A quiet revolution is reshaping the world of optometric manufacturing. Where once lens crafting and frame assembly relied on human intuition and manual precision, today’s optical production floors are humming with data-driven intelligence. The rise of Industry 4.0—the integration of automation, AI, and real-time connectivity—is transforming traditional optical manufacturing into an interconnected web of smart, agile factories. As optometric demands grow more complex, smart factories have emerged as critical enablers for lens and frame producers worldwide.
In this evolving landscape, the fusion of robotics, machine learning, and cloud computing allows optical manufacturers like OPTI USA to meet consumer expectations for personalization, speed, and quality. The optical industry, with its precise tolerances and high-value products, is fertile ground for the sweeping changes driven by Industry 4.0 and smart factory innovations.
What is a Smart Factory and Why Does it Matter for Optical Manufacturers?
A Smart Factory is a highly digitized and connected production environment where machinery and equipment autonomously improve processes through self-optimization and learning. It leverages real-time data and cyber-physical systems to drive efficiencies and enhance production capabilities.
For optical manufacturers, the smart factory is more than a buzzword—it’s a necessity to remain competitive. The precision and customization demands in eyewear production, from intricate lens coatings to complex frame geometries, require seamless workflows and flawless quality assurance. By embracing smart factory principles, optical manufacturers gain agility, reduce lead times, and achieve consistent product quality across every production run.
Key components of a smart factory include:
- Industrial Internet of Things (IIoT) for real-time machine connectivity
- Artificial Intelligence (AI) for predictive insights and defect detection
- Robotics to automate repetitive and precision-heavy tasks
- Data analytics platforms to enable informed decision-making
- Cloud computing for remote monitoring and scalable operations
- Cyber-physical systems linking the physical and digital worlds
Optometric manufacturers worldwide are embedding these technologies into their production floors. From digitally simulating entire lens production lines to automating polishing and coating processes, smart factories are redefining optical craftsmanship.
How is Industry 4.0 Shaping the Optical Manufacturing Sector?
Industry 4.0 refers to the fourth industrial revolution, which integrates advanced digital technologies like cyber-physical systems, cloud platforms, and artificial intelligence into manufacturing processes. For optical manufacturers, this shift enhances operational visibility, precision, and speed, while opening doors to scalable mass customization.
Pillars of Industry 4.0 in optical manufacturing:
- Cyber-physical systems: Integration of sensors and software with production machinery
- Cloud computing: Data storage, processing, and analytics at scale
- Industrial Internet of Things (IIoT): Networking of machines, devices, and systems
- Artificial Intelligence (AI) & Machine Learning: Autonomous process improvements and real-time defect detection
- Big Data & Advanced Analytics: Actionable insights from large datasets
- Additive manufacturing (3D printing): Prototyping and small-batch optical components
The global push toward smart optical factories is accelerating. Manufacturers are shifting away from rigid, batch-based production models and toward agile, fully connected systems. In lens production, AI and real-time data are reducing error rates and streamlining coating and assembly stages. Meanwhile, IIoT-enabled equipment is providing optical firms with predictive maintenance capabilities, drastically cutting downtime and extending machinery lifespan.
Emerging markets, such as Asia-Pacific, are adopting Industry 4.0 faster due to increasing demand for premium eyewear and rapid urbanization, further pushing manufacturers to innovate.
What Technologies Power Smart Factories in Optical Manufacturing?
Smart optical factories are defined by the interplay of interconnected technologies. From intelligent machines to virtual replicas of production floors, these tools create an ecosystem where efficiency and precision thrive.
Industrial Internet of Things (IIoT)
In optical factories, IIoT enables machines, tools, and systems to share data seamlessly. By embedding sensors and connected devices into equipment like surfacing machines or frame cutters, manufacturers gain real-time insights into production parameters.
IIoT applications in optical manufacturing:
- Monitoring lens surfacing pressure and speed via connected sensors
- Real-time tracking of frame cutting machines to optimize material use
- Automated alerts for polishing machine wear and tear
- Temperature and humidity control systems for coating rooms
- Energy consumption analytics for each production cell
Artificial Intelligence & Machine Learning
AI and ML algorithms analyze production data to predict failures, optimize workflows, and ensure consistent product quality in optical factories. These systems are particularly valuable in managing the complexities of lens coating, assembly, and polishing.
