A prismatic cell is a type of lithium-ion battery cell that has a rectangular shape. It is composed of stacked or flattened electrodes and separators enclosed in a rigid casing. It is scalable and is available in various sizes, ranging from small capacities suitable for portable electronic devices to larger capacities for electric vehicles and energy storage systems. That is why it has gained much popularity.
To help understand this type of battery comprehensively, this guide will show you the advantages and disadvantages of prismatic cells, as well as explores the ongoing improvements in their design and technology. Let’s see!
Understanding the Pros and Cons of Prismatic Cells
Following are some pros and cons of prismatic cells when they are used practically in industry.
Pros of Prismatic Cells
- Prismatic cells have higher energy density due to efficient use of space. This makes them ideal for applications where maximizing energy storage in a compact form factor is critical so that they are part of electric vehicles and portable electronics.
- Prismatic cells offer configuration flexibility. The battery manufacturing process is complex, but prismatic cells’ rectangular shape allows for more flexibility in designing battery packs. Manufacturers can arrange cells in different configurations to optimize space, achieving the desired voltage and capacity requirements.
- Prismatic cells are easy to integrate. Due to their flat shape, prismatic cells are more accessible to integrate into devices and vehicles. This reduces the complexity of the battery manufacturing process.
- Prismatic cells have better thermal management. The flat surface area of prismatic cells enhances heat dissipation and thermal management compared to cylindrical cells. This feature helps maintain stable operating temperatures, prolong battery life, and enhance safety during operation.
- Prismatic cells often own robust outer casings. It provides better protection against physical damage and environmental stresses. This durability makes them ideal for applications where environmental stressors are present.
Cons of Prismatic Cells
- The manufacturing process for prismatic cells involves precise assembly and sealing, which can be more expensive than that for cylindrical cells. Initial setup costs for specialized equipment and tooling may also contribute to higher production costs.
- Sometimes, prismatic cells are susceptible to swelling, especially under conditions of high temperature or improper charging or discharging. This can affect battery performance.
- Ensuring uniform quality and performance across prismatic cell batches can be challenging.
Pros and Cons When Manufacturing Prismatic Cells on the Assembly Line
Battery manufacturing is a process of efficient production but complication. Here’s why:
Pros
- Manufacturing prismatic cells on an automated assembly line ensures consistency in cell assembly, reducing human error and increasing production efficiency. Moreover, automated processing lowers labor costs and reduces waste
- Automated manufacturing allows for tighter control over critical parameters such as cell thickness, electrode alignment, and electrolyte filling
- Automated battery assembly machines can be scaled up more efficiently to cater for the growing demands for prismatic cells. This scalability ensures that production capacity can be adjusted efficiently in response to market dynamics and customer requirements
- Automated manufacturing of prismatic cells also offers enhanced safety. There is no need for manual handling of hazardous materials
Cons
- Maintaining automated production equipment for prismatic cells involves regular checking and tuning. It requires skill and can cost you more.
- Manufacturers need skilled personnel capable of troubleshooting technical issues and optimizing production processes to maximize efficiency and yield.
- Automated production lines for prismatic cells may have limited flexibility compared to manual assembly methods.
Overview of Maintaining Peak Performance Before Delivery
Before dispatching batteries from the factory, it is crucial to address potential issues your clients care about the most.
What are the Scenarios You Would Meet Before Delivery?
There are several situations where a battery might exhibit issues that need resolution before it can be shipped to customers:
- Manufacturing Defects: Minor defects in the assembly or in the materials used (such as separators, electrodes, or electrolyte inconsistencies) can affect the battery’s overall performance and safety
- Storage Conditions: Batteries stored in the factory for an extended period might experience a decrease in performance or require recharging and reconditioning to ensure they retain their specified charge capacity and lifecycle
- Firmware Updates: For batteries integrated with smart management systems, firmware updates are essential to ensure compatibility with devices they will power and optimize their performance according to the latest enhancements
- Compliance with Standards: Batteries must meet various international and regional standards related to safety, transportation, and environmental impact before they can be dispatched
How to Ensure Battery Performance in Peak Before Delivery?
Before prismatic cells leave the factory, follow the necessary steps. These can ensure their performance and reliability.
Rigorous Quality Control
Each prismatic cell undergoes rigorous quality control testing. It verifies electrical performance, capacity, and safety parameters. Testing includes checks for internal resistance and voltage stability.
Checking against Environmental Stressors and Physical Damage
Prismatic cells are subjected to environmental stress tests, including temperature cycling, humidity exposure, and vibration testing. Cells are typically packaged in robust containers that shield them from physical damage. It also prevents exposure to moisture or contaminants.
Pre-Charging
Prismatic batteries should be shipped with an optimal state of charge to minimize degradation during transit. This charge level is considered a safe balance for maintaining battery health and reducing the risk of incidents during shipping.
Necessary Information like Batch Number and Bar Code
Detailed documentation that includes manufacturing batch information, test results, and compliance certifications must be checked.
Advantages of SZJ Automation’s Prismatic Cell Turnkey Solution
For manufacturing the best prismatic cell for your clients, the Prismatic Cell Turnkey Solution presented by SZJ Automation could be qualified. It represents a groundbreaking advancement of technologies in the realm of battery manufacturing machines.
By incorporating SZJ Automation’s self-owned proprietary continuous laser welding technology, this solution dramatically boosts production efficiency, offering a 3-5 times increase over traditional segmental welding techniques. Designed to deliver a consistent productivity rate of 6-20 pieces per minute (PPM), this turnkey solution ensures optimal operational throughput and precision.
In addition to its advanced production capabilities, SZJ Automation’s Prismatic Cell Turnkey Solution includes rigorous quality assurance procedures to ensure that each unit meets the highest standards before leaving the factory. Each prismatic and blade cell undergoes a detailed welding inspection, utilizing precision instruments to detect any inconsistencies or defects that could compromise performance or safety. Following the welding inspection, cells are subjected to a thorough Helium Inspection, a critical step designed to ensure the integrity of the cell’s seal and detect any microscopic leaks that could affect long-term reliability and efficiency. These meticulous inspection processes guarantee that every battery delivered to our clients operates at peak performance, thereby enhancing product reliability and customer satisfaction.
As a result, SZJ Automation’s prismatic cell turnkey manufacturing solution not only streamlines production processes but also enhances the overall quality of prismatic and blade cells, making it an ideal choice for manufacturers aiming to scale operations efficiently and maintain a competitive edge in the rapidly evolving battery market.
Conclusion
Prismatic cells are a mark of advancement in battery technology. They offer higher energy density and improved design flexibility for diverse applications. Although they have challenges like manufacturing costs and complexity, the advantages they offer outweigh these considerations.
SZJ Automation offers a trailblazing prismatic cell turnkey solution that improves the battery industry’s manufacturing process. Their automatic assembly line integrates advanced technology and precision engineering to streamline production. It ensures that manufacturers can effectively meet growing demands.
Recently, they established a new factory in Xiangyang, Hubei, China, in order to study and deliver more advantages battery assembly machines for their clients. If you are interested, contact them to learn more information!
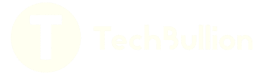