Topstar’s injection molding machines have long been recognized for their superior performance and reliability in various manufacturing environments, and their deployment in Spain is no exception. In a country where power fluctuations are not uncommon, especially in some industrial regions, Topstar has been at the forefront of engineering solutions that ensure continuous production without compromising quality. This article details how Topstar’s injection molding machines overcome these power challenges through innovative design, intelligent control, and robust engineering. We’ll explore the journey of these machines from their initial concept to their advanced operating features while maintaining optimal performance even when power is unstable.
Injection Molding Machines: Engineering for Power Fluctuations
Engineering is at the heart of Topstar’s injection molding machines and focuses on resilience and adaptability in power fluctuations. The design process began with a thorough analysis of the characteristics of the Spanish power grid and the specific challenges facing manufacturers. Engineers identified that sudden voltage drops, spikes, and frequency variations were common issues that could interrupt production. To address these issues, the Topstar team integrated a multi-layered power management system that includes voltage regulators, surge suppressors, and adaptive frequency converters. These components create a stable operating environment, ensuring the injection molding machines maintain their precision and output quality regardless of external power conditions.
A key innovation in the design is the inclusion of a redundant power supply module. With a dual power supply system, the machine can instantly switch to an alternate power path when detecting an anomaly. This redundancy protects the delicate internal circuitry and prevents unexpected downtime that could lead to material waste or production delays.
Injection Molding Machine: Smart Technology and Control System Integration
Modern manufacturing requires innovative solutions beyond mechanical robustness, and Topstar’s injection molding machine is a testament to this evolution. The machine incorporates innovative technology and an advanced control system as the digital backbone of its operation. The machine continuously monitors its internal processes and external power conditions by integrating state-of-the-art sensors and a centralized control unit. This real-time data acquisition enables the system to make instant adjustments, ensuring that the molding process remains uninterrupted and meets strict quality parameters even during power fluctuations.
The digital control unit is at the heart of this intelligent system, programmed with algorithms designed to predict and respond to power anomalies. These algorithms analyze data from multiple sensors that track voltage levels, current, and temperature, among other critical parameters. When the system detects a deviation from the expected power input, it activates a predetermined safety protocol, and this rapid response prevents production errors.
Performance in Spain’s Power Environment
The performance of the Topstar injection molding machine in Spain’s fluctuating power environment is a great testament to its design and integration of innovative technologies. In areas with unpredictable power supply, the machine has proven to maintain consistent production quality without interruption. This is mainly due to the robust power management system and real-time adjustments embedded in its control architecture. Manufacturers report that the machine seamlessly operates even during peak hours when voltage is unstable, ensuring they meet production deadlines and maintain product standards.
Field data from multiple Topstar customers in Spain demonstrate the machine’s resiliency. In one instance, a production plant reported that during a sudden power outage, the injection molding machine automatically switched to backup power mode, maintaining the precise temperature and pressure required to mold high-quality parts. This automatic response prevents potential production delays and protects the machine from pressure-related damage.
Equipment Sharing and Collaborative Advantages
One of Topstar injection molding machines’ standout features is their important role in facilitating equipment sharing and collaborative use among Spanish manufacturers. In today’s competitive market, sharing high-cost, high-performance equipment can lead to significant cost savings and operational efficiencies. In addition, equipment sharing enables multiple manufacturers to use the latest injection molding technology, thereby reducing the capital expenditure required to purchase and maintain individual machines. This collaborative approach is particularly popular in Spain, where economic pressures and the need for high-quality production often require innovative financial solutions. Topstar’s shared equipment model provides cost-effective, advanced technology and fosters an environment for knowledge-sharing and collaborative problem-solving. Manufacturers can exchange best practices and technical insights and coordinate maintenance schedules to ensure that shared injection molding machines provide optimal performance for all parties involved.
Adaptability and operational flexibility on the Spanish power grid
Adaptability is a key factor in the enduring success of Topstar’s injection molding machines in the competitive Spanish manufacturing market. The injection molding process is susceptible to power stability, and Spain’s dynamic power grid requires equipment that can flexibly adapt to different conditions. Topstar designs its machines with multiple layers of adaptive technology to ensure operational flexibility even when the electrical environment is less than ideal. By anticipating and responding to power fluctuations, the machine can maintain consistent quality, enabling manufacturers to reliably produce high-precision components. At the same time, the machine’s integrated energy management system defines one of its key adaptability characteristics. Designed to transition between different power modes seamlessly, the system ensures that the injection molding machine can operate efficiently during peak and off-peak hours.
Ultimately
Topstar’s injection molding machines are expected to set a higher standard in resilient manufacturing technology. Continued developments in intelligent systems, energy management, and adaptive design are expected to improve further the machines’ performance in regions such as Spain, where power fluctuations remain a significant challenge. With continued investment in R&D, Topstar is committed to perfecting the integration of advanced control systems and innovative engineering solutions that will mitigate the risks associated with unstable power and improve operational efficiency and quality.
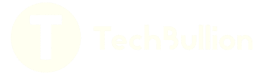