In today’s rapidly evolving business landscape, staying competitive and profitable can be a challenging feat. That’s why more and more companies are turning to Lean Six Sigma as a tried-and-true method for driving growth and increasing profitability. In this blog post, we’ll explore the numerous benefits of implementing Lean Six Sigma in your business, from streamlining processes to eliminating waste and improving customer satisfaction. Get ready to revolutionize your operations and skyrocket your success with Lean Six Sigma!
Introduction to Lean Six Sigma
Companies are constantly seeking ways to improve their processes, reduce waste, and increase profitability. One approach that has gained popularity over the years is Lean Six Sigma. This methodology combines the principles of lean manufacturing, which focuses on eliminating waste and increasing efficiency, with Six Sigma, a data-driven approach for process improvement.
The idea behind Lean Six Sigma is simple – to achieve better results with fewer resources and less time. By removing non-value adding activities and defects from processes, companies can improve customer satisfaction and drive growth while minimizing costs. It focuses on identifying and eliminating “waste” in every step of the production or service delivery process.
The origin of Lean Six Sigma can be traced back to Toyota’s production system in Japan in the 1950s. However, it gained widespread recognition after being successfully implemented by General Electric in the 1980s. Since then, many businesses across different industries have adopted this methodology to achieve significant improvements in their operations.
At its core, Lean Six Sigma aims to help businesses achieve consistent quality through continuous improvement efforts while reducing variation and errors. It provides a structured framework for problem-solving using data analysis rather than intuition or guesswork. The Five Phases of Lean Six Sigma – Define, Measure Analyze Improve Control (DMAIC) – guides organizations through a systematic approach for process improvement.
Lean Six Sigma also emphasizes the importance of employee involvement at all levels within an organization. Employees are trained as “belts” depending on their level of expertise – White Belt, Yellow Belt, Green Belt, Black Belt- to lead projects utilizing data analysis tools such as Pareto charts and root cause analysis.
Understanding the Principles and Methodologies of Lean Six Sigma
The principles and methodologies of Lean Six Sigma are essential to understand before implementing the framework in your business. Lean Six Sigma is a data-driven, process improvement methodology that combines the principles of lean manufacturing with the rigor and statistical analysis of Six Sigma. This approach aims to identify and eliminate inconsistencies, waste, and defects in processes across all areas of an organization.
The core principle of Lean Six Sigma is to focus on creating value for customers while minimizing or eliminating waste. It involves a continuous cycle of identifying areas for improvement, analyzing data, and implementing changes to optimize processes continuously. This mindset of continuous improvement is also known as the DMAIC (Define, Measure, Analyze, Improve, Control) process.
Defining the problem or opportunity is the first step in implementing Lean Six Sigma. It involves identifying customer needs and expectations clearly and mapping out existing processes. By defining what success looks like for both customers and internal stakeholders, organizations can align their efforts towards achieving those goals.
The second step is measuring current performance against defined metrics using data collection techniques such as surveys or process mapping tools. This step helps organizations gain insight into their processes’ specific strengths and weaknesses objectively.
Analyzing root causes behind inconsistencies or inefficiencies discovered during measurement allows businesses to determine where they should focus their attention for improvements effectively. Statistical analysis methods such as trend charts, Pareto diagrams, cause-and-effect diagrams are commonly used at this stage.
Using insights gained through analysis leads to making informed decisions on improving processes by removing non-value adding activities or streamlining workflows within them. The goal here is not only reducing costs but also enhancing quality by preventing errors from occurring.
How Lean Six Sigma Can Benefit Your Business
Lean Six Sigma is a powerful methodology that combines the principles of lean manufacturing and Six Sigma to optimize processes, reduce waste, and improve overall business performance. This approach has gained popularity in recent years as companies strive to stay competitive in today’s fast-paced market. In this section, we will delve into the specific ways in which implementing Lean Six Sigma can benefit your business.
1) Increased Efficiency and Productivity
One of the primary benefits of Lean Six Sigma is its focus on streamlining processes and minimizing waste. By utilizing tools such as value stream mapping, root cause analysis, and mistake-proofing techniques, businesses are able to identify inefficiencies and implement improvements that lead to increased efficiency. This results in not only cost savings but also improved productivity as employees are able to complete tasks more effectively and efficiently.
2) Better Quality Products or Services
The Six Sigma aspect of this methodology centers around achieving near-perfect levels of quality by reducing defects and variation within processes. By following statistical methods for identifying and eliminating root causes of errors, businesses can ensure their products or services meet high standards consistently. This leads to satisfied customers who have confidence in the quality of the company’s offerings.
