Selecting the right pneumatic valve is crucial for optimizing the performance and efficiency of industrial systems. In this guide, we will walk you through the essential steps to make an informed valve selection, covering everything from understanding different valve types, such as directional control, ball, and butterfly valves, to the key factors that influence your decision, including material compatibility, environmental conditions, and sizing requirements. We’ll also highlight common mistakes to avoid, such as oversizing or neglecting maintenance needs, and provide a step-by-step process to help you choose the perfect valve for your system’s needs. With this knowledge, you can ensure reliable, safe, and cost-effective operation of your pneumatic systems.
What Are Pneumatic Valves?
Pneumatic valves are devices designed to manage the flow of compressed air within a pneumatic system. They control the direction, pressure, and flow rate of air, enabling precise operation of pneumatic actuators, cylinders, and other components. By regulating airflow, these valves ensure that pneumatic systems function efficiently and safely.Â
Why Pneumatic Valves Matter in Industrial Systems
Pneumatic systems offer several advantages that make them integral to industrial operations:
- Speed: Pneumatic systems can actuate components rapidly, making them ideal for applications requiring quick response times.Â
- Reliability: Pneumatic valves are known for their durability and reliability, making them suitable for demanding industrial environments.Â
- Safety: Operating on compressed air reduces the risk of fire hazards associated with hydraulic systems, enhancing workplace safety.Â
Types of Pneumatic Valves
Pneumatic valves are integral to controlling airflow within pneumatic systems, each type serving specific functions to meet diverse industrial requirements. Below is an overview of the primary types:
Directional Control Valves
Directional control valves manage the path of compressed air, directing it to various parts of a system. They are categorized based on the number of ports and positions:
- 2-Way Valves: These valves have two ports and two positions, allowing air to flow in one direction and blocking it in the other. They are commonly used for simple on/off control applications.Â
- 3-Way Valves: Featuring three ports and two positions, these valves can control the flow to a single-acting cylinder or serve as a pilot for other valves. They are often used in pairs to operate double-acting cylinders.Â
- 4-Way Valves: With four ports and two or more positions, these valves are essential for controlling double-acting cylinders, enabling both extension and retraction. They are widely used in applications requiring precise control of actuator movements.Â
Ball Valves
Ball valves utilize a rotating ball with a hole through its center to control airflow. They are primarily used for on/off control, providing quick shut-off capabilities with minimal pressure drop. Their robust design makes them suitable for applications where a reliable seal is essential.Â
Butterfly Valves
Butterfly valves consist of a disc mounted on a shaft, which rotates to control airflow. They are ideal for high-flow, low-pressure systems due to their lightweight construction and quick operation. Commonly used in large-scale industrial applications, butterfly valves offer a cost-effective solution for regulating flow.Â
Solenoid Valves
Solenoid valves are electrically operated, using an electromagnetic coil to control the valve’s position. They are integral to electropneumatic integration, enabling automated control of pneumatic systems. Solenoid valves are widely used in industrial automation for their precision and reliability.Â
Specialty Valves
Specialty valves cater to specific applications and include:
- Needle Valves: These valves provide precise flow control, making them ideal for applications requiring fine adjustments.Â
- Pinch Valves: Utilizing a flexible sleeve, pinch valves control flow by pinching the sleeve closed, suitable for handling abrasive or corrosive materials.Â
- Proportional Valves: These valves adjust flow proportionally to an input signal, allowing for precise control in applications such as robotics and automated manufacturing.Â
Key Factors to Consider When Selecting a Pneumatic Valve
Selecting the appropriate pneumatic valve is crucial for ensuring optimal performance, safety, and efficiency in industrial systems. The following factors should be carefully evaluated during the selection process:
Application Requirements
- Pressure and Temperature: Assess the operating pressure and temperature ranges of your system to ensure the valve can withstand these conditions without compromising performance.
- Media Type: Identify the type of media—such as air, gas, or liquid—that the valve will control. This determination is essential for selecting a valve compatible with the specific media and its properties.Â
Operating Environment
- Corrosive Conditions: If the valve will be exposed to corrosive substances, materials resistant to corrosion are necessary to prevent degradation and ensure longevity.
- Explosive Atmospheres: In environments with explosive risks, valves must meet stringent safety standards to prevent ignition and ensure safe operation.
- Extreme Temperatures: For applications involving high or low temperatures, selecting valves designed to operate effectively under such conditions is vital.
Valve Material Compatibility
- Metals: Materials like stainless steel and brass offer durability and resistance to various chemicals and temperatures. Stainless steel is particularly suitable for high-pressure and high-temperature applications.
- Polymers: Materials such as PTFE and Nylon provide excellent chemical resistance and are ideal for applications involving aggressive chemicals or where metal contamination is a concern.
Valve Size and Flow Rate (Cv Value)
- Sizing Calculations: Proper valve sizing is essential for system efficiency. The flow coefficient (Cv) is a critical parameter that indicates the valve’s capacity to pass fluid. Calculating the required Cv involves considering factors like desired flow rate, pressure drop, and fluid properties. An undersized valve can lead to inadequate flow, while an oversized valve may result in excessive pressure drop and energy loss.Â
Actuation Method
- Manual Actuation: Suitable for applications where infrequent operation is required.
