Flexographic printing, commonly known as flexo printing, is a versatile and widely used printing method in the packaging industry. As the demand for flexible packaging continues to grow, so does the need for high-quality flexo printing plates. Finding a flexo printing plate manufacturer that can meet this standard is always a big challenge for most investors in this industry. In fact, with the growing number of manufacturers, quality standards are becoming a big issue.
However, with big brands in the industry like laser engraving manufacturers, investors have an opportunity to get not only quality flexo plate makers but also custom-made machines. In this guide, we are going to look at key things surrounding flexo printing plate manufacturers. We will look at the industry trends and innovations and show you what to look for when selecting these manufacturers.
Innovations Shaping the Industry
Innovation is the cornerstone of progress in the flexo printing plate manufacturing industry, driving advancements that enhance print quality, efficiency, and sustainability. Let’s delve deeper into some of the groundbreaking innovations shaping the future of flexographic printing:
Laser Engraving Technology:
Laser engraving technology has revolutionized the process of plate imaging, allowing for precise and intricate designs. Unlike traditional methods that rely on mechanical or chemical etching, laser engraving offers unparalleled control over dot structure and depth. By harnessing the power of lasers, manufacturers can achieve microscopically precise plate engravings, resulting in sharper images, finer details, and smoother gradients. Laser-engraved plates also exhibit superior durability, withstanding the rigors of high-speed printing without compromising on quality or consistency.
Flat-Top Dot Technology:
Flat-top dot (FTD) technology has emerged as a game-changer in flexo printing, revolutionizing the way dots are formed on printing plates. Unlike conventional dot shapes, which feature a rounded “shoulder,” FTD technology produces dots with a flat, uniform surface. This innovative approach eliminates the need for time-consuming and labor-intensive plate processing techniques, such as surface screening or bump curves. By producing flat-top dots, manufacturers can achieve more precise ink transfer, resulting in vibrant colors, smoother gradients, and finer details.
Multi-Layer Plate Technology:
Multi-layer plate technology represents a significant leap forward in flexographic printing, allowing for the creation of complex designs with unparalleled precision and versatility. By stacking multiple layers of photopolymer material, manufacturers can achieve precise control over ink laydown, enabling the reproduction of intricate artwork, fine text, and special effects. Each layer can be tailored to accommodate different ink densities, textures, and surface finishes, providing designers with unprecedented creative freedom. Multi-layer plates are particularly well-suited for applications that require precise registration, such as package printing, labels, and security printing.
Hybrid Plate Solutions:
Hybrid plate solutions represent the convergence of digital and analogue technologies, offering the best of both worlds in terms of speed, quality, and flexibility. By integrating digital imaging with conventional plate making techniques, manufacturers can optimize workflow efficiency and print quality while reducing costs and turnaround times. Hybrid plates combine the precision and consistency of digital imaging with the durability and performance of traditional flexo plates, making them ideal for a wide range of printing applications.
Industry Trends
The flexo printing plate manufacturing industry is constantly evolving to meet the changing demands of the packaging market. Let’s delve into the latest trends shaping this dynamic sector:
Sustainability Focus:
One of the prominent trends in the flexo printing plate manufacturing industry is the increasing emphasis on sustainability. Manufacturers are investing in eco-friendly materials and processes to reduce environmental impact. Water-based and solvent-free plate making solutions are gaining traction as businesses strive to minimize their carbon footprint.
Digitalization:
Digital technologies are revolutionizing the flexo printing plate manufacturing process. Advancements in computer-to-plate (CTP) systems and digital imaging have led to greater precision, faster turnaround times, and improved print quality. Digitalization also enables customization and personalization, catering to the evolving demands of brands and consumers.
Automation and Robotics:
Automation is streamlining production processes in the flexo printing plate manufacturing industry. From plate imaging and processing to inspection and quality control, robotic systems are enhancing efficiency and consistency while reducing labor costs. Automation also ensures greater accuracy, minimizing errors and waste.
Enhanced Plate Durability:
Manufacturers are continually innovating to improve the durability and longevity of flexo printing plates. Advanced materials and coatings are being developed to withstand the rigors of high-speed printing and prolonged use. Enhanced durability not only increases productivity but also reduces the frequency of plate replacements, leading to cost savings for printers.
Sustainable Plate Disposal:
With sustainability becoming a priority, manufacturers are focusing on developing recycling and disposal solutions for flexo printing plates. Biodegradable materials and recycling programs are being implemented to minimize environmental impact and promote circular economy practices. By offering sustainable end-of-life solutions, manufacturers are aligning with the sustainability goals of their customers.
Flexo Printing Plate Manufacturer Selection Hacks:
Assess Manufacturer’s Expertise:
When selecting a flexo printing plate manufacturer, assess their expertise and experience in the industry. Look for manufacturers with a proven track record of delivering high-quality plates and innovative solutions. Consider their knowledge of industry trends and their ability to adapt to changing market demands.
Evaluate Plate Quality:
Quality is paramount when choosing a flexo printing plate manufacturer. Evaluate the durability, consistency, and print performance of their plates through samples and customer testimonials. Look for manufacturers that use advanced materials and technologies to ensure superior results across a range of printing applications.
Consider Sustainability Practices:
In today’s environmentally conscious market, sustainability is a key consideration. Choose a manufacturer that prioritizes sustainable practices throughout the production process, from materials sourcing to waste management. Look for certifications and initiatives that demonstrate their commitment to reducing environmental impact.
Review Technical Support:
Technical support is essential for the seamless integration of flexo printing plates into your workflow. Choose a manufacturer that offers comprehensive technical assistance, including plate optimization, troubleshooting, and training. Look for responsive customer service and prompt assistance to address any issues or concerns that may arise.
Cost and ROI Analysis:
While cost is a factor, consider the overall return on investment (ROI) when selecting a flexo printing plate manufacturer. Evaluate the total cost of ownership, including plate longevity, print quality, and production efficiency. Choose a manufacturer that offers competitive pricing without compromising on quality or service.
Conclusion:
The flexo printing plate manufacturing industry is undergoing rapid evolution, driven by technological advancements and shifting market dynamics. By staying abreast of industry trends, embracing innovative technologies, and following selection hacks, businesses can make informed decisions when choosing a flexo printing plate manufacturer. Whether prioritizing sustainability, print quality, or cost-effectiveness, selecting the right manufacturer is essential for achieving success in today’s competitive packaging market.
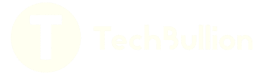