In a world where businesses are constantly striving for greatness, creating a culture of excellence is crucial for long-term success. One powerful tool that has been proven to drive significant improvements in organizations is Lean Six Sigma. Join us as we explore the impact of Lean Six Sigma on businesses and how it can help cultivate a culture of excellence within your organization. From reducing waste to enhancing processes, get ready to discover how implementing Lean Six Sigma can transform your business into a top-performing powerhouse.
Introduction to Lean Six Sigma
Lean Six Sigma is a business methodology that combines two powerful problem-solving and process improvement approaches – Lean Management and Six Sigma. It focuses on eliminating waste, reducing variability, and improving overall efficiency in an organization’s processes.
The concept of Lean Manufacturing was first pioneered by Toyota in the 1950s, with the goal of reducing manufacturing defects and increasing customer value through continuous improvement. On the other hand, Six Sigma was developed by Motorola in the 1980s to improve quality management processes by identifying and eliminating errors and defects.
When these two methodologies are combined, they offer a robust framework for driving sustainable development within any organization. This approach provides businesses with the tools to identify areas of inefficiency or waste and implement changes that lead to improved performance, customer satisfaction, cost savings, and profitability.
The Importance of a Culture of Excellence in Business
In today’s competitive business landscape, companies are constantly striving for success and growth. However, many organizations struggle to achieve their goals due to a lack of focus on excellence in their culture. A culture of excellence is essential for businesses to thrive in the long run.
What is a Culture of Excellence?
A culture of excellence refers to an organization’s shared values, norms, beliefs, and practices that promote high performance and continuous improvement. It is an environment where every employee strives for perfection and pursues the highest standards in their work. This type of culture encourages continuous learning, innovation, and collaboration among team members.
Role of Lean Six Sigma in Creating a Culture of Excellence
Lean Six Sigma methodology plays a crucial role in creating a culture of excellence within an organization. Its principles focus on eliminating waste, improving efficiency and reducing defects through data-driven decision-making processes. When implemented effectively, it can transform an organization’s culture by promoting a mindset that emphasizes constant improvement.
1. Instilling Quality as the Top Priority
One essential aspect of Lean Six Sigma is its emphasis on quality as the ultimate goal. By making quality a top priority throughout all levels of the organization, employees are motivated to consistently produce excellent work that meets or exceeds customer expectations.
2. Encouraging Continuous Improvement
Another crucial element is over-arching commitment to continuous improvement driven by lean principles which considers each process as having room for growth instead being considered static.. A key principle behind this approach is kaizen – the belief that small changes lead to significant improvements over time,
3. Fostering Collaboration and Teamwork
Lean Six Sigma also promotes collaboration among team members across various departments or functions within an organization. This collaborative mindset encourages employees to share knowledge and expertise, leading to more effective problem-solving capabilities.
4. Embracing Data-Driven Decision Making
Making decisions based on data rather than intuition or personal bias is a fundamental aspect of Lean Six Sigma methodology. This promotes a culture of continuous learning and improvement, as decisions are based on facts rather than assumptions or opinions.
How Lean Six Sigma Can Help Improve Businesses
Lean Six Sigma is a powerful methodology that has been adopted by countless businesses to improve their operations and gain a competitive edge in the market. It combines the principles of Lean manufacturing, which focuses on minimizing waste and maximizing efficiency, with Six Sigma’s data-driven approach to quality management. This combination provides businesses with a comprehensive framework for identifying and eliminating process inefficiencies, reducing costs, and improving overall performance.
One of the key ways that Lean Six Sigma can help improve businesses is by promoting a culture of continuous improvement. The methodology emphasizes the importance of constantly evaluating and refining processes to eliminate errors, defects, and waste. This approach encourages employees at all levels to actively seek out opportunities for improvement and empowers them to take ownership of their work. As a result, organizations that embrace Lean Six Sigma often see an increase in employee engagement, motivation, and productivity.
In addition to boosting employee morale, Lean Six Sigma helps businesses achieve tangible results through its focus on data analysis. By using statistical tools such as control charts and process capability analysis, problems can be identified early on, leading to faster resolutions. This not only reduces costs but also prevents potential customer complaints or dissatisfaction.