3) Cost Reductions
By minimizing waste through Lean principles such as just-in-time production and inventory management, businesses can significantly reduce their costs. Additionally, by improving process efficiency, organizations save time which translates into reduced labor costs. The combination of these factors leads to tangible cost savings for businesses that implement Lean Six Sigma.
4) Improved Customer Satisfaction
As mentioned earlier, with better quality products or services comes increased customer satisfaction. This can result in repeat business from happy customers who are more likely to recommend your organization to others. Additionally, streamlined processes mean quicker delivery times leading to faster response rates for customer inquiries or issues.
5) Enhanced Data-Driven Decision Making
With data playing a critical role throughout the implementation of Lean Six Sigma methodologies from defining problems to measuring improvements, businesses are able to make more informed decisions. This is in stark contrast to traditional decision-making processes based on intuition or personal opinions, which can be less accurate and lead to suboptimal outcomes.
Real-Life Examples of Businesses Implementing Lean Six Sigma
Lean Six Sigma is a proven methodology that has been successfully implemented by businesses in various industries around the world. By combining the principles of lean manufacturing and Six Sigma, companies have been able to drive growth and achieve significant improvements in profitability. In this section, we will explore real-life examples of businesses that have implemented Lean Six Sigma and the benefits they have experienced.
1) General Electric (GE):
One of the most well-known success stories of Lean Six Sigma implementation is that of General Electric (GE). In the early 2000s, GE adopted a company-wide strategy to incorporate Lean Six Sigma practices into their operations. This transformation resulted in cost savings of over $2 billion annually for the company. Furthermore, it helped GE streamline its processes and improve customer satisfaction levels significantly.
2) Toyota:
Toyota is synonymous with lean production systems, and their continuous pursuit of excellence through continuous improvement has made them an industry leader. The company’s renowned Toyota Production System (TPS) is heavily based on lean principles. By embracing a “Kaizen” culture and implementing lean tools and techniques, Toyota has become one of the most successful automobile manufacturers globally.
3) Amazon:
The e-commerce giant Amazon has embraced Six Sigma methodologies as part of its relentless focus on customer satisfaction. By using data-driven decision-making processes, Amazon has been able to continuously improve its operations while maintaining exceptional service levels for its customers.
4) Honeywell:
Honeywell’s Aerospace division used Lean Six Sigma to identify inefficiencies in their supply chain process, resulting in significant cost savings. The implementation resulted in a reduction in lead times by 50%, defects by 72%, inventory by 25%, and scrap rates by 80%. As a result, Honeywell was able to better serve their customers’ needs while reducing costs.
5) Ford Motor Company:
Ford Motor Company successfully applied Lean Six Sigma principles across all departments within their organization. This led to improved quality, reduced defects, and increased customer satisfaction. The company also saw a significant reduction in operational costs, which contributed to their profitability.
6) Miami Valley Hospital:
Miami Valley Hospital implemented Lean Six Sigma to improve patient care processes and reduce medical errors. As a result, the hospital reported a 33% decrease in patient wait times and an 83% reduction in medication errors. These improvements have not only positively impacted patient outcomes but have also led to cost savings for the hospital.
Steps to Implementing Lean Six Sigma in Your Business
Implementing Lean Six Sigma in your business can bring about numerous benefits, such as increased efficiency, reduced waste, improved quality and ultimately, driving growth and profitability. However, the process of implementing this methodology can seem daunting at first. In this section, we will outline the key steps to successfully implementing Lean Six Sigma in your business.
1. Identify Areas for Improvement:
The first step towards implementing Lean Six Sigma in your business is to identify areas where there is scope for improvement. This could involve looking at processes that are causing delays or bottlenecks, identifying sources of waste or defects, or even gathering feedback from customers on areas that they feel could be improved.
2. Create a Cross-functional Team:
To ensure success with Lean Six Sigma implementation, it is important to form a cross-functional team comprising individuals from different departments and levels within the organization. This ensures that all perspectives are considered during the implementation process and also encourages collaboration and buy-in from all stakeholders.
3. Define Goals:
Once you have identified areas for improvement and formed a team to lead the implementation process, it is crucial to clearly define your goals and objectives. These goals should be specific, measurable, achievable and relevant to your business objectives.
4. Conduct Training:
It is essential to invest in training programs for employees as part of the implementation process. Training should cover not only the principles of Lean Six Sigma but also how it applies specifically to their roles within the organization. This will help employees understand their role in driving improvements and make them more motivated and engaged in the process.
5. Map Current Processes:
Before making any changes or improvements using Lean Six Sigma methodology, it is important to map out your current processes thoroughly. This helps identify potential areas for optimization or elimination of waste.
6. Implement Changes Incrementally:
A common mistake made by businesses when implementing Lean Six Sigma is trying to make too many changes at once which can overwhelm employees and create resistance towards the methodology. It is important to implement changes incrementally, starting with small improvements and gradually building upon them.
