In terms of design, development, and manufacturing, the automotive industry stands at the pinnacle of industrialization, alongside other gigantic and complex manufacturing industries. At each point, there is an immense pressure for car manufacturers to meet up with the ever-growing auto market demands. This situation implies that they have to develop innovative designs that place them at the forefront of customers’ appeal and satisfaction consistently. With such tasks at hand, each phase of the automotive design and development cycle must align with the manufacturing goals – to create aesthetic and high-performing vehicles that match the customers’ preferences. In this vein, fabricating ideal custom prototypes plays an essential role in bridging the gap between the conceptual phase and the final roll-out phase of production.
With custom prototyping in the automotive industry, automobile manufacturers can optimally verify the design process, monitor the manufacturing process at the highest standard, and fabricate high-fidelity components using the best material. It is worth mentioning that prototyping is one of the integral parts of the engineering process in the automotive industry. This statement implies that car manufacturing companies come up with various strategies and techniques to manufacture vehicles that do not only stick to the industry standard but also appeal to consumers and potential investors.
The Automotive Design and Development Cycle
There are several stages embedded in the automotive design and development cycle; they include the following:
- Proof of concept
- Modeling and visualization of Computer-Aided Design (CAD) digital model
- Verification of the vehicle’s structure and performance
- Function and engineering test
How does each phase contribute to an automobile manufacturing process? At the concept design and modeling phase, automotive design engineers turn vehicle sketches into scale prototypes, with the aid of clay modeling. This model serves as the foundation for conceptual design. Using reverse engineering technology, these experts develop actual CAD models from these prototypes to augment the overall automotive model. This process may run for a while to ensure that design engineers fully acquaint themselves with design elements that will provide optimum user experience, and also communicate them to respective team members, stakeholders, and clients.
Once these parties validate the concept, design engineers can move on to the next phase, also known as the “mule stage, “to refine the prototype by eliminating previous design bottlenecks and evaluating the functionality and operability of the automobile product. What this means is that the design experts will fabricate functional custom prototypes that can work in an existing vehicle. This process helps them to run checks on the component’s confinement to dimension and gather information on its performance. In simpler terms, automotive design engineers can check how a prototype fits into a car and interact with other automotive parts. Information from this evaluation can help to determine the design, functional mechanism, tolerance, strength, production, and assembly of an automobile prototype.
Having satisfied the requirements for the mule stage, the automotive designers can fabricate engineering prototypes, along with pre-manufactured components in small units. This stage is essential to the automotive manufacturing process, as it determines whether a car manufacturing company can commence production or review their engineering prototypes. These components share close similarities with the end product in terms of appearance and functionality. During this phase, it is paramount that custom-built prototypes pass the following requirements: verification, testing, performance, certification, and quality.
In the aspect of testing, automotive prototypes must be safe for clients to use. For this reason, they undergo scrutinized testing under varying scenarios and extreme conditions. With this rigorous evaluation test, engineers can determine if a component is safe to install in a vehicle.
Understanding Various Custom Prototyping Parts
Custom auto parts usually fall into three categories, namely: Interior, exterior, and functional components.
- Interior Components
Car manufacturers can product prototypes tailored to augment the interior of a vehicle. These components include:
- Consoles
- Dashboards
- Steering wheel
- Armrests
- Central control panel
- Air vents and ducts
- Switchplates
- Speaker grilles
- Door panels
- Trim pieces
- Car pillars
- Exterior Components
Exterior prototypes enhance the exterior aspect of a car. These prototypes include:
- Headlights
- Door handles
- Grilles
- Grille covers
- Taillights
- Bumper
- Mirror housing and mounts
- Fog lamps
- Trunk lids
- Spoilers and air dams
- Fenders
- Fender liners
- Chrome trim
- Functional Components
These are prototypes that house the electro-mechanics of a vehicle; they include:
- Fuel tanks
- Engine cover
- Air filter housing
- Air components
- Battery components
- Shifting device lid
Design engineers take into consideration manufacturing details and finishes when fabricating an automotive component. However, they cannot achieve this without having expert knowledge and experience and using advanced prototyping machines and techniques. These machining methodologies include 3 to 5-axis CNC milling. As the automotive industry has taken a quantum leap in technology, some manufacturers presently use single-point diamond turning (SPDT) – especially for the fabrication of lighting prototypes. This machining technology gives the component the best appearance and functionality.
