Advances in the Industrial Internet of Things (IIoT), artificial intelligence (AI), machine learning, and advanced analytics are turbocharging the move to Industry 4.0. To stay competitive, companies are using AI-powered IoT tools to alert manufacturers to failures in equipment, set maintenance reminders, improve quality control measures and automate processes.
Machine learning for Processes Optimization
Machine learning algorithms can be applied to historical data about consumed energy in the past, to detect patterns and trends. Then, future energy consumption can be predicted.
For instance, if your production facility is turning out high-quality products, but you are still incurring high production costs, data may reveal that your facility is using too much energy. Data scientists can choose to run autoregressive models that reveal cyclic patterns of energy use. Deep neural networks can define and detect patterns, and forecast energy use quickly so that you are able to manage your output as needed.
Improving data quality ensures that the information that is received by your AI-powered IoT sensors is accurate, customized, and relevant to your concerns and tools.
Machine Learning for Predictive Maintenance
Manufacturing centers with large workloads or long production hours can take advantage of machine learning for predictive maintenance. In many instances, machine learning models can be used to limit shut-down completely, or at least mitigate any loss of manufacturing time.
As mentioned earlier, data quality is imperative when designing machine learning models. But, choosing the best model for the outcomes you desire is an important step as well. Several machine learning models are used to address frequent issues within the manufacturing sector.
An anomaly detection method compares normal system behavior against failure events. When a piece of equipment veers from the norm, the model can flag a device. Supervisors and maintenance staff can then investigate the issue and correct it on-the-spot, if necessary.
Regression models can predict the Remaining Useful Life (RUL) of a piece of equipment. They compare usage history and static data to determine how long the piece of equipment can continue output before failing. This allows manufacturers to know how long and how hard they can push equipment to meet an order, before scheduling down-time for maintenance.
Classification models can predict a failure within a selected period of time. The failure can range from a significant shortfall, to a routine issue. A maintenance team can evaluate when, and how to schedule maintenance.
Computer Vision for Quality Control
While AI can improve the manufacturing process, it is also capable of assisting with product quality control. Using computer imaging techniques and clean image data, an AI-powered algorithm can efficiently check for quality.
AI visual inspection is a cost-effective way for manufacturers to monitor product quality in real-time. Using computer vision for quality control is especially helpful for manufacturers in highly regulated industries. For instance, Audi and other auto manufacturers have used AI to assist in quality control checks.
A camera-based computer vision system scans parts using high-resolution images and GPU technology. Thanks to real-time video processing, AI quality control checks can alert supervisors to sudden drops in quality mid-production.
Each part’s scan is compared against historic images of perfect parts. This is accomplished by employing deep learning neural network integration. This technology offers greater accuracy than other computer screening options, because it is built using instance segmentation algorithms. Because the system is constantly collecting images of surface defects, the quality control system is continuously improving. Parts that do not match the historical criteria are flagged by the AI program and removed from the sorting area.
Edge AI: The Future of Manufacturing
IoT use cases show that manufacturers can employ edge AI to enhance the industrial Internet of Things processes.
Edge AI technology does not rely on the cloud, or bandwidth to communicate information. Placing this technology in a manufacturing setting can reduce cross-communication problems when too many devices are connected to the same network and mitigate bandwidth limitations. Eventually, this makes it possible to speed up the production cycle and increases throughput.
We are witnessing numerous cases where emerging technologies are creating a smarter ecosystem. Using edge AI and data analytics, a Japanese industrial electronics company, Daihen Corporation, eliminated 5,000 hours of manual data entry per year for electric transformers production.
Manufacturing systems today perform at no more than 90 percent efficiency, but they can’t get the last 10 percent because machines break. The core idea of edge AI is to never let the production system stop. As more manufacturers invest in smart systems, this investment will make a tremendous difference in the world’s economic efficiency.
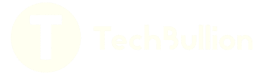