7. Monitor Progress and Make Adjustments:
To ensure that your Lean Six Sigma implementation is successful, it is crucial to monitor progress regularly. This can involve tracking key performance indicators (KPIs) and analyzing data to see if the changes made are leading to the desired results. If not, adjustments may need to be made in order to continue moving towards your goals.
Challenges and Tips for Success with Lean Six Sigma
The implementation of Lean Six Sigma may be challenging, but the rewards it offers in terms of growth and profitability are well worth the effort. As with any new approach or methodology, there are certain challenges that businesses may face when implementing Lean Six Sigma. However, by being aware of these challenges and following some key tips for success, businesses can effectively navigate through the implementation process and reap the full benefits of this powerful methodology.
One of the main challenges faced by businesses when implementing Lean Six Sigma is resistance to change. This can come from employees who are used to working in a certain way and may be apprehensive about adapting to a new system. To overcome this challenge, it is crucial for leaders to communicate effectively with their employees about the reasons behind the change and how it will benefit both them and the company as a whole. Regular trainings, workshops, and open forums can also help foster a culture of acceptance towards adopting Lean Six Sigma.
Another challenge is maintaining momentum throughout the implementation process. It is common for companies to become enthusiastic at first but lose steam over time due to various factors such as resource constraints or competing priorities. To avoid this, it is important for organizations to establish a clear timeline with achievable goals that align with their overall business objectives. Setting up regular check-ins and progress reviews can also help keep everyone on track towards successfully implementing Lean Six Sigma.
A major factor that contributes to successful implementation is executive buy-in from top-level management. Leaders must not only support but also actively participate in driving forward any changes brought on by Lean Six Sigma initiatives. Having senior leadership involved not only helps mitigate resistance from other employees but also reinforces its importance within the organization’s culture.
Additionally, another important tip for success in implementing Lean Six Sigma is ensuring effective project selection. In order to maximize results and minimize wasted efforts, businesses should prioritize projects that align directly with their strategic goals rather than just tackling random processes. This ensures that the efforts and resources invested in Lean Six Sigma yield substantial returns for the company.
Measuring the Impact of Lean Six Sigma on Growth and Profitability
Implementing Lean Six Sigma methodologies can bring numerous benefits to a business, such as improving efficiency, reducing waste, and enhancing customer satisfaction. However, what truly matters for any organization is how these improvements translate into tangible results in terms of growth and profitability. In this section, we will discuss the different metrics and tools that can be used to measure the impact of Lean Six Sigma on these crucial aspects of your business.
1. Cost Savings
One significant impact of implementing Lean Six Sigma is cost savings. By identifying and eliminating waste in processes, businesses can significantly reduce their operational costs. This includes both direct costs (labor, material, etc.) and indirect costs (overhead expenses). Lean Six Sigma brings a data-driven approach to identify areas for improvement and implement solutions that eliminate inefficiencies. Measuring cost savings before and after implementing Lean Six Sigma initiatives provides a clear indication of its impact on profitability.
2. Time Reduction
Another critical factor in measuring the success of Lean Six Sigma is time reduction or cycle time improvement. The methodology focuses on streamlining processes by removing unnecessary steps or activities, leading to quicker turnaround times for delivering products or services to customers. Reducing lead time not only improves customer satisfaction but also increases efficiency by utilizing resources more effectively.
3.Executing Projects Successfully
Successful project execution is an essential aspect when it comes to evaluating the impact of Lean Six Sigma on growth and profitability. This metric looks at how many projects were completed within budget and timeline while meeting quality standards set by the organization. With structured problem-solving techniques implemented by Lean Six Sigma teams, organizations can increase their project success rate significantly.
4.Customer Satisfaction
Happy customers are key to sustainable growth and increased profitability for any business – this is why measuring customer satisfaction levels is crucial when evaluating the impact of implementingLeanSixSigma.Customerfeedbackshouldbeacriticalcomponentofanyorganization’smeasurement strategy by collecting and analyzing customer satisfaction data before and after Lean Six Sigma implementation. Improving customer satisfaction through better processes leads to increased sales and repeat customers.
Conclusion
In today’s competitive business world, it is crucial for companies to continuously improve and streamline their processes in order to stay ahead. Implementing Lean Six Sigma methodology can provide numerous benefits such as increased efficiency, reduced waste and cost, improved customer satisfaction, and ultimately contribute to driving growth and profitability. By incorporating these principles into your business operations, you are setting a strong foundation for success and ensuring long-term sustainability in an ever-evolving market. So take the leap towards implementing Lean Six Sigma in your organization and reap the rewards of a more efficient and profitable business.
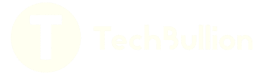