If you have a passion for creating products and want to start your own business, starting a plastic molding company can be an excellent idea. Plastic molding is the process of shaping plastic materials into various forms that are used in different industries such as automotive, electronics, packaging, and more. With the global market size for plastic molding expected to reach $162 billion by 2025, there has never been a better time to get started. In this article, we will guide you through everything you need to know about how to start your own plastic molding company from scratch!
What is plastic molding?
Plastic molding is the process of manufacturing plastic into various shapes and forms. This production technique involves melting plastic materials, then injecting or compressing it into a mold to create a specific shape. Once cooled and solidified, the plastic can be removed from the mold.
There are several different types of plastic molding techniques used in industry today, each with its unique advantages and disadvantages. Some common methods include injection molding, blow molding, rotational molding, and thermoforming.
Injection Moulding is one of the most popular techniques used for producing high volume orders quickly and efficiently. Blow Moulding is ideal for creating hollow objects like bottles or containers while Rotational Moulding works well when creating large parts such as car bumpers. Thermoforming uses heat to soften sheets of thermoplastic material so they can be formed over a mold.
Plastic Moulding encompasses an array of processes that transform raw plastic material into products we use daily- whether it’s automotive parts or food packaging!
The global market size for plastic molding
The global market size for plastic molding is vast and continually expanding. In 2020, the global plastic molding market was valued at $339.3 billion and is projected to reach $529.1 billion by 2027.
The Asia-Pacific region dominates the plastic molding industry, accounting for over 40% of the total revenue share in 2020. This growth can be attributed to rapid industrialization, urbanization, increasing population, and favorable government policies promoting manufacturing activities.
Furthermore, the packaging segment holds a significant share in the plastic molding market due to its extensive use in food and beverage industries. Additionally, automotive applications are expected to grow significantly with advancements in technology leading to lighter-weight components being produced through plastic injection molding.
The increase in demand for sustainable products has led to a surge in biodegradable plastics production using methods such as extrusion blow molding and rotational molding techniques. Moreover, medical equipment manufacturing is also driving growth due to an aging population requiring more healthcare services.
With increasing awareness towards eco-friendly products coupled with technological advancements leading to innovative product development across different sectors; it’s safe to say that there will be continued growth for years ahead within the global plastic molding market.
The different types of plastic molding
Plastic molding is an essential process in manufacturing plastic products, and there are several different types of plastic molding. Each type has its unique advantages and disadvantages, making it suitable for specific applications.
Injection molding is the most common type of plastic molding used to produce high volumes of identical parts quickly. This method involves injecting melted plastic into a mold cavity with high pressure and temperature, which then cools to form the desired shape.
Blow molding is another popular technique that uses compressed air to inflate molten plastic into a hollow tube-shaped mold. Once cooled, this results in a wide variety of products such as bottles, containers, and other similar items.
Rotational molding involves heating a hollow mold that rotates around two perpendicular axes while melted resin is added gradually. This creates an even coating inside the mold resulting in strong yet lightweight products.
Thermoforming utilizes heat to soften thermoplastic sheets before vacuum or pressure forming them over molds. It’s widely used for packaging materials like blisters or clamshells but also for creating larger products with low volume production runs.
Each technique has its benefits when it comes down to producing quality components efficiently without sacrificing any structural integrity or precision requirements needed by customers.
The equipment you will need to start a plastic molding company
To start a plastic molding company, you need to have the right equipment. Here are some of the essential tools and machines that you will require:
- Injection molding machine
This is one of the most important pieces of equipment in plastic molding. It uses heat and pressure to melt and inject molten plastic material into a mold cavity.
- Mold tool
Mold tools come in various shapes and sizes depending on what product you intend to manufacture. They are used to shape the melted plastic material into your desired product.
- Granulator
A granulator breaks down large chunks or sheets of plastic into smaller pellets for injection molding machines.
- Cooling system
To prevent warping, cracking, or shrinking of your molded products, it’s crucial to have an efficient cooling system that can regulate temperature during production.
- Quality control equipment
After manufacturing your products, it’s important to ensure they meet specified standards by checking them with quality control instruments like calipers or micrometers.
Getting all these items might be expensive but worth investing if starting a profitable business is what really matters.
The cost varies depending on where you are located so do proper research before purchasing any machinery or tools required for starting up this business venture!
How to start a plastic molding company
Starting a plastic molding company can be an exciting and challenging venture. Here are some steps to help you get started.
Firstly, research your market and identify the types of plastic products in high demand. This will help you decide which type of plastic molding process to specialize in.
Next, create a business plan that outlines your goals, target market, financial projections, and marketing strategy. This will give you a clear roadmap for success.
Once you have your business plan in place, secure funding through investors or loans to purchase the necessary equipment such as injection molding machines, molds, and auxiliary equipment like chillers or robots.
After acquiring the right machinery and tools for your production line-up it is important to hire skilled staff who understand plastics engineering technologies including design specifications & quality control processes.
Finally, promote your plastic molding company online using SEO keywords relevant to the industry such as “plastic manufacturer” or “molding services”. Participate on social media platforms where individuals interested in this field may congregate so that they know about your brand!
Conclusion
Starting a plastic molding company can be an exciting and lucrative venture. It requires a lot of planning, research, and hard work to get started, but with the right equipment, knowledge, and resources in place, you can build a successful business that meets the needs of your customers.
Remember that while there are many different types of plastic molding processes available today, each has its own unique benefits and challenges. The key is to choose the method that best suits your needs based on factors such as production volume, part complexity, material selection etc.
As with any business endeavor, it’s important to do your due diligence upfront so you have a clear understanding of what it takes to succeed in this industry. This includes conducting market research to identify potential competitors and customer demands; setting up manufacturing facilities equipped with advanced technology like 3D printing capabilities; securing financing for raw materials procurement or hiring skilled employees as needed; developing marketing strategies tailored specifically for different target audiences etc.
In conclusion then: if you’re ready for an exciting challenge in the world of plastics manufacturing – one that offers plenty of growth opportunities over time- then starting a plastic molding company could be just what you need! Keep these tips in mind as you move forward towards success!
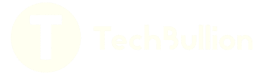