In today’s time, we aim for compact functions in one electronic device. This means that the device gets the most of the work done while occupying the least amount of space. This pursuit is what fuels the ongoing advancements in the design and production of printed circuit boards (PCBs). Amidst this backdrop, there are two standout types of PCBs that have played a pivotal role in meeting these demands: High-Density Interconnector PCBs (HDI PCBs) and Aluminum PCBs. These particular PCB variations come with their own set of advantages, making them indispensable components in the ongoing transformation of contemporary electronics.
HDI PCBs
HDI PCBs, or High-Density Interconnector PCBs, represent a significant leap forward in the realm of circuit board technology. They are designed to achieve a higher wiring density per unit area compared to conventional PCBs without blind or buried vias. Essentially, this translates into the ability to accommodate more components and connections within a smaller circuit board area, facilitating the development of more compact and complex electronic devices.
The primary strength of HDI PCBs lies in their capacity to host intricate and miniature designs. As the trend in technology continues towards smaller form factors, HDI PCBs have become indispensable in the creation of devices like smartphones, tablets, wearables, and other portable gadgets. The reduced size of these PCBs also results in shorter signal pathways, leading to enhanced signal quality and reduced electromagnetic interference (EMI).
A noteworthy feature of HDI PCBs is the use of microvias and blind vias. Microvias are minute openings drilled into the PCB, connecting different layers of the board and enabling signal routing in confined spaces, thus increasing routing density. Blind vias, conversely, link an outer layer of the PCB to one or more inner layers, eliminating the need to traverse the entire board. This technology significantly enhances routing flexibility and reduces the number of signal layers required, consequently reducing overall PCB thickness.
Advantages of HDI PCBs
- Compact Design: HDI PCBs enable the creation of smaller and more compact electronic devices, catering to the modern consumer market’s demands.
- Improved Signal Integrity: Shorter signal paths and diminished electromagnetic interference result in superior signal quality and reliability.
- Enhanced Flexibility: Microvias and blind vias offer greater flexibility in routing, allowing for intricate and high-density designs.
- Cost Efficiency: While initial production costs may be higher, the compact design and reduced layer count often lead to cost savings in the long run.
Aluminum PCBs: A Solution for Heat Dissipation
Wondering what Aluminum PCBs are? Well, here’s all you need to know about them! It’s a type of PCBs that features a layer of thermally conductive dielectric material sandwiched between an aluminum layer at the bottom and a copper foil layer at the top.
The primary advantage of Aluminum PCBs is their excellent heat dissipation capabilities.
Electronic components, particularly those that consume significant power in working, generate heat during operation. Without effective heat dissipation, this heat can be dispatched mostly to avoid potential damage to the components. Aluminum, being a proficient heat conductor, efficiently transfers heat away from the components, preventing overheating and ensuring stable operation.
Due to their thermal properties, aluminium PBCs are used in some different areas where heat control is important. They find applications such as power supplies for LED lighting, high power applications like motor controllers and automotive electronics as well as others. For example, Aluminum PCBs are used in EV powertrains to control heating from high-current electronic devices in the automotive industry.
Advantages of Aluminum PCBs
In order to maintain ideal temperatures for its electronic components and increase its lifespan, it is suggested that you use aluminium PCBs. The made-to-order PCBs have sufficient properties to dissipate heat so that no overheating problem occurs. In addition to this critical function, aluminum PCBs offer a host of other advantages:
- Heat Resistance: Such components withstand very high temperatures and do not succumb to alteration of operations.
- Thermal Shock Resilience: They are used in situations involving quick variations of climate temperatures.
- Lightweight Design: They are appropriate for situations in which cutting down on weight is essential because of their minimal weight.
- Enhanced LED Performance: LED lighting systems benefit much from aluminium PCBs increasing their brightness as well as durability.
The best choice for high-quality thermal conductivity and reliability should be aluminum PCBs. They are commonly used across various industries such as automotive, aerospace, medical, and consumer electronics.
Selecting the Appropriate PCB for Your Application
Finally, PCB type selection depends highly upon the requirements of the device or application. For example, we need to use an HDI circuit board if we need a complicated main control device, and we need to use an aluminium PCB if we need a power PCB which will run high currency. Besides, please note that there are various other considerations which must be made when comparing HDI PCBs with Aluminum PCBs, sometimes a mixture of the two types can be used in the same device for maximum function and efficiency.
HDI PCBs are the best option in cases where the miniaturization of devices and their high-density design is necessary. This is exemplified by how HDI PCBs allow phones to integrate many components into their slender designs without compromising on efficiency.
In contrast, aluminium printed circuit boards are very efficient for creating electronic systems which can provide considerable amounts of heat, like power electronics and LED lighting. Such boards make sure that temperature-sensitive parts run at the recommended temperature range for maximum performance and long life.
Innovation and Integration
This will lead to electronics being more advanced, smaller and cheaper. For instance, in the case of electric cars, the use of aluminium PCBs in power trains is helpful in improving the reliability and efficiency of electric vehicles.
Such PCBs are essential for EVs’ optimum operation by maximizing vehicle mileage capacity. In addition, combining HDI PCBs and Aluminium PCBs ushers in a new dawn of possibilities towards innovation. For instance, when integrated into fields such as medical technology the ultra wide circuit boards may be utilized to develop small and effective portable diagnostic machines with increased function and reliability.
Challenges and Future Trends
Although HDI PCBs and Aluminum PCBs come with their fair share of benefits, they also come with some distinct challenges. HDI PCBs, in particular, can be quite intricate and expensive to produce, primarily because of the complex production process of micro vias and blind/buried vias. Ensuring the reliability and robustness of these PCBs is critical, especially in mission-critical applications.
On the other hand, Aluminum PCBs may have limitations in complex applications which need two or more copper layers, as the production process and limitations make it is difficult to produce multilayer aluminium printed circuit boards.
Industries are constantly striving to tackle these challenges through creative design choices and the selection of materials. Looking forward, the future of PCB technology holds great promise. Progress in materials, manufacturing techniques, more advanced equipment and design methods is expected to lead to even more compact and complex electronic devices. Combining HDI PCBs and Aluminum PCBs with emerging technologies like industry, automotive, telecommunications, renewable energy, 5G and the Internet of Things (IoT) will unlock fresh opportunities for more advanced devices.
As a parting thought, HDI PCBs and Aluminum PCBs stand as two distinct yet equally essential advancements in circuit board technology. HDI PCBs enable the development of smaller, high-density electronic devices with enhanced signal integrity, whereas Aluminum PCBs excel in managing heat, guaranteeing the reliability and durability of electronic components. As technology continues to advance, the integration of these PCB types will have a pivotal role in shaping the future of electronics, fostering innovation across a wide array of industries.
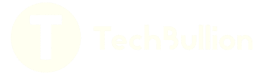