Introduction
Efficiency and cost-effectiveness are critical to success in today’s fiercely competitive industrial sector. Manufacturers are using cutting-edge technology solutions, such Computerized Maintenance Management System (CMMS) software, to achieve a competitive advantage. This potent technology revolutionizes production processes by streamlining maintenance procedures, increasing productivity, and lowering costs. In this article, we’ll examine how CMMS software has significantly improved manufacturing productivity and highlight a startling figure that demonstrates its importance.
How does CMMS software work?
CMMS software solution also known as CMMS, or Computerized Maintenance Management System, is created to optimize and expedite maintenance processes across a variety of sectors. It offers a unified platform for organizing and managing work orders, inventories, assets, and maintenance activities, which boosts asset reliability, cost-effectiveness, and efficiency.
At its foundation, CMMS software functions as an extensive database that houses vital data about an organization’s assets, including its infrastructure, machines, and facilities. Details about the asset, maintenance history, warranty information, and instructions are all included in this data. By centralizing and digitizing this data, CMMS software enables simple access, tracking, and analysis, enabling maintenance teams to take preemptive actions and well-informed judgments.
Work order management is one of the main features of CMMS software. Users can use it to make, assign, and follow up on work orders for maintenance projects. Work orders can be created for inspections, repairs, preventative maintenance, corrective maintenance, and other maintenance tasks. By automating the workflow and ensuring that work orders are correctly documented, scheduled, and carried out, CMMS software lowers the likelihood of forgotten jobs or delays.
Preventive maintenance is another essential component of CMMS software. It enables businesses to create and manage preventative maintenance plans based on consumer usage trends, manufacturer advice, and industry best practices. CMMS software helps reduce unexpected downtime, increase asset longevity, and boost overall productivity by routinely inspecting, repairing, and maintaining equipment before they fail.
By keeping track of the replacement parts, supplies, and materials needed for maintenance tasks, CMMS software also aids with inventory management. It supports the creation of purchase orders, tracking stock availability, and inventory level optimization.
CMMS software is a versatile solution that automates workflows, centralizes data, enables preventive maintenance, improves inventory management, and offers insightful data to revolutionize maintenance operations. Organizations may increase productivity, cut expenses, and extend the lifespan and reliability of their assets by utilizing CMMS software.
Streamlining Maintenance Processes
The management and optimization of maintenance procedures is one of the main difficulties that manufacturers encounter. Traditional methods that rely on manual record-keeping and reactive maintenance techniques can increase expenses, cause equipment downtime, and result in inefficiencies. However, manufacturers may plan preventative maintenance, manage maintenance jobs proactively, and monitor asset performance in real-time with CMMS software.
By automating work order production, streamlining inventory management, and offering centralized access to vital information, CMMS software promotes simplified operations. The history of assets can be followed, historical data can be accessed, and maintenance teams can more effectively plan maintenance tasks. Process simplification not only lowers errors and saves time, but also improves overall operational effectiveness.
Improving Asset Reliability
To increase output and satisfy client demands, manufacturers primarily rely on their assets. Any unanticipated equipment breakdown or unscheduled downtime can have a negative impact on output, client satisfaction, and profitability. The reduction of unplanned downtime and enhancement of asset reliability are both made possible by CMMS software.
Manufacturers can proactively plan preventive maintenance jobs based on usage trends, manufacturer recommendations, and industry best practices by deploying CMMS software. This increases the lifespan of equipment and lowers the risk of breakdowns by identifying and resolving possible problems before they become serious.
Additionally, manufacturers can monitor asset performance measures like mean time between failures (MTBF) and mean time to repair (MTTR) using CMMS software. These measurements offer perceptions into asset dependability and support manufacturers in making data-driven decisions for resource allocation and maintenance strategy optimization.
Lowering expenses
Manufacturers place a high premium on cutting costs, and CMMS software shows to be an effective instrument in reaching this goal. CMMS software aids in limiting equipment downtime and enables preventive maintenance, which lowers the cost of repairs, emergency maintenance costs, and production interruptions.
The cost-saving potential of CMMS software in manufacturing operations is shown by a noteworthy figure. Companies who deployed CMMS software reported an average cost reduction of 15% in their maintenance operations, according to a survey performed by a top industry association. This decrease can be attributable to greater inventory management made possible by CMMS software, improved equipment reliability, and optimized maintenance scheduling.
For maintenance scheduling several organizations use preventive maintenance software. It is also an effective tool for avoiding sudden equipment failure and creating maintenance plans & check work orders in real time as well.
Furthermore, CMMS software gives manufacturers insights into maintenance costs, enabling them to keep track of expenditures, spot areas of overspending, and make wise choices to manage maintenance budgets. Manufacturers can avoid expensive breakdowns and increase the longevity of their assets, further lowering overall maintenance costs, by emphasizing preventative maintenance over reactive repairs.
Conclusion:
In conclusion, CMMS software transforms industrial processes by increasing productivity and reducing expenses. Manufacturers can optimize operations, increase productivity, and stay ahead in a fiercely competitive market thanks to CMMS software’s streamlined maintenance processes, increased asset reliability, and decreased costs. These are just a few of the benefits of CMMS Software.
According to the Statista, “As of that time, 65 percent of the respondents indicated that CMMS helps improve the overall efficiency of plant manufacturing.” This figure highlights the important role that CMMS software plays in enhancing manufacturing productivity and cost-effectiveness. Manufacturers may improve their operations, maximize asset performance, and achieve sustainable success in today’s dynamic industrial industry by implementing CMMS software.
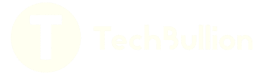