Welcome to the fascinating world of Industry 4.0! In this era of technological advancements, machines are becoming smarter, processes more efficient, and industries more interconnected than ever before. The concept of Industry 4.0 is revolutionizing the way we work and shaping the future of manufacturing and production. From its humble beginnings to its potential impact on our workforce, let’s delve into what makes Industry 4.0 so revolutionary and how it is transforming the industrial landscape as we know it. So grab a cup of coffee and get ready for an exhilarating journey into the world of high performance tool material in Industry 4.0!
The concept of Industry 4.0
The concept of Industry 4.0 refers to the fourth industrial revolution, where digital technologies merge with traditional manufacturing processes to create a highly interconnected and intelligent system. It encompasses a range of cutting-edge technologies such as artificial intelligence, robotics, Internet of Things (IoT), big data analytics, and cloud computing.
At its core, Industry 4.0 aims to optimize efficiency, productivity, and flexibility in the industrial sector. By integrating smart machines with advanced data analytics systems, manufacturers can gain real-time insights into their operations and make informed decisions for enhanced performance.
One key aspect of Industry 4.0 is the concept of cyber-physical systems (CPS). These are physical machines connected through a network that communicate and cooperate with each other autonomously. This enables seamless collaboration between humans and machines in various stages of production.
Another significant feature is the ability to collect vast amounts of data from sensors embedded in machinery or products during the manufacturing process. This wealth of information provides valuable insights for predictive maintenance strategies, quality control measures, supply chain management optimization, and overall process improvement.
Industry leaders recognized the potential benefits that Industry 4.0 could bring to their businesses – improved production efficiency, reduced costs through optimized processes,
and faster time-to-market for new products or services.
The challenges of Industry 4.0
The challenges of Industry 4.0 are not to be underestimated. As technology continues to advance at an unprecedented pace, businesses must grapple with a range of obstacles in order to fully embrace the potential benefits that come with this new era.
One of the key challenges is the need for organizations to invest in and implement new technologies. This can be a costly endeavor, requiring significant financial resources and time for training employees on how to effectively use these tools. Additionally, there is often resistance from workers who fear that automation will replace their jobs.
Another challenge lies in data security and privacy concerns. With increased connectivity and reliance on digital systems, there is an inherent risk of cyberattacks and breaches. Businesses must prioritize cybersecurity measures and ensure that sensitive information remains protected.
Furthermore, there is a growing skills gap as traditional job roles evolve or become obsolete altogether. The workforce needs to adapt by acquiring new skills such as data analytics, artificial intelligence, and robotics programming. This requires investment in education and training programs.
Additionally, the integration of different technologies across various departments within an organization can pose compatibility issues. Ensuring seamless communication between machines, systems, and people becomes crucial for maximizing efficiency.
The future of Industry 4.0
The future of Industry 4.0 holds immense potential for advancements and innovation across various sectors. With the continuous evolution of technology, we can expect even greater integration of digital systems and physical processes in manufacturing and beyond.
One aspect that will shape the future of Industry 4.0 is the rise of artificial intelligence (AI) and machine learning. These technologies have already started to revolutionize industries by enabling machines to learn from data, make decisions, and perform tasks with minimal human intervention. As AI continues to advance, it will undoubtedly enhance productivity, efficiency, and accuracy in manufacturing processes.
Another significant development on the horizon is the Internet of Things (IoT). This interconnected network allows devices to communicate with each other through sensors and embedded software. By leveraging IoT capabilities, manufacturers can gather real-time data from their equipment, optimize operations remotely, predict maintenance needs accurately, and improve overall performance.
Furthermore,the emergence of high-performance tool materials will contribute significantly to advancing Industry 4.0 capabilities.
High-performance tool materials exhibit superior strength,durability,and heat resistance characteristics,enabling them to withstand extreme conditions encountered during manufacturing processes.
These materials not only increase production efficiency but also reduce downtime due to tool failure,resulting in cost savings for manufacturers.
Conclusion
Industry 4.0 is revolutionizing the way we work and operate in various industries. This concept, which originated from Germany’s vision of a fourth industrial revolution, brings together advanced technologies such as IoT, AI, robotics, and data analytics to create smart factories and optimize production processes.
The benefits of Industry 4.0 are immense. Companies can achieve higher productivity levels and efficiency by leveraging real-time data and automation. With predictive maintenance systems, they can minimize equipment downtime and reduce costs significantly. Additionally, the ability to customize products based on individual customer preferences has opened up new opportunities for businesses to cater to diverse markets effectively.
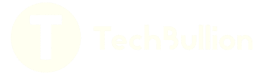