Industrial automation engineering is reshaping the way modern manufacturing operates. By integrating advanced technologies like robotics, artificial intelligence (AI), and machine learning (ML), industrial automation engineers create systems that perform repetitive tasks with precision, efficiency, and speed. These innovations are essential for businesses seeking to stay competitive in a global market.
Understanding Industrial Automation Engineering
At its core, industrial automation refers to the use of technology to control and operate manufacturing systems with minimal human intervention. This involves designing, programming, and deploying hardware and software solutions to automate routine tasks that were once performed manually. The goal of industrial automation is to increase productivity, reduce costs, and improve overall quality while ensuring safety and compliance with industry standards.
Automation engineers are responsible for developing and implementing these systems. They create automated machinery, design control systems, and program software to streamline manufacturing processes. This field requires a solid foundation in electrical and mechanical engineering, computer science, and industrial systems.
Key Technologies in Industrial Automation
Several key technologies form the backbone of industrial automation engineering. These technologies enable seamless integration of hardware and software systems to automate manufacturing tasks. Some of the most critical technologies include:
Robotics
Robots are a key component of modern manufacturing automation. They are used to perform repetitive, high-precision tasks such as assembly, welding, painting, and packaging. Robots can operate 24/7 without fatigue, significantly increasing production rates and maintaining consistency. Industrial automation engineers design robotic systems that are flexible, scalable, and capable of adapting to changing production requirements.
Programmable Logic Controllers (PLCs)
PLCs are specialized computers used to control industrial machinery. They are programmed to execute specific tasks, such as controlling motors, sensors, and actuators. PLCs are reliable, robust, and suitable for harsh industrial environments. They play a critical role in the automation of processes such as conveyor systems, manufacturing lines, and machine tools.
Human-Machine Interfaces (HMIs)
HMIs are interfaces that allow human operators to interact with automated systems. These interfaces provide real-time data on system performance, allowing operators to monitor and control processes. HMI systems are designed to be user-friendly, ensuring that workers can easily oversee automated processes without requiring extensive technical knowledge.
Artificial Intelligence and Machine Learning
AI and ML are becoming increasingly important in industrial automation. These technologies enable machines to learn from data, make decisions, and optimize processes in real time. AI-powered automation systems can analyze sensor data, detect anomalies, and adjust operations to improve efficiency. By integrating AI and ML into manufacturing systems, engineers can create smarter and more adaptable automation solutions.
Supervisory Control and Data Acquisition (SCADA) Systems
SCADA systems are used to monitor and control industrial processes in real time. They collect data from sensors and devices across a manufacturing facility, providing engineers and operators with a comprehensive view of operations. SCADA systems are essential for ensuring that automated processes run smoothly and that any issues are quickly identified and addressed.
Advantages of Automating Manufacturing Processes
Industrial automation brings numerous advantages to manufacturing. By automating repetitive and time-consuming tasks, businesses can improve efficiency, reduce errors, and lower costs. Below are some of the key benefits of automating manufacturing processes:
Increased Productivity
Automation allows manufacturing plants to operate continuously, without the limitations of human labor. Robots and automated systems can work around the clock, increasing production rates and throughput. This results in shorter lead times and the ability to meet customer demands more effectively.
Improved Precision and Quality
Automated systems can perform tasks with a level of precision that is difficult for human workers to match. This is especially important in industries like electronics and automotive manufacturing, where small errors can lead to costly defects. By automating processes, manufacturers can achieve consistent quality and reduce the risk of mistakes.
Reduced Labor Costs
One of the most immediate benefits of industrial automation is the reduction in labor costs. Automating tasks that were once performed manually allows manufacturers to reduce their reliance on human workers for repetitive, low-skill tasks. This not only lowers labor costs but also allows companies to reallocate human resources to higher-value tasks, such as product design, quality control, and innovation.
Enhanced Safety
Manufacturing environments can be hazardous, with risks such as heavy machinery, chemicals, and repetitive motion injuries. Automation helps to reduce these risks by minimizing human involvement in dangerous or physically demanding tasks. Robots can be used in environments that are hazardous to humans, such as handling toxic materials or operating in extreme temperatures.
Real-Time Monitoring and Optimization
With the integration of AI, ML, and SCADA systems, automated manufacturing processes can be continuously monitored and optimized in real time. Engineers can collect and analyze data on machine performance, energy consumption, and output quality, allowing for proactive maintenance and adjustments. This leads to higher efficiency and lower downtime.
Challenges in Industrial Automation Engineering
While industrial automation brings numerous benefits, it also presents several challenges. Engineers must navigate technical, financial, and operational hurdles when designing and implementing automated systems. Some of the primary challenges include:
Complexity of System Integration
Integrating new automation technologies into existing manufacturing systems can be complex and time-consuming. Engineers must ensure that the various hardware and software components work together seamlessly. This often requires custom solutions, careful planning, and thorough testing to avoid compatibility issues.
High Initial Investment
Implementing industrial automation can be expensive, particularly for small and medium-sized enterprises (SMEs). The cost of robotic systems, PLCs, and AI-powered software can be substantial. Additionally, there are costs associated with installation, training, and maintenance. However, while the upfront investment may be high, the long-term cost savings and productivity improvements often justify the expense.
Workforce Training and Adaptation
As manufacturing becomes more automated, the skills required to operate and maintain automated systems change. Workers must be trained to interact with new technologies, such as HMIs and SCADA systems. In some cases, workers may need to learn how to program or troubleshoot automated machinery. This shift in workforce requirements can lead to challenges in adaptation and potential job displacement.
Cybersecurity Risks
As industrial automation systems become more connected through the Industrial Internet of Things (IIoT), they are vulnerable to cybersecurity threats. Protecting automated systems from cyberattacks is critical to maintaining operational integrity. Engineers must implement robust cybersecurity protocols to safeguard data and ensure that automated processes are not compromised.
The Future of Industrial Automation
The future of industrial automation engineering looks promising, with continued advancements in AI, robotics, and connectivity. As the Fourth Industrial Revolution (Industry 4.0) progresses, smart factories will become the norm, with machines communicating and making decisions autonomously. The rise of 5G technology will further enhance connectivity, enabling real-time communication between machines and systems across vast distances.
In the future, we can expect to see more collaborative robots, or “cobots,” working alongside human operators in manufacturing plants. These cobots will be designed to assist humans with tasks that require precision and strength, allowing for safer and more efficient operations.
Additionally, AI and machine learning will continue to play a vital role in automating more complex processes. Engineers will develop more advanced algorithms that allow machines to learn from data and optimize processes in ways that were previously unimaginable.
Conclusion
Industrial automation engineering is revolutionizing manufacturing by automating processes that were once performed manually. Through the use of technologies such as robotics, PLCs, AI, and SCADA systems, automation engineers are enabling manufacturers to increase productivity, improve quality, and reduce costs. While there are challenges to implementing automation, the long-term benefits far outweigh the difficulties.
As technology continues to change, industrial automation will only become more critical to the future of manufacturing. By embracing automation, businesses can remain competitive in an increasingly fast-paced and demanding market, paving the way for more efficient, safer, and innovative production methods.
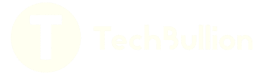