.
Technologies in Robotics Controls Engineering
Various technologies play a significant role in robotics controls engineering. These technologies enhance the efficiency and effectiveness of control systems.
PID Control
Proportional-Integral-Derivative (PID) control is one of the most widely used control strategies in robotics. PID controllers adjust their output based on three terms: the proportional term considers the current error, the integral term accounts for the cumulative error over time, and the derivative term predicts future errors. By tuning these parameters, engineers can create responsive control systems that maintain stability and accuracy.
Fuzzy Logic Control
Fuzzy logic control is a powerful approach that mimics human decision-making. Unlike traditional binary logic, fuzzy logic allows for degrees of truth, enabling robots to handle uncertain or imprecise information. This is particularly useful in situations where precise data may be challenging to obtain, such as in complex environments with varying conditions.
Neural Networks
Neural networks are increasingly being integrated into robotics controls engineering. These machine learning models can process large amounts of data and identify patterns, making them ideal for complex control tasks. By training neural networks with data from sensors, robots can learn to adapt their behavior based on past experiences, improving their performance over time.
Model Predictive Control (MPC)
Model Predictive Control is an advanced control strategy that uses a model of the system to predict future behavior. MPC evaluates potential future actions and selects the one that minimizes a cost function. This approach is particularly beneficial for robots operating in dynamic environments, as it allows for proactive decision-making and optimization.
Applications of Robotics Controls Engineering
The applications of robotics controls engineering are vast and varied, impacting numerous industries. Here are some of the key areas where robotics control systems are making a difference:
Manufacturing
In manufacturing, robots play a crucial role in automating processes. Robotics controls engineering ensures that industrial robots operate efficiently, performing tasks such as assembly, welding, and painting. Advanced control systems enhance precision, reduce errors, and increase production rates, ultimately leading to cost savings and improved quality.
Healthcare
In healthcare, robotics controls engineering is transforming patient care. Surgical robots, such as the da Vinci Surgical System, rely on sophisticated control systems to assist surgeons in performing minimally invasive procedures with precision. Rehabilitation robots help patients regain mobility by providing targeted support and exercises, guided by responsive control systems.
Autonomous Vehicles
The automotive industry is experiencing a significant shift towards automation, with autonomous vehicles becoming increasingly prevalent. Robotics controls engineering is at the heart of this transformation, ensuring that self-driving cars can navigate safely and efficiently. Control systems process data from various sensors, enabling vehicles to detect obstacles, adjust speeds, and make real-time decisions.
Agriculture
In agriculture, robotics technology is being employed to optimize farming practices. Autonomous drones and robotic harvesters rely on advanced control systems to monitor crops, apply pesticides, and harvest produce. These systems improve efficiency, reduce labor costs, and enhance sustainability in food production.
Service Robotics
Service robots are gaining popularity in various sectors, including hospitality, logistics, and retail. Robotics controls engineering enables these robots to interact with customers, navigate environments, and perform tasks such as cleaning or delivery. The development of responsive control systems enhances the overall user experience and ensures safe operation in dynamic settings.
Future Trends in Robotics Controls Engineering
As robotics technology continues to advance, several trends are shaping the future of robotics controls engineering:
Increased Autonomy
The push for increased autonomy in robots is driving advancements in control systems. As robots become more capable of performing complex tasks independently, the demand for sophisticated control algorithms will grow. Engineers will focus on developing systems that enable robots to adapt to changing environments and make decisions without human intervention.
Enhanced Human-Robot Interaction
The future of robotics will see improved human-robot interaction (HRI) capabilities. Engineers will work on developing intuitive control systems that allow robots to understand and respond to human commands naturally. This trend will enhance collaboration between humans and robots, particularly in settings such as healthcare and manufacturing.
Integration of AI and Machine Learning
The integration of artificial intelligence and machine learning into robotics controls engineering is a significant trend. By leveraging these technologies, engineers can develop control systems that learn from data and improve over time. This will enable robots to perform more complex tasks and adapt to new situations with greater ease.
Focus on Safety and Reliability
As robots become more integrated into daily life, ensuring safety and reliability will be paramount. Engineers will prioritize developing robust control systems that can handle failures and uncertainties. This includes implementing fail-safe mechanisms and redundancy in control strategies to minimize risks in critical applications.
Collaborative Robots (Cobots)
The rise of collaborative robots (cobots) is another important trend. These robots are designed to work alongside humans safely and effectively. The development of control systems that prioritize human safety and interaction will be crucial for the success of cobots in various industries.
Conclusion
Robotics controls engineering is a vital discipline that underpins the functionality and effectiveness of robots in diverse applications. Through the development of advanced control systems, engineers are enabling robots to operate autonomously, adapt to changing environments, and collaborate with humans. As technology continues to evolve, the field of robotics controls engineering will play a crucial role in shaping the future of automation, enhancing efficiency, and improving quality of life.
The innovations and trends discussed in this article highlight the exciting potential of robotics controls engineering. By embracing advancements in AI, machine learning, and human-robot interaction, we can look forward to a future where robots become increasingly integral to our lives and industries. As we navigate this transformative landscape, the importance of effective and responsive control systems will be paramount in unlocking the full potential of robotics technology.
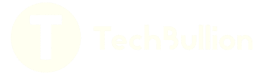