For manufacturing companies that specialize in cutting materials and high-speed machining, it is important to periodically review the production process to gauge which existing machines need maintaining, repairing or upgrading, and which new machines should be purchased.
When selecting new cutting machinery, plant managers need to carefully consider the capabilities and features of cutting machines. Generally, cutting machines should employ tools that meet some basic industry standards by exhibiting certain critical properties, these include:
- Mechanical properties; hardness at high temperatures, deformation resistance, fatigue resistance, toughness to prevent fractures
- Thermal properties; immense heat conductivity to divert high temperatures away from the cutting edge, elevated thermal shock resistance
- A stable chemical composition
- Tribological properties; resistance to wear and tear
There are several types of industrial cutting machines commonly found in manufacturing plants that are capable of various different functions to size and shape materials by removing unwanted pieces through techniques such as broaching, boring, electrical discharge machining, grinding, milling or turning. Machine tools can cut a range of materials including aluminum, brass, carbon steel, copper, cork, expanded steel, glass, paper, plastics and wood.
To get a better idea of different machine tools, their features and how they can expand production options, here are some of the machine tools used in manufacturing plants and workshops.
Electrical Discharge Machining
Also referred to as spark machining, die sinking or wire burning, electrical discharge machining (EDM) is the process of removing metal using electric sparks. One example of spark machining is the Fanuc Robocut Wire EDM which can accurately and efficiently cut and shape thick pieces of metal. Electrical discharge machines work by creating a rapidly repeating current discharge between two electrodes and are kept apart by a dielectric liquid. To create an electric arc used to remove metal, a high voltage current is needed to create an intense electric field between the two electrodes.
In addition to wire electrical discharge machines used to make two-dimensional cuts in three-dimensional pieces of metal, there are also other EDMs with different functions such as drilling holes, cavity shaping and die sinking. Manufacturers using EDM can benefit from a number of advantages including:
- Having the capability to work any material that conducts electricity
- Not worrying about the consequences of mechanical force as EDM does not come into contact with the material
- The ability to cut various shapes and depths
- Its suitability to work hardened materials
Laser Cutting Machine
Laser cutting works by focusing a powerful beam of light onto a material and cutting it with accurate precision. Powerful lasers cut material through melting and evaporation and are considered to be the most accurate machine tools. The key features that make a laser cutting machine a key piece of manufacturing equipment are:
- High accuracy cuts
- Short lead times as processes carried out on laser machines don’t require custom tooling and modification for specific projects
- Decreased maintenance costs; laser machines generally have fewer parts than other machines
- Flexibility to create specific parts in small or large batches using schematics and machine software
- Less material waste; sheet material utilization can be increased by nesting cuts together and accurately laser cutting around them
- Cutting versatility; lasers can cut through almost any material including composites, metals, plastic and wood.
Plasma Cutting Machine
Plasma cutting is the process of firing a charged gas jet at high speeds to cut through conductive metals such as aluminum, brass, copper, iron and steel. Compared to manual cutting machines and torches, plasma cutting provides manufacturers with many advantages:
- Safety improvements; the necessary gases are usually less flammable and easier to contain and control
- Increased cutting speed; mechanical plasma cutters are several times faster than traditional cutting methods
- It is more cost-effective than laser and water-jet cutting
- They can cut material of varying type and thickness
- Cooling systems prevent warping and damage to coatings
Water Jet Cutting
Water jet cutting is a method used in manufacturing to cut materials with an extremely pressurized and high-velocity jet of water. This technique is widespread and utilized to cut both soft and hard materials into almost any desired shape.
Pure water jet cutting is not able to cut through hard materials however it is a suitable application for cutting softer materials such as foam, paper, plastic, rubber and wood.
Abrasive jet cutting on the other hand is capable of cutting harder materials including aluminum, ceramics, composites, concrete, duracon, glass, granite, stainless steel and titanium. To provide the increased cutting power required to cut through hard materials, manufacturers add abrasive materials such as aluminium oxide and silica sand to the water.
CNC Machines
Computer numerical control (CNC) machining involves pre-programmed computer software being used to control the movement of tools and machinery in the manufacturing process. The versatility of CNC machines makes them particularly useful as they can control many kinds of machinery and tools, whether it be a grinder, lathe or router to carry out both two and three-dimensional cutting tasks.
CNC machining is very much cutting edge and a key piece of equipment in the production of high-end industrial-grade components and products due to its many advantages including:
- Assurance of high-quality products due to extremely accurate cutting
- Shorter lead times compared to manual cutting as CNC machines complete tasks faster and within a predictable timeframe
- Lower staffing costs as fewer operators are required
Travelling Head Presses
For manufacturers that regularly need to cut shapes and patterns out of sheets of material, a travelling head press is an essential piece of cutting equipment. Automatic travelling head presses allow operators to input the dimensions of a design into software and then simply load the sheet of material, wait for the press to cut it and then unload the waste materials and finished components. If thousands of pieces need to be made every day then it is also possible to automate the loading and unloading of material, off-cuts and finished products using conveyors belts and robotic arms.
The cutting and shaping of materials like composite, metals, plastics and stone is an important process in the production of many goods and these manufacturing processes require various high-tech and powerful cutting machines like those discussed above.
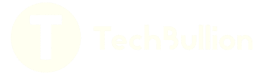