Rahul Gangolli is a Senior Technical Program Manager at Amazon with a strong background in manufacturing efficiency, robotics, and program management. With extensive expertise in Lean manufacturing and standardized reporting, Rahul focuses on driving operational improvements and advancing scalable processes in manufacturing. His work emphasizes the integration of cutting-edge methodologies and technologies to enhance program management, efficiency, and communication in complex manufacturing environments.
Abstract: Standardized reporting mechanisms play a transformative role in advancing program management across the manufacturing sector. Rooted in foundational quality control principles and now enhanced by Industry 4.0 digital technologies, standardized reporting is vital for optimizing operational efficiency, improving communication, and enabling data-driven decision-making. Organized into financial, operational, industry-specific, and productivity-focused reports, these frameworks provide essential insights that align stakeholders and streamline processes. The discussion also addresses implementation challenges, including resistance to change and the limitations in industries with high customization demands. Future trends, such as real-time analytics, enhanced cybersecurity, and integrated dashboards, promise to expand the influence of standardized reporting as manufacturing embraces digital transformation. This study highlights the essential role of structured reporting in fostering agility and competitiveness within modern manufacturing environments.
The implementation of standardized reporting mechanisms in the manufacturing sector has become a pivotal element in enhancing program management, driving efficiency, and fostering effective communication across various operational levels. Originating from early quality control methodologies developed by figures like Walter A. Shewhart and Joseph M. Juran, standardized reporting has evolved to incorporate advanced digital technologies as part of Industry 4.0 advancements[1]. These systems have become indispensable in modern manufacturing, offering a structured approach to monitoring processes, managing resources, and ensuring compliance with industry standards.
Standardized reporting mechanisms serve multiple functions within the manufacturing environment, categorized into financial, operational, industry-specific, and productivity reports. Each type plays a crucial role in maintaining operational efficiency, tracking production metrics, and supporting strategic decision-making[2]. By providing clear and consistent data, these reports not only enhance productivity but also streamline communication between stakeholders, thus ensuring a unified understanding of the operational landscape[3]. However, the adoption of these systems is not without challenges, including resistance to change and potential limitations in flexibility, particularly in industries that require high levels of customization[4].
The impact of standardized reporting on program management is profound, with significant improvements in process tracking, risk management, and decision-making capabilities. Enhanced visibility over production status and team performance allows for more informed and timely decisions, aligning with the principles of Lean manufacturing to reduce waste and optimize efficiency[5]. Moreover, standardized reporting fosters a culture of accountability and open communication, critical for effective risk management and strategic planning[6].
As the manufacturing sector continues to evolve with the integration of the Industrial Internet of Things (IIoT) and advanced data analytics, the role of standardized reporting mechanisms is expected to expand. Future trends indicate a focus on real-time data insights, cybersecurity measures, and the development of comprehensive dashboards to accommodate diverse stakeholder needs[7][8]. These advancements will further solidify the importance of standardized reporting in maintaining competitiveness and driving innovation in an increasingly digital manufacturing landscape.
Historical Background
The concept of standardized reporting mechanisms in manufacturing can trace its origins back to early quality control principles established by pioneers such as Walter A. Shewhart and Joseph M. Juran. Shewhart’s foundational work laid the groundwork for quality control, which was crucial in shaping the evolution of manufacturing processes[1]. His contributions, further expanded by Juran, led to the development of Total Quality Control, highlighting the importance of structured processes in maintaining high standards in production[1].
As manufacturing industries progressed, the introduction of Lean manufacturing methodologies further emphasized the need for standardized processes, including reporting mechanisms[9]. Standard work charts, part of Lean’s structured approach, helped document precise work sequences and inventory requirements, thereby minimizing waste and enhancing productivity[9]. Such frameworks necessitated standardized reporting to track operational efficiency and spot improvement opportunities[2].
In recent years, the advent of the Fourth Industrial Revolution, or Industry 4.0, has transformed manufacturing operations by integrating digital technologies, such as the Industrial Internet of Things (IIoT)[7]. This digital evolution has underscored the importance of data standardization, ensuring that information collected from various sources can be effectively analyzed and utilized[7]. Solutions like MachineMetrics have emerged to facilitate the transformation of machine data into standardized reports, driving operational insights and decision-making processes within modern manufacturing environments[7].
The historical progression from early quality control frameworks to today’s sophisticated digital reporting systems highlights the continuous evolution and increasing importance of standardized reporting mechanisms in enhancing program management in the manufacturing sector.
Types of Standardized Reporting Mechanisms
Standardized reporting mechanisms play a crucial role in enhancing productivity and operational efficiency within program management, particularly in the manufacturing sector. These mechanisms can be categorized into several types, each serving distinct functions that address various aspects of business operations.
