Introduction
What’s AR?
If you’re here to read this blog post, you probably already know what Augmented Reality is. So, better not bore ourselves with dictionary definitions. Before we dig deeper & marvel at the waves AR has made in the Manufacturing Industry, Let’s skim through a short introduction.
Unlike VR (Virtual Reality), AR is not a completely virtual immersive environment. Instead, it poses as a digital layer on existing physical surroundings. Augmented Reality enhances a physical environment through photos, videos, information & etc. It does so by overlaying digital content onto the real world, in real-time. AR operates with the help of cameras & sensors in order to detect a user’s surroundings to project virtual content. It can be experienced through various devices such as smartphones, tablets, smart glasses, or headsets. AR projections can include anything & everything – From simple text & images to animations & 3d models that appear integrated into the real world.
It has many applications in several major industries like the Manufacturing Industry, Automobile Industry & etc. Other fields of usage include Education, Entertainment, Marketing & more. Like the title & intro suggest – Today, we will focus on the role of AR in the Manufacturing Industry.
Importance of AR in the manufacturing industry
AR offers the manufacturing industry endless possibilities. Following is a brief summary of its numerous applications:
- Improving Training and Onboarding: Using AR technology, immersive training programs that simulate real-life scenarios for workers are created. This helps to reduce the time and money spent on traditional training methods.
- Enhancing Design and Development: AR assists designers and engineers in virtual visualization and testing product designs. Thereby reducing the need for physical prototypes and optimizing the product development cycle.
- Streamlining Manufacturing Processes: Using AR, workers are guided through complex manufacturing processes, receiving real-time instructions and feedback. This assists to reduce errors, improve quality, and increase efficiency.
- Enabling Remote Support: AR is used to give workers on the field remote assistance. For instance: A remote expert could use AR technology to direct technicians through a maintenance or repair job, cutting downtime and boosting output.
Overview
The manufacturing sector’s usage of augmented reality (AR) is the main topic of this blog. By superimposing digital information over the real world, augmented reality (AR) technology gives workers access to real-time information and direction. Design and prototyping, assembly and production, maintenance and repair, as well as training and teaching, are just a few of the manufacturing-related uses for augmented reality technology. AR may improve productivity, improve safety, and reduce costs in manufacturing operations, making it an attractive technology for organizations in the industry. The initial expenditure in hardware and software, as well as ongoing maintenance and updates, might make integrating AR challenging.
What’s AR and How Does it Work?
By superimposing computer-generated content over the real world, augmented reality, or AR, technology, improves the user’s sense of reality. The user can interact with a variety of real-world and virtual surroundings thanks to this technology.
AR technology and hardware:
Using hardware including cameras, sensors, and displays, augmented reality (AR) technology overlays digital content on top of the user’s field of vision of the physical environment. Smart glasses, smartphones, tablets, and head-mounted displays are just a few of the gadgets that allow users to experience augmented reality.
Types of AR:
Basically, there are two types of AR:
- Marker-based AR: This type of AR uses visual markers to prompt the display of digital material, like QR codes or image recognition. The camera may superimpose 3D pictures or other content over the actual surroundings when it recognizes markers.
- Markerless AR: Markerless AR, sometimes referred to as position-based AR, determines the user’s location and orientation using GPS, accelerometers, and other sensors. Depending on the user’s location, the technology can then overlay pertinent digital content onto a real-world setting.
How AR works in the manufacturing industry:
By enabling hands-free, interactive viewing of complex data, instructions, and 3D models, augmented reality technology is revolutionizing the manufacturing sector. AR headsets can be used to overlay instructions and feedback on processes and procedures on an employee’s production line or equipment.
The usage of AR in remote training and cooperation enables professionals to supervise employees’ work from a distance. As a result, less travel may be required, and worker safety may also be improved.
Benefits of AR in the Manufacturing Industry
Increased productivity:
- Improved efficiency in assembly and production: AR technology can provide workers with step-by-step guidance during assembly and production, reducing errors and improving efficiency. AR can also provide real-time feedback on performance, allowing workers to optimize their processes.
- Streamlined maintenance and repair processes: AR technology can provide maintenance and repair workers with visual overlays of machinery and equipment, making it easier to diagnose and repair problems quickly and accurately.
Enhanced safety:
- Training and education of employees: AR technology can provide realistic simulations of dangerous scenarios and equipment, allowing workers to practice safety procedures and protocols in a risk-free environment.
- Accident prevention: AR technology can provide workers with real-time safety warnings and alerts, reducing the risk of accidents and injuries.
Cost savings:
- Reduced waste: AR technology can help reduce waste by improving production processes and minimizing errors and defects.
- Lowered training costs: AR technology can provide interactive and engaging training experiences, reducing the need for expensive training programs and reducing training time.
- Decreased downtime: AR technology can provide real-time information on equipment and machinery, allowing for proactive maintenance and reducing downtime due to unexpected failures or breakdowns.
