Introduction: Precision Engineering 4.0 refers to the new era of manufacturing where artificial intelligence (AI), advanced automation and the Internet of Things converge to produce extremely accurate parts and components. In this paradigm, smart factories leverage robotics, sensors and real-time data analytics (Industry 4.0 technologies) to craft precision manufacturing processes with micron-level tolerances. Precision parts for aerospace, medical or electronics often require tolerances of just a few microns, and AI in manufacturing helps achieve this reliably. By linking every step – from CAD models to CNC machining – with AI-driven insights and feedback, manufacturers boost throughput and quality. In short, precision engineering now means using data and AI to make ultra-precise parts faster, cheaper and greener.
Core Value: Measurable Benefits of AI-Driven Precision Manufacturing
Modern precision shops use collaborative robots and AI-guided systems at every stage to enforce extremely tight tolerances. AI-driven Industry 4.0 systems significantly boost output and quality: for example, AI-powered robots now perform complex assembly tasks with precision, boosting production rates and reducing defects. These intelligent systems detect issues before they cause downtime and adjust parameters on the fly, setting new standards for throughput and consistency. The result is dramatic improvements in traditional KPIs, such as:
- Yield & Quality: First-pass yield improvements of ~40% have been reported; automated vision inspection can detect 90% more defects than human inspection.
- Throughput & Downtime: Production output can rise (e.g. +6% in one automotive plant) and overall equipment effectiveness (OEE) gains of ~11% have been documented. At the same time, unplanned downtime drops dramatically (–25% in some cases), and total downtime waste can fall by over 50%.
- Cost & ROI: Smarter processes lower unit costs (for instance, a –3.5% cost-per-unit reduction was seen at a connected plant). In one precision-machining SME, AI-driven integration saved about £420K in three years (paying back the investment in under a year).
- Flexibility & Speed: AI-run “microfactories” can be set up in weeks instead of months. In one case, a new aerospace workshop was ready in 2 weeks vs the normal 3–6 months, and staff requirements shrank from 50 skilled workers to just 12.
- Sustainability: Smart automation cuts waste and energy use. For example, sensors and AI can trim energy/GHG use – one system cut carbon footprint by ~30% and a case study saw a 43% drop in CO₂ emissions after going smart.
- Efficiency: Some AI-enhanced lines now run above 90% OEE, and one study reported a 47% jump in machine utilization after installing Industry 4.0 systems.
These metrics illustrate how Industry 4.0 technologies unlock real value in precision manufacturing: higher yield, faster throughput, lower scrap, and better resource efficiency.
Data Proof: Case Studies and Industry Examples
Real-world implementations back up these claims with hard data. For instance, the Watch Out “microfactory” system (used by LISI Group for aerospace fasteners) cuts costs and carbon footprint by ~30% while running 24% of the previous labor force. Its autonomous cells use AI and sensors to self-optimize, enabling round-the-clock production with drastically fewer operators. In practical terms, what once took 50 machinists can now run on 12 staffers, and setup time falls from months to mere weeks.
Similarly, a peer-reviewed study of a precision-machining SME measured the impact of a six-stage smart-factory rollout. After three years of AI and IoT upgrades, machine utilization jumped ~47% and downtime waste fell 53%. This lifted productivity and cut operating costs by about £420K, giving a payback under 1 year.
Major manufacturers report comparable gains. In automotive, one luxury car plant used AI dashboards to power predictive maintenance, slashing unplanned downtime by ~25%. Another connected plant raised output ~6% by networking all machines on a single analytics system. In quality control, Ford’s implementation of an AI vision system (JAI cameras on the paint line) improved defect detection by 90% versus manual inspection. Bosch, using a flexible robot-inspection cell, now exceeds 90% OEE at the line.
Taken together, these cases show that AI-driven precision engineering isn’t hypothetical – it’s delivering double-digit improvements in key KPIs (yield, throughput, uptime and ROI) across industries.
Future Outlook: The Next 5–10 Years
Looking ahead, the convergence of AI, automation and precision manufacturing will only accelerate. Key trends and possibilities include:
- Intelligent Robotics & Cobots:
Robots will get smarter and more collaborative. Next-gen cobots can adapt to changing production needs and safely work alongside humans, handling more complex assembly and machining tasks. AI-enabled robots will boost production rates and slash defects.
- Digital Twins & Simulation: Virtual replicas of machines and factories will enable engineers to simulate and optimize processes in software before committing to hardware. Digital twins will help predict failures and fine-tune operations without stopping production.
- AI Quality Control & Analytics: Automated vision systems powered by deep learning will catch even tiny flaws that humans miss. Combined with predictive analytics, factories will preempt issues – for example, dynamic models can forecast when a tool will drift out of tolerance and trigger recalibration, essentially eliminating scrap over time.
- Edge Computing & IIoT: As more sensors come online, data will be processed on-site (edge) for instant response. This real-time analytics backbone will underpin fast decision-making – from optimizing cutting parameters mid-process to self-adjusting robots if a vibration spike occurs.
- Sustainability & Green Manufacturing:
AI will drive the industry’s environmental goals. Advanced algorithms will continuously optimize energy use (turning off idle machines, adjusting power draw, etc.) and minimize material waste by precise demand forecasting. In future plants, carbon emissions may be tracked in real time and actively reduced, as AI suggests process tweaks to hit sustainability targets
- Customization & Agility: With AI and automation, custom “batch of one” manufacturing becomes feasible. Systems can rapidly switch production modes, allowing more complex part families and personalization while maintaining precision.
- Challenges: Significant hurdles remain. Up-front costs and legacy systems can slow adoption, and companies must invest in new infrastructure and software. The skills gap is also real: workers need retraining to oversee AI-driven processes, shifting from manual tasks to data analysis and machine supervision. Cybersecurity and data governance become critical as more operational technology goes online.
Overall, experts predict that AI-integrated factories will set the industry pace by 2030. According to one analysis, combining AI with automation “promises to redefine productivity standards, cut downtime, and open new possibilities for innovation”. In this future, manufacturers that embrace data-driven precision can expect faster cycles, tighter tolerances and a smaller environmental footprint – provided they prepare their people and systems for the change.
Conclusion – Moving Forward with Precision Automation
The evidence is clear: AI-driven manufacturing is raising the bar for precision engineering. Across real factories and studies, companies are seeing quantifiable improvements – better yields, lower defect rates, higher throughput and significant cost savings. These gains hold true for small precision shops and large factories alike. As we’ve seen, smart automation can even turn labor shortages into an advantage, enabling continuous (24/7) production with far fewer operators.
Manufacturers of precision parts should therefore seriously explore AI and Industry 4.0 solutions. Now is the time to pilot smart sensors, machine learning quality control, and robotic automation in your own processes. The benefits – from micron-accurate parts to faster lead times and greener operations – are proven. In a competitive market, adopting precision automation is no longer optional but a strategic necessity. Take the next step toward AI-enabled precision manufacturing to secure higher performance and cost-effectiveness for your future operations.
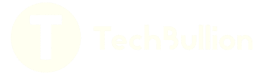