A CMMS or computerized maintenance management system is a valuable innovation for every modern industrial business. But, a common question remains: Is the cost of CMMS software and system implementation worth it? Are the cost savings and other benefits from CMMS significant and provide a positive return on investment (ROI)? In this post, we provide a detailed look into how CMMS provides cost savings and financial benefits for a facility. You’ll also learn the common methods of estimating the ROI of CMMS.
What Can a CMMS Do?
Before we look into the financial benefits, here’s a quick refresher on CMMS and what it can do for you. A robust CMMS like Redlist, for example, can:
- Take the place of manual recording systems like Excel sheets and physical paper forms to track and monitor maintenance tasks such as repairs, inspections, cleaning, etc.
- Store data on all assets, including specifications and user manuals, repair and maintenance history, spare parts requirements, preventive maintenance information, testing or calibration records, etc.
- Provide a digital workspace where managers can create schedules and work orders that technicians and other personnel can view, allowing faster and more accurate interaction and communication within the team.
- Help manage the inventory of maintenance materials like spare parts, tools, lubricants, cleaning supplies, etc., allowing managers to monitor stock availability and control ordering schedules.
- Integrate maintenance with other business processes like accounting, human resources, engineering, operations, purchasing, logistics, etc. This allows different departments to view or interact with maintenance data to accomplish critical tasks accurately.
Cost Savings and Financial Benefits of Implementing CMMS
Below is a list of the ways CMMS providing cost savings and financial benefits:
Reduced Downtime
Downtime equals decreased productivity and loss of revenue. An hour of downtime is estimated to cost a facility $10,000, and this amount can be higher for high-value assets. Thus, reducing downtime means increasing asset productivity and increasing revenue. CMMS reduces downtime by:
- Faster information transfer – Managers and technicians communicate faster and more accurately through CMMS, resolving equipment failure faster.
- Better planning – CMMS makes planning maintenance operations easier, allowing facilities to focus on preventive maintenance and reducing unplanned downtime.
- Availability of resources – CMMS lets you assign maintenance resources such as technicians, materials, and parts more efficiently, ensuring that these are available whenever needed, resulting in faster resolution of failure or breakdowns.
- Historical reference – CMMS lets you keep records of past maintenance work, providing accessible critical information that can shorten the troubleshooting time and speed up the repair or maintenance process, thus, reducing downtime.
Reduced Labor Costs
Maintenance relies on labor to execute work orders and necessary operations. And maintenance labor can come in the form of technical or specialized skills which can be costly. Managing these types of labor is necessary to minimize such costs. CMMS reduces labor costs by:
- Reducing overtime – CMMS helps plan work orders better and reduce technician overtime by improving workplace communication and information transfer. Managers can monitor work completion and adjust schedules in real-time to optimize labor and reduce overtime.
- Minimizing unplanned or reactive maintenance – Reactive maintenance, or repairing assets when they fail, often comes with costly and recurrent labor. CMMS minimizes reactive maintenance by allowing you to focus on preventive maintenance
Improved Asset Reliability
By promoting preventive maintenance, CMMS implementation can help facilities improve asset reliability. Improved asset reliability is the bottom line of any competitive facility because it ultimately leads to reduced maintenance costs, increased productivity, and optimized operations. CMMS improves asset reliability by:
- Providing an accessible database of asset information – CMMS makes it easy for reliability specialists to extract metrics and key performance indicators (KPIs) essential for reliability tracking and improvements.
- Generating analytics accurately – CMMS computing technology can analyze and provide reports that can help managers and decision-makers formulate plans and strategies based on actual asset data.
- Connecting with other data systems – CMMS allows you to share maintenance data with other data processing systems to analyze asset reliability further. For example, accounting can look into maintenance data for more efficient budgeting and inventory of assets and components. Tracking and logistics can also use maintenance work order data for better scheduling and asset availability.
Improved Inventory Management
Poor inventory management of maintenance materials results in costly mistakes, expensive deliveries, and overstocking that ties too much capital. CMMS can improve inventory management and reduce inventory costs by:
- Real-time inventory updates – CMMS allows users to update the inventory levels of maintenance, repair, and operations (MRO) items as they are used. This makes it easy to maintain optimum stock levels and prevent ordering errors.
- Automating the ordering process – CMMS like Redlist have automated functions like creating orders when stocks of MRO items reach critical levels. This saves ordering time and costs that often come with urgent deliveries.
- Forecasting requirements – CMMS lets you analyze inventory usage to forecast MRO needs, helping you plan budgets more efficiently and implement steps to minimize ordering costs. For example, knowing your yearly stock requirements can help you request discounts on bulk orders or shipping costs.
Calculating the ROI of CMMS
The expense of CMMS can be justified by calculating the ROI. To do so, you need the following data:
- Asset maintenance expenses or amount spent on repairs, parts replacements, cleaning, etc.
- Inventory of MRO items including total costs
- Overtime of maintenance employees including the type of maintenance work executed
- Downtime caused by failure and planned or unplanned maintenance work
- Overall maintenance expense
Below are the ways to calculate the ROI, choose one that best fits your organization and available data:
ROI by Maintenance Expense
You can estimate the ROI of CMMS if you have the data on all maintenance expenses (including MRO and overtime expenses) before and after CMMS implementation. You subtract maintenance expenses after CMMS from before CMMS and divide them by the cost of CMMS. To illustrate, if maintenance expenses before CMMS are $200,000 and $100,000 after, and the cost of CMMS is $5,000, the ROI is 1900%.
ROI = (Pre-CMMS Maintenance Cost – Post-CMMS Maintenance Cost – CMMS Cost) / CMMS Cost X 100
For example: ROI = ($200,000 – $100,000 – $5,000) / $5,000 x 100 = 1900%
ROI by Downtime Cost
You can also estimate the ROI from CMMS implementation by calculating the cost of downtime. Downtime cost is calculated by multiplying the total downtime in minutes with an operation’s cost per minute. Cost per minute can vary from $400 to $9,000 depending on the industry type. Calculate ROI by subtracting downtime cost after CMMS from downtime costs before CMMS and dividing it by the cost of CMMS. To illustrate, if your downtime costs went from $30,000 to $5,000 and the cost of CMMS is $5,000, the ROI is 400%.
ROI = (Pre-CMMS Downtime Cost – Post-CMMS Downtime Cost – CMMS Cost) / CMMS Cost X 100
For example: ROI = ($30,000 – $5,000 – $5,000) / $5,000 X 100 = 400%
Evaluating CMMS Implementation
Understandably, you need to know if your CMMS is worth the money and effort to implement. You may see improvements in your maintenance management, but are they significant and do they equate to monetary value for your company? This is why evaluating your CMMS is critical after implementation. With Redlist’s CMMS software, evaluating and monitoring the effect of your CMMS implementation is a continuous and easy process. You can use the data gathered from using this system to compute total expenses, downtime, and other maintenance metrics. Redlist can help you analyze the ROI and other valuable insights to improve your maintenance management further. Schedule a free demo to experience Redlist today!
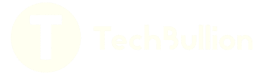