Honing hydraulic cylinder tubes is a critical process that significantly contributes to the performance and reliability of hydraulic systems. These tubes serve as essential components, providing housing for pistons and facilitating the conversion of hydraulic energy into mechanical force. The honing process involves precision machining techniques that improve surface finish, dimensional accuracy, and cylinder tube integrity. This article explores the significance of honing hydraulic cylinder tubes, highlighting how it enhances performance, reliability, and longevity in hydraulic systems.
Understanding Hydraulic Cylinder Tubes
Hydraulic cylinder tubes are integral to the functioning of hydraulic systems. They provide a sealed chamber for pistons to move within, converting hydraulic energy into linear motion. These tubes are typically made of materials like steel or stainless steel, chosen for their durability and resistance to the high pressures and forces involved in hydraulic operations. The surface finish and dimensional accuracy of hydraulic cylinder tubes are crucial for efficient and reliable system performance.
The Importance of Honing Hydraulic Cylinder Tubes
Honing is a machining process that involves the removal of material from the internal surface of hydraulic cylinder tubes. It is performed using honing stones that have abrasive particles embedded in them. Honing serves several important purposes:
Surface Finish Enhancement: Honing removes any imperfections, such as roughness, irregularities, or machining marks, from the inner surface of the cylinder tube. This results in a smoother finish that reduces friction and wear, improving overall system efficiency.
Dimensional Accuracy: Honing ensures precise internal diameter (ID) dimensions of the cylinder tube. This accuracy is crucial for proper piston fitment and seal integrity, preventing leakage and maintaining optimal system performance.
Cylinder Tube Integrity: The honing process removes any surface irregularities or stress concentrations that may have occurred during the tube manufacturing or handling process. This enhances the structural integrity of the cylinder tube, reducing the risk of failure or fatigue under high-pressure conditions.
Honing Process and Techniques
The honing process involves passing a set of honing stones through the cylinder tube while rotating and reciprocating them. The stones gradually remove material, creating a precise and smooth internal surface. The process parameters, such as stone grit, feed rate, and rotational speed, are carefully controlled to achieve the desired surface finish and dimensional accuracy. Advanced honing machines and automation systems are often used to ensure consistency and precision.
In addition to conventional honing, specialized techniques like diamond honing and plateau honing are employed for specific applications. Diamond honing utilizes diamond-impregnated honing stones for superior precision and surface quality. Plateau honing involves a multi-step process that creates a plateau-like surface texture, optimizing oil retention and promoting proper lubrication in the cylinder tube.
Benefits of Honing Hydraulic Cylinder Tubes
The honing process offers several benefits that enhance the performance and reliability of hydraulic systems:
Improved Sealing: Honing ensures a precise and smooth internal surface, enabling proper piston fitment and seal integrity. This minimizes leakage and improves the efficiency and responsiveness of hydraulic systems.
Reduced Friction and Wear: The honed surface finish reduces friction between the piston and cylinder tube, extending component life and minimizing wear. This results in enhanced system reliability and reduced maintenance requirements.
Optimal Fluid Flow: Honing eliminates surface irregularities and promotes uniform fluid flow within the cylinder tube, optimizing system performance and responsiveness.
Enhanced Corrosion Resistance: The honing process can create a micro-textured surface that improves the adhesion of protective coatings, enhancing the corrosion resistance of the cylinder tube.
Advanced Honing Technologies
In addition to conventional honing techniques, advancements in technology have led to the development of specialized honing processes. For instance, computer-controlled honing machines offer precise control over process parameters, resulting in consistent and repeatable results. Additionally, honing with coolant or specialized abrasives can improve cutting efficiency and surface finish. Laser-assisted honing is another innovative technique that utilizes laser beams to heat and soften the cylinder tube surface, enhancing the honing process and achieving superior surface quality.
Quality Control and Inspection
To ensure the effectiveness of the honing process, quality control and inspection play a vital role. Metrology tools, such as coordinate measuring machines (CMMs) and optical measurement systems, are used to verify dimensional accuracy and surface finish. Additionally, non-destructive testing techniques, such as ultrasonic or eddy current testing, can be employed to detect any internal defects or irregularities in the cylinder tube. Implementing rigorous quality control measures helps maintain the desired standards and ensures the reliability and performance of honed hydraulic cylinder tubes.
Conclusion
Honing hydraulic cylinder tubes is a crucial process that enhances the performance, reliability, and longevity of hydraulic systems. By improving surface finish, dimensional accuracy, and cylinder tube integrity, honing ensures efficient fluid flow, reduced friction, and optimal sealing, contributing to the seamless operation of hydraulic systems.
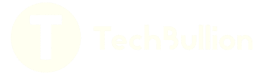