AR Applications in the Manufacturing Industry
Design and prototyping:
- Virtual prototyping: AR technology can be used to create virtual prototypes, allowing designers to visualize and test designs before physically producing them. This can save time and money by reducing the number of physical prototypes needed.
- Real-time feedback on design changes: AR technology can provide real-time feedback on design changes, allowing designers to make adjustments and see the impact on the final product.
Assembly and Production:
- Real-time instructions and guidance: AR technology can provide workers with real-time instructions and guidance during assembly and production, improving efficiency and reducing errors.
- Quality control and inspection: AR technology can be used for quality control and inspection by providing workers with visual overlays that highlight defects and anomalies, improving the accuracy and efficiency of inspections.
Maintenance and Repair:
- Remote assistance and collaboration: AR technology can be used for remote assistance and collaboration, allowing experts to guide workers through maintenance and repair tasks from a remote location.
- Predictive maintenance: AR technology can provide real-time data on equipment and machinery, allowing for predictive maintenance and reducing downtime due to unexpected failures or breakdowns.
Case Studies of AR Implementation in Manufacturing:
Boeing: In order to increase productivity and decrease errors during the construction of aeroplanes, Boeing has used AR technology. While assembling, augmented reality headsets give workers real-time instructions and direction, eliminating the need for paper instructions and increasing process accuracy. AR is also used for quality control and inspection, enabling staff to recognize flaws and abnormalities with speed and accuracy.
General Electric: To increase the effectiveness and security of its maintenance and repair procedures, General Electric has adopted AR technology. With the aid of augmented reality (AR) headsets, employees can see visual overlays of machinery and equipment, which makes it simpler to swiftly and properly identify and fix issues. AR is also utilized for remote collaboration and help, enabling professionals to direct workers through tasks from a distance.
Ford: To increase the effectiveness of its design and prototyping processes, Ford has adopted AR technology. The quantity of physical prototypes needed is decreased since AR enables designers to envision and test designs before making them. In order to allow designers to make adjustments and observe how they affect the finished product, AR is also utilized to obtain immediate feedback on design changes.
Siemens: To increase the effectiveness and security of its maintenance and repair procedures, Siemens has adopted AR technology. With the aid of augmented reality (AR) headsets, employees can see visual overlays of machinery and equipment, which makes it simpler to swiftly and properly identify and fix issues. AR is also utilized for remote collaboration and help, enabling professionals to direct workers through tasks from a distance. Siemens has also used augmented reality technology to offer real-time data and analytics on its manufacturing processes, enabling proactive maintenance and process improvement.
Challenges in Implementing AR in Manufacturing:
Technical limitations:
- Hardware and software compatibility: AR technology requires compatible hardware and software, which can be a challenge in manufacturing environments where existing systems may not be compatible.
- Security concerns: AR technology may introduce new security concerns, such as data privacy and protection, which must be addressed to ensure the safety and security of sensitive information.
Employee training:
- Learning curve for new technology: AR technology may require new skills and knowledge, which can be challenging for employees to learn and implement.
- Resistance to change: Employees may be resistant to change, especially if they are used to traditional methods and processes.
Cost:
- Initial investment in hardware and software: AR technology can be expensive, requiring a significant initial investment in hardware and software.
- Maintenance and upgrades: AR technology requires ongoing maintenance and upgrades, which can be costly and time-consuming.
Future of AR in Manufacturing:
Advancements in AR technology:
- Wearable AR devices: The development of wearable AR devices, such as smart glasses, could provide workers with a more immersive and hands-free experience, improving efficiency and productivity.
- Haptic feedback: Haptic feedback technology, which provides tactile feedback through vibration or other sensations, could enhance the realism and effectiveness of AR training and simulations.
- Integration with other technologies: Integration of AR with other technologies such as robotics and IoT, could create new opportunities for automation and process optimization in manufacturing.
Potential impact on the manufacturing industry:
- Improved efficiency and productivity: AR technology has the potential to significantly improve efficiency and productivity in the manufacturing industry by providing workers with real-time guidance, reducing errors, and improving training and education.
- Creation of new jobs: The implementation of AR technology in manufacturing could create new job opportunities for workers with the skills and knowledge to operate and maintain the technology.
Conclusion
The fundamentals of augmented reality (AR) are covered in this article, along with applications for the manufacturing sector. We have discussed many types of augmented reality, their advantages for the manufacturing industry, case studies of their application there, their difficulties, and their prospects for the future.
Through increasing effectiveness, productivity, safety, and cost savings, AR has the potential to change the manufacturing sector. Several industrial processes, including design and prototyping, assembly and production, and maintenance and repair, can benefit from the usage of augmented reality (AR) technology.
Manufacturers ought to investigate the advantages of augmented reality technology and think about integrating it into their processes. Collaboration between manufacturers, workers, and technology suppliers is essential for the effective and long-lasting adoption of AR technology.
The manufacturing sector will likely benefit significantly from the rapid development of AR technology. In order to optimize their processes and remain competitive, manufacturers must be informed about new developments in augmented reality technology.
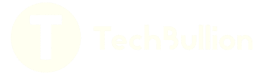