Another benefit of implementing Lean Six Sigma is its emphasis on meeting customer needs. The methodology recognizes that without satisfied customers, a business cannot succeed in the long run. Through tools like voice of the customer (VOC) analysis and quality function deployment (QFD), organizations can better understand customer requirements and align their processes accordingly. By consistently delivering products or services that meet or exceed expectations, businesses can build trust with customers and establish themselves as industry leaders.
Real Life Examples of Successful Implementation of Lean Six Sigma
There are numerous companies and organizations around the world that have successfully implemented Lean Six Sigma principles to improve their businesses and achieve significant results. In this section, we will explore some real-life examples of how Lean Six Sigma has been used in different industries to drive improvements and create a culture of excellence.
1. General Electric (GE)
One of the earliest adopters of Lean Six Sigma, GE’s CEO Jack Welch famously said, “From now on, your job is not just to do your work; it’s to spot problems and solve them.” This mindset shift towards continuous improvement has allowed GE to save billions of dollars through waste reduction and process optimization. For instance, their aviation division implemented Lean Six Sigma methodologies, resulting in a 44% decrease in aircraft engine backlogs and an increase in profit margins by 5%.
2. Toyota Motor Corporation
Toyota is widely credited as the pioneer of Lean manufacturing principles that later evolved into Lean Six Sigma. The company’s production system focuses on minimizing waste while improving efficiency and quality. Toyota has achieved outstanding results with this approach, including reducing defects by 93%, increasing productivity by 34%, and cutting down lead times from months to days.
3. Amazon
The e-commerce giant has utilized Lean techniques throughout its operations to streamline processes, increase efficiency, reduce costs, and ultimately deliver exceptional customer experiences. One example is their “two-pizza rule,” where every internal team must be small enough to be fed with two pizzas – limiting bureaucracy for faster decision making.
4. Caterpillar Inc.
The heavy equipment manufacturer credits its success in product development largely due to integrating Lean Six Sigma methodologies across its entire organization. Using tools such as value stream mapping and kaizen events have resulted in significant cost savings while continuously improving product quality.
5. Memorial Hospital
Healthcare organizations have also embraced Lean Six Sigma principles with remarkable results. Memorial Hospital reduced wait times for patients by implementing a patient-focused process using Lean Six Sigma methodologies. This resulted in a 30% increase in patient satisfaction scores and an overall improvement in the quality of care delivered.
6. Starbucks
The global coffee giant has applied Lean Six Sigma to its supply chain management, resulting in significant cost savings and improved customer satisfaction. By implementing kaizen events, Starbucks was able to identify areas for improvement and implement changes that have led to efficiencies throughout their supply chain.
Measuring the Success and Impact of Lean Six Sigma in Businesses
Measuring the success and impact of Lean Six Sigma in businesses is a crucial step towards understanding its effectiveness and continuously improving processes. In this section, we’ll explore some key metrics that can be used to evaluate the success of implementing Lean Six Sigma.
Firstly, one of the most commonly used metrics for measuring the success of Lean Six Sigma is its impact on cost reduction. Since one of the main goals of this methodology is to eliminate waste and improve efficiency, it’s essential to track how much money has been saved through process improvements. This could include reduced material costs, improved cycle time, or decreased rework. It’s also important to compare these savings with investments made in implementing Lean Six Sigma, such as training costs or hiring consultants.
Another critical factor in evaluating the success of Lean Six Sigma is customer satisfaction. This can be measured through surveys or feedback from customers who have experienced changes implemented through Lean Six Sigma projects. By using customer-centric metrics like Net Promoter Score (NPS) or Customer Satisfaction Score (CSAT), businesses can get an overall understanding of how well their processes are meeting customers’ needs and expectations.
Quality control is also a significant aspect when measuring the impact of Lean Six Sigma. With its focus on reducing errors and defects, companies should track improvements in their products or services’ quality after implementing Lean Six Sigma methodologies. This can be measured through product rejection rates, defect rates, or customer complaints related to product quality.
Apart from specific metrics related to cost reduction and quality control, there are also broader organizational benefits that come with implementing Lean Six Sigma practices. These include improved employee morale and engagement due to clearer roles and responsibilities within teams and streamlined processes leading to less stress at work. Tracking employee satisfaction levels before and after implementation can provide insights into these intangible but crucial aspects.
