Conformal coatings are an incredibly important element in the world of electronics. They are often used by manufacturers of electronic devices to protect circuit boards and other electronic components from various environmental elements that may cause damage.
These coatings have found applications in various industries where electronic goods or systems are involved but very little seems to be known about them.
Let’s take a look at what exactly conformal coatings are, their applications, their advantages, and more.
What Are Conformal Coatings?
Conformal coatings are thin, electrically insulating films that are applied to the surface of printed circuit boards and other electronic components as a means of protecting them from environmental, physical, or chemical damage.
They can be applied in various ways, including dipping, spraying, or brushing. Once applied, the coating cures to form a hard, durable, and transparent film on the surface where it is applied.
Oftentimes, the protective layer formed may range from 25 to 250 micrometers in thickness and is usually transparent to allow easy identification of the board components. Moreover, the coating usually has a UV tracer to assist in the inspection as well as to identify the coating material in case a rework is needed.
Applications of Conformal Coatings
Conformal coatings are an essential part of many electronics, and their importance is only likely to grow in the future. However, these coatings are also used in a variety of applications, from protecting spacecraft from the harsh environment of space to keeping delicate medical devices free of contaminants.
They can also be used to improve the reliability of solder joints and prevent arcing and corrosion. Some are used to encapsulate sensitive components, protect against mechanical damage, and improve the heat dissipation of electronic devices.
Types of Conformal Coatings
There are several different types of conformal coatings depending on the material used. Each type has its own set of advantages and disadvantages.
The most common types, however, include the following:
1. Parylene
Although only in use in the past few decades, polymer-based coatings, such as polyarylene, are rapidly becoming an integral part of electronics manufacturing due to their robustness and efficiency. Parylene coatings come with several other advantages, including excellent uniformity, chemical inertness, and low outgassing.
Besides the material itself being budget-friendly, it is also easy to get cost-effective Parylene coating services as a manufacturer or even repair technician. Parylene is often considered among the best options for reducing the risk of electrical failure or damage due to various elements. The major difference is that unlike other types of coatings, parylene is applied through a vapor or vacuum deposition process.
2. Silicone
A far more versatile and durable type of conformal coating, silicone is extremely popular with electronic manufacturers due to its reliability and high level of compatibility. Silicone conformal coatings are highly resistant to high temperatures, making them ideal for use in exposed or high-heat areas. They are typically applied using a spray gun or brush and can be applied to both the surface of the device and to the component itself.
3. Acrylic
Acrylic coatings are a very sturdy and durable type of conformal coating that is almost invisible when applied to a surface. They are known for their ease of application, good moisture resistance, and simple drying process.
4. Fluoropolymers
Fluoropolymer coatings, which have the trade-name Teflon, are used widely in electronic circuits and devices due to their robustness. They are one of the most durable and longest-lasting types of coatings available and are often used in high-wear applications such as automotive and aerospace. Fluoropolymer coatings are also very resistant to chemicals, making them ideal for use in harsh environments.
5. Epoxy (sometimes referred to as polyester)
This is by far the most widely used form of conformal coating and one that is most commonly found on printed circuit boards. It is one of the least brittle and durable of the coatings available. However, epoxy conformal coatings are sometimes prone to electrical coupling, which is when two parts in close proximity produce an electrical charge, often resulting in short circuits. This is a major drawback, but often one that can be overcome with careful design.
6. Polyurethane
Polyurethane is a particularly good example of a flexible and resilient kind of coating used by the aerospace industry. Alongside dielectric properties, the material has adorable moisture resistance, abrasion resistance, and solvent resistance.
It is important to keep in mind that a specific type of coating used in an application might not always be suitable for all applications. For instance, silicone conformal coatings are highly suitable for electronics, but they aren’t usually suitable for airframes and aerospace applications due to their low adhesion to metal and their tendency to emit ethylene oxide.
Indeed, conformal coatings are an unsung hero, particularly in the electronics industry. By protecting our gadgets from various sources of damage, these coatings not only save us money but also help keep us safe.
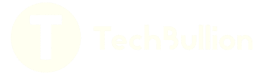