- Solenoid Actuation: Ideal for automated systems requiring remote control and precise operation.
- Pneumatic Actuation: Utilizes compressed air for actuation, offering rapid response times and suitability for hazardous environments.
Compliance and Certifications
- Industry Standards: Ensure the valve complies with relevant standards such as ISO, ANSI, or ATEX, which govern quality, safety, and performance.
- Certifications: Verify that the valve has the necessary certifications for your specific application, especially in regulated industries.
By meticulously evaluating these factors, you can select a pneumatic valve that aligns with your system’s requirements, ensuring reliable and efficient operation.
(Learn how to choose the right pneumatic valve accessories for your system.)
Step-by-Step Pneumatic Valve Selection Process
Selecting the appropriate pneumatic valve is crucial for ensuring optimal performance, safety, and efficiency in industrial systems. The following step-by-step guide outlines the key considerations to assist in making an informed decision:
Define Your System Requirements
- Media Type: Identify the fluid—such as air, gas, or liquid—that the valve will control. This determination is essential for selecting a valve compatible with the specific media and its properties.Â
- Operating Conditions: Assess the operating pressure and temperature ranges of your system to ensure the valve can withstand these conditions without compromising performance.
Evaluate Valve Types and Configurations
- Valve Functionality: Determine the required valve function, such as on/off control, flow regulation, or directional control. This will guide you toward the appropriate valve type, such as ball, butterfly, or solenoid valves.Â
- Actuation Method: Decide on the actuation method—manual, solenoid, or pneumatic—based on your system’s automation needs and control requirements.
Match Materials to Media and Environment
- Material Compatibility: Select valve materials that are compatible with the media to prevent corrosion and ensure longevity. For instance, stainless steel is suitable for high-pressure and high-temperature applications, while PTFE is ideal for aggressive chemicals.Â
- Environmental Considerations: Ensure the valve materials and coatings are suitable for the operating environment, including factors like exposure to chemicals, extreme temperatures, and potential for corrosion.
Calculate Flow and Pressure Needs
- Flow Requirements: Determine the required flow rate for your application to ensure the valve can handle the necessary volume without causing excessive pressure drop.
- Pressure Considerations: Assess the system’s pressure requirements to select a valve that can operate effectively within the specified pressure range.
Verify Compliance and Safety Standards
- Industry Standards: Ensure the selected valve complies with relevant industry standards such as ISO, ANSI, or ATEX, which govern quality, safety, and performance.
- Certifications: Verify that the valve has the necessary certifications for your specific application, especially in regulated industries, to ensure safety and reliability.
Common Mistakes to Avoid in Pneumatic Valve Selection
Selecting the appropriate pneumatic valve is crucial for ensuring optimal performance and longevity of your system. Avoiding common pitfalls can prevent inefficiencies, increased costs, and potential system failures. Here are key mistakes to watch out for:
Oversizing or Undersizing Valves
- Oversizing: Choosing a valve with a larger capacity than necessary can lead to increased costs and wasted energy. Oversized valves may also result in slower response times and reduced control precision.
- Undersizing: Opting for a valve that’s too small can restrict airflow, causing pressure drops, reduced system efficiency, and potential damage to components. An undersized valve may also struggle to handle peak flow rates, leading to operational issues.
Ignoring Environmental Factors
- Humidity: High moisture levels can cause corrosion and damage internal components. Selecting valves with appropriate seals and materials resistant to moisture is essential.
- Dust and Contaminants: Particulate matter can infiltrate valves, leading to wear, blockages, and malfunctions. Implementing proper filtration and choosing valves with suitable ingress protection (IP) ratings can mitigate these risks.
Material Incompatibility with Media
- Chemical Resistance: Using valves made from materials incompatible with the media can result in corrosion, degradation, and leaks. For instance, certain plastics may not withstand aggressive chemicals, while metals might corrode in acidic environments.
- Temperature Tolerance: Materials must be chosen based on the operating temperature range. For example, rubber seals may degrade at high temperatures, while metals might become brittle at low temperatures.
Neglecting Maintenance Requirements
- Accessibility: Selecting valves that are difficult to access can complicate maintenance tasks, leading to extended downtime and increased labor costs.
- Serviceability: Valves with non-replaceable parts or those requiring specialized tools for maintenance can increase operational costs and downtime.
Conclusion
In conclusion, selecting the right pneumatic valve requires careful consideration of various factors such as system requirements, valve types, material compatibility, environmental conditions, and sizing needs. By following a systematic selection process and avoiding common mistakes like oversizing or material incompatibility, you can ensure optimal valve performance and long-term reliability. Understanding the specific needs of your system and adhering to industry standards will not only improve efficiency but also prevent costly failures and maintenance issues. Armed with this knowledge, you can confidently make the best valve choice for your pneumatic systems, ensuring smooth, safe, and efficient operations.
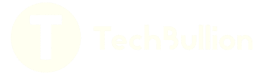