Financial Reports
Financial reports are essential standardized mechanisms that offer a comprehensive overview of an organization’s economic activities. They include key financial metrics necessary for monitoring a business’s financial health, allowing organizations to identify potential issues and opportunities for improvement. Such reports help in keeping finances in check, which is critical for achieving overall success in the competitive manufacturing industry[2].
Operational Reports
Operational reports are widely used in manufacturing as well as logistics and retail sectors. These reports focus on tracking inventory, production, and costs, among other elements. They enable businesses to maintain optimal operational efficiency by identifying bottlenecks and suggesting possible enhancements. Operational reports are a key component in ensuring that goods are produced in accordance with specifications and quality standards are maintained[2][10].
Industry-Specific Reports
Another important category is industry-specific reports, which cater to the unique needs of different manufacturing sectors. These reports provide tailored insights and data relevant to specific industries, aiding businesses in making informed decisions and strategic planning. The standardized nature of these reports ensures that all stakeholders have a unified understanding of the operational landscape, thus facilitating smoother communication and decision-making processes[2].
Productivity and Efficiency Reports
Standardized productivity and efficiency reports aim to eliminate inefficiencies and promote a common framework for data consumption. By providing a clear and consistent presentation of relevant data, these reports enable stakeholders to swiftly understand and act upon the information provided. This not only enhances productivity but also ensures that project managers and other stakeholders can focus their time on core activities rather than getting bogged down in creating customized reports for every stakeholder[3].
Impact on Program Management
Standardized reporting mechanisms significantly impact program management within the manufacturing sector by enhancing efficiency, communication, and decision-making processes. The use of standardized systems in manufacturing facilitates the tracking and management of processes and tasks, ensuring all steps are completed within quality standards and on time[5]. This standardization aligns with the principles of Lean manufacturing, which aims to eliminate waste and increase operational efficiency[9]. By providing a clear framework for reporting, these mechanisms enable better collaboration and data sharing among multiple manufacturing sites and stakeholders[5].
Furthermore, standardized reporting mechanisms aid in maintaining visibility over production status, team performance, and resource usage[7]. This is crucial for shop floor managers and manufacturing engineers, who can struggle with limited visibility without such systems. The ability to access real-time data through connected devices improves program management by allowing stakeholders to make informed decisions quickly and efficiently[7].
Additionally, standardized reporting contributes to effective risk management by fostering a culture of open communication and accountability[6]. By standardizing communication channels, the potential for miscommunication is reduced, thereby ensuring that reports and critical information are accurately conveyed[3]. This not only enhances the reliability of reporting but also supports the implementation of risk mitigation strategies by providing a consistent framework for assessing and responding to potential risks[6].
Case Studies
The implementation of standardized reporting mechanisms in program management within the manufacturing sector is illustrated through various case studies that highlight both the challenges and benefits of these systems. One notable example involves a manufacturing company that sought to improve its operational risk management by aligning incentives with risk management goals and promoting a risk-aware culture[6]. This company experienced improved accountability and risk-conscious behavior among its employees as a result of its standardized approach to risk management[6].
Another case study focuses on the integration of IT systems within a manufacturing company to achieve end-to-end visibility and control over operations[11]. By utilizing interconnected systems and standardized protocols, the company was able to enhance its operational efficiency, demonstrating the significant impact of standardized reporting mechanisms on program management[11].
Additionally, a company involved in Product Configuration Systems (PCS) development encountered challenges such as maintenance, documentation, and communication with domain experts[12]. Through the implementation of standardized reporting practices, the company improved knowledge management and system quality, thereby overcoming some of these challenges[12].
These case studies underscore the importance of standardized reporting mechanisms in overcoming managerial challenges and improving operational outcomes in the manufacturing industry.
Challenges and Limitations
Implementing standardized reporting mechanisms in program management within the manufacturing sector comes with a unique set of challenges and limitations. One significant issue is the potential decrease in agility, as a commitment to specific standardized methods may limit an organization’s ability to adapt to new technologies or methods of manufacturing[4]. This lack of flexibility can pose a substantial obstacle in an industry that frequently undergoes technological advancements.
Another challenge is resistance from personnel within the organization. While standardized processes can enhance productivity by eliminating inefficiencies, some workers, particularly those with long-standing practices, may not immediately see the value of such changes[9]. Supervisors may also be reluctant to adopt new methods imposed by external entities, believing they are capable of managing their departments independently[9]. This resistance can act as a barrier to effective implementation unless adequately addressed through comprehensive change management strategies.
Additionally, standardization can limit product variety, which is a significant drawback for companies that offer customized products[4]. This lack of choice might hinder the organization’s ability to meet diverse customer needs, thereby affecting its competitive edge in the market.
Resource constraints also present a challenge. The successful implementation of standardized reporting systems requires adequate resources, including advanced data analytics tools and platforms[11]. Without sufficient resources, organizations may struggle to monitor and evaluate progress towards their strategic objectives effectively, thereby compromising their overall goals[13].