Delving further into the subject of automotive custom prototyping, car manufacturers develop functional prototypes for the following goals:
- To comply with the complex functional mechanisms of an automotive component and its conformity to fitness and build.
- To use these prototypes as simulations of the end products in terms of material properties and functionality.
- To compare and evaluate tolerances, dimensional disparities, and design flaws.
What Makes Custom Prototyping Top-Notch in the Automotive Industry?
There are several advantages of manufacturing automotive custom prototypes, especially in the automotive design and development cycle; They include:
- Speed
As a result of the high demand in automobiles worldwide, car manufacturers have to increase their production output while maintaining quality delivery. In other words, speed is essential in fulfilling market demands. For this reason, car manufacturers implement various technologies to automate their manufacturing process, including the use of CNC technology. With such methodologies, it is easy to make custom auto parts in large quantities and with outstanding precision. There are heavy-duty machines that execute the fabrication process seamlessly and repeatedly.
- Accuracy
In the automotive industry, precision is everything, as one wrong dimension or cut can spell doom to a batch of automotive products, leading to financial and material loss. As a result, engineers must fabricate automotive prototypes using a high level of precision. Each component must be exact with the next in appearance, dimension, and functionality. With manual labor or other less-sophisticated machining techniques, it is difficult for a manufacturer to achieve this goal.
However, using custom rapid prototyping, machinists can produce components with delivering tolerance of up to ±0.001. This feature is critical in the automotive industry as it decides the optimum performance of a car and the safety of the driver.
- Repeatability
A typical manufacturing process involves repeatability, especially where manufacturers have to produce a batch of the same model. As such, there should be no difference between Product A and Product B of the same set. With other techniques and methodologies, it may be challenging to accomplish this task, but not with automotive custom prototyping. Car manufacturers can produce the same product multiple times without discrepancies in-between each prototype; this comes into play when manufacturing a component in large volumes.
- Cost-Effectiveness
Custom-fabricated prototypes require less human intervention. As a result, there is little to no manual labor, which means fewer expenses for the manufacturer. Simultaneously, the automotive fabricating machines produce high-fidelity custom parts at unimaginable speeds, thereby reducing the manufacturing lead time of a car company.
Knowing What Prototyping Process to Use
Several factors determine the type of prototyping technology a car manufacturer should use in developing prototypes. Interestingly, it all boils down to using CNC machining, 3D printing technology, or injection molding. Each process has its unique merits. Hence, a car company may want to look at the following:
- The type of vehicle components they intend to produce.
- The type of material they need to produce the prototypes; this could be any substrate, including plastics and metals.
- The geometric complexity of the component they intend to fabricate.
- The timeframe for production – this spans from the initial design phase to the manufacturing phase.
- The level of perfection they intend to achieve in designing the component; this is in terms of aesthetics and functionality.
As the automotive industry continues to advance, fewer companies manufacture vehicles by hands, except for the high-end luxury vehicle lines, like Rolls-Royce (owned by BMW) that are handmade. For other manufacturers, various robotics come into play to produce vehicles with precision and perfection. These automobile companies use high-tech 5-axis prototyping machines and up-to-date CAD software to design components of several cars, accurately and efficiently.
What Does the Future Hold for Automotive Custom Prototyping?
There are various views on which prototyping technology would usher the automotive industry into the next phase. However, it would suffice to say that the automotive world is gravitating towards additive manufacturing. There are stable releases of state-of-the-art materials, techniques, and even machines that improve the 3D printing industry. Manufacturers are implementing new ways to augment their designs and convert them to actual workable prototypes.
In all, the goal is to exceed the current limits in the aspect of car performance and customer satisfaction. This idea will further promote competition among auto companies, ensuring that the automotive industry stays relevant. Although overwhelming, car manufacturers can develop new ways to produce vehicles faster and more efficiently using various custom prototyping technologies.
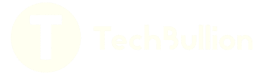