Challenges and Roadblocks in Implementing Lean Six Sigma
Implementing Lean Six Sigma in any business can bring about numerous benefits, such as improved efficiency, increased profits, and enhanced customer satisfaction. However, the road to achieving these benefits is not always smooth sailing. There are several challenges and roadblocks that organizations may encounter when adopting Lean Six Sigma methodologies.
One of the most significant challenges in implementing Lean Six Sigma is resistance to change. Many employees may be reluctant to embrace a new way of working or adapting to a new culture within the organization. This resistance can lead to friction among team members and hinder the successful implementation of Lean Six Sigma principles. To counter this challenge, it is vital for organizations to provide thorough training and education for all employees involved in the process. By investing time and resources into educating their workforce on the principles and benefits of Lean Six Sigma, organizations can help ease their transition into a culture of excellence.
Another common obstacle in implementing Lean Six Sigma is the lack of leadership support. For any organizational change to be successful, it must have top management’s commitment and involvement. Without support from leaders at all levels, employees may struggle with understanding the importance of Lean Six Sigma initiatives and see them as just another company initiative with no real impact on their day-to-day work. Therefore, it is essential for leaders to actively participate in training programs and demonstrate their commitment through actions rather than just words.
Limited resources can also pose a challenge when implementing Lean Six Sigma methodologies. Organizations may hesitate to invest in hiring additional staff or purchasing necessary tools for fear of increasing costs. However, taking shortcuts or using outdated tools can result in less reliable data analysis that could ultimately compromise process improvements’ effectiveness.
A lack of data-driven decision-making processes can also impede progress when implementing Lean Six Sigma strategies successfully. Organizations need accurate data analysis to identify areas for improvement accurately; however, without reliable data collection systems or proper utilization techniques, decision-making becomes challenging.
Strategies for Creating a Culture of Excellence Through Lean Six Sigma
Lean Six Sigma is not just a methodology or a set of tools, it is a culture that promotes continuous improvement and excellence. To truly create a culture of excellence within an organization, it is important to understand the principles and strategies behind implementing Lean Six Sigma in the workplace. In this section, we will discuss some key strategies that can help businesses create a culture of excellence through Lean Six Sigma.
1. Top-Down Approach: The first strategy for creating a culture of excellence through Lean Six Sigma is to have strong support from top-level management. This means that leaders should actively participate and lead by example in the implementation and adoption of Lean Six Sigma practices. When employees see their leaders fully committed to this approach, they are more likely to embrace it themselves.
2. Cultural Change: Adopting Lean Six Sigma requires a shift in mindset and behavior across all levels of the organization. It is not just about implementing new processes or procedures; it requires a cultural change where continuous learning, improvement, and problem-solving become ingrained in the company’s DNA. This can be achieved by providing training and resources to employees at all levels and ensuring everyone understands their role in contributing to the company’s success through Lean Six Sigma.
3. Clear Communication: Effective communication is vital when implementing any new initiative but even more so when trying to create a culture of excellence through Lean Six Sigma. Leaders must clearly articulate the goals, benefits, and expectations associated with adopting this methodology so that employees understand why it matters to the organization as well as how they fit into its overall goals.
4. Data-Driven Decision Making: One core principle of Lean Six Sigma is using data to make informed decisions rather than relying on intuition or guesswork. Encouraging data-driven decision-making at all levels builds trust within teams while also promoting accountability for results.
5. Continuous Improvement Mindset: A critical aspect of Lean Six Sigma is its focus on continuous improvement. This means that the organization must be open to change and willing to adapt processes and practices based on data and feedback. Having a growth mindset, where employees are continuously looking for ways to improve, is key to creating a culture of excellence.
6. Recognizing and Celebrating Success: It is important to recognize and celebrate successes along the way. When team members see the positive impact their efforts have on the organization, it motivates them to continue improving and striving for excellence.
Conclusion
In conclusion, the implementation of Lean Six Sigma methodology has proven to be a major contributor in driving businesses towards excellence. Its focus on eliminating waste and continuously improving processes helps organizations become more efficient, productive and competitive in today’s fast-paced business environment. By adopting this approach, companies can not only improve their bottom line but also create a culture of excellence where continuous improvement is engrained in every aspect of their operations. It is clear that Lean Six Sigma is a powerful tool for any organization striving for success and growth.
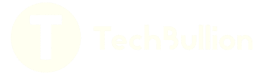