Finally, managing stakeholder expectations is critical. With numerous stakeholders involved, from shop floor managers to manufacturing engineers, ensuring that all parties have visibility into production status and performance metrics is crucial[7]. Failure to achieve this can lead to dissatisfaction and further resistance to standardized reporting initiatives.
Overcoming these challenges requires strategic planning, robust data management practices, and a willingness to engage with and educate all organizational levels about the benefits of standardized reporting systems[14][11].
Future Trends
As the manufacturing industry continues to evolve with the advancements of Industry 4.0 and the Industrial Internet of Things (IIoT), the future of standardized reporting mechanisms in program management is set to be shaped by several key trends. One of the major trends is the increasing integration of advanced data analytics and IT solutions, which are essential for deriving actionable insights and optimizing manufacturing processes[7][11]. These technologies are expected to further enhance decision-making capabilities by providing real-time, data-driven insights into operational efficiency, inventory management, and production costs[2].
Another anticipated trend is the ongoing modernization of technology infrastructure within the manufacturing sector. This involves implementing integrated systems that ensure seamless data flow and collaboration across the supply chain[8].. With the growing emphasis on cybersecurity, manufacturers will also prioritize robust measures to safeguard sensitive data, ensuring the integrity and accessibility of their standardized reporting systems[8].[11].
Moreover, the development of one-size-fits-all dashboards is likely to gain traction. These dashboards aim to meet the diverse requirements of various stakeholders by offering scalable solutions that accommodate the ever-increasing demands for data compatibility and analytics[15]. However, the commitment to specific standardization methods may also present challenges, such as limiting product variety and reducing agility, particularly for organizations that offer customized products[4].
Lastly, as the industry embraces digital transformation, the role of standardized reporting mechanisms will expand beyond traditional applications. There will be a growing focus on the deployment of advanced data governance frameworks and analytics platforms to facilitate intelligent forecasting and predictive actions[11]. This shift will enable manufacturers to proactively address operational challenges and maintain competitiveness in an increasingly dynamic market environment.
References
[1] Investopedia Team. (2024, June 19). What is total quality management (TQM), and why is it important? Investopedia. https://www.investopedia.com/terms/t/total-quality-management-tqm.asp
[2] Graupp, P. (n.d.). Standardized work: What is it and when to apply it. TWI Institute. https://www.twi-institute.com/what-is-standardized-work/
[3] RIB Software. (2024, June 17). A guide to the top 14 types of reports with examples of when to use them. RIB Software. https://www.rib-software.com/en/blogs/types-of-reports-examples
[4] Immerman, G. (2022, March 24). The importance of data standardization in manufacturing. MachineMetrics. https://www.machinemetrics.com/blog/data-standardization-in-manufacturing
[5] University of Minnesota. (2016). 11.1 Operations management in manufacturing. In Exploring Business. https://open.lib.umn.edu/exploringbusiness/chapter/11-1-operations-management-in-manufacturing/
[6]Taylor, P. (2021, October 25). The 5 key benefits of standardized reports. Office Timeline. https://www.officetimeline.com/blog/guest-post-the-5-key-benefits-of-standardized-reports
[7] Quickbase. (2024, February 29). Project management can improve the efficiency and success of your manufacturing projects. Quickbase. https://www.quickbase.com/blog/project-management-manufacturing
[8] FasterCapital. (n.d.). Implementing effective risk monitoring and reporting mechanisms. FasterCapital. https://fastercapital.com/topics/implementing-effective-risk-monitoring-and-reporting-mechanisms.html
[9] Team Kissflow. (2024, October 23). Top 3 challenges of IT in manufacturing industry and how to solve them. Kissflow. https://kissflow.com/solutions/manufacturing/it-challenges-in-manufacturing-industry/
[10] Elsevier B.V. (2020). The main challenges for manufacturing companies in implementing and utilizing configurators. https://www.sciencedirect.com
[11] Van Echtelt, R. (2024, April 5). The benefits of standardization in the manufacturing industry. AG5. https://www.ag5.com/benefits-of-standardization-in-manufacturing/
[12] SHRM. (2024, October 28). Practicing strategic human resources. SHRM. https://www.shrm.org/topics-tools/tools/toolkits/practicing-strategic-human-resources
[13] Quain, S. (n.d.). Barriers & challenges to change implementation. Chron. https://smallbusiness.chron.com/barriers-challenges-change-implementation-30842.html
[14] Anderson, L. (2024, February 7). 10 common supply chain management problems (and solutions) for your business. Cart.com. https://cart.com/blog/supply-chain-management
[15] Liulcenco, A. (2022, October 18). The benefits of standardized reporting. Mercury Media Technology GmbH. https://www.mercurymediatechnology.com/en/blog/the-benefits-of-standardized-reporting/
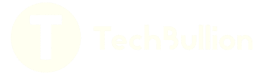