AI-driven innovations in optical production:
- Predictive maintenance algorithms reducing unplanned downtime
- AI-based defect detection in lenses during coating and curing stages
- Machine learning optimization of polishing cycles for higher yield
- Intelligent scheduling and resource allocation for assembly lines
- AI-driven adjustment of surfacing parameters based on historical quality data
Robotics & Automation
Robotic systems in optical factories handle repetitive and high-precision tasks with unmatched consistency. From lens surfacing to frame assembly, robotics ensures tight tolerances and accelerated production times.
Common robotic tasks in optical manufacturing:
- Pick-and-place operations for lenses and frames
- Automated polishing and edge-smoothing of lenses
- Robotic frame welding and cutting
- Handling of coated lenses during curing processes
- Automated packaging and labeling of finished eyewear
Digital Twins & Simulation
A digital twin is a virtual model of a physical production system. Optical manufacturers use digital twins to simulate processes, optimize equipment layout, and test production scenarios without disrupting real operations.
Benefits of digital twins for optical factories:
- Faster prototyping of lenses and frames
- Reduced equipment downtime via predictive simulations
- Optimization of production floor layouts
- Simulating process adjustments before real-world implementation
- Continuous process improvement through virtual testing
Cloud Computing & Big Data
By integrating cloud platforms, optical manufacturers centralize their data and gain access to powerful analytics tools. Cloud computing supports remote monitoring, allowing managers to oversee operations across multiple sites in real time.
Metrics monitored via cloud systems:
- Overall Equipment Effectiveness (OEE) for each machine
- Production throughput and yield rates
- Maintenance logs and failure predictions
- Energy consumption trends across facilities
- Scrap and rework rates by production line
What Are the Key Benefits of Smart Factories for Optometric Manufacturers?
Smart factories are redefining the competitive edge for optometric manufacturers. By combining automation, real-time analytics, and interconnected systems, these facilities deliver a range of benefits tailored to the demands of the optical industry.
Key advantages include:
- Higher precision in lens crafting and frame assembly processes
- Waste reduction through optimized material usage and defect minimization
- Faster time-to-market by streamlining production cycles and reducing bottlenecks
- Energy efficiency via smart resource allocation and energy-saving equipment
- Predictive maintenance that prevents costly downtime and extends equipment life
- Customization and mass personalization to meet growing demand for tailored eyewear
- Enhanced product consistency through automated quality control and standardization
In an industry where micron-level accuracy defines product value, the shift toward smart manufacturing is allowing companies to consistently exceed customer expectations while reducing operational risks.
How Do Smart Factories Enhance Lens & Frame Manufacturing?
The impact of smart factories extends deep into the optical production line, revolutionizing how lenses and frames are crafted, coated, and assembled. Automation and AI are applied at nearly every stage to enhance quality, speed, and flexibility.
Steps within optical manufacturing benefiting most from automation:
- Automated lens surfacing and polishing
- Robotic coating and curing systems
- CNC-based frame production and assembly
- AI-powered quality control and defect detection
- Integrated inspection and packaging stations
Automated Lens Surfacing & Polishing
Precision and surface uniformity are critical in lens manufacturing. Robotic surfacing machines equipped with AI algorithms now autonomously adjust parameters like pressure and rotation speed, achieving highly consistent tolerances. Polishing automation eliminates manual variability, resulting in lenses with superior optical clarity and durability.
Coating & Curing Processes
Automated coating lines apply anti-reflective, photochromic, and scratch-resistant treatments with accuracy beyond human capabilities. Intelligent curing systems monitor variables such as UV exposure and temperature in real-time, ensuring coatings are hardened perfectly, reducing rejection rates.
Automated Frame Production & Assembly
Modern frame manufacturing utilizes CNC machinery and robotic arms to cut, weld, and assemble frames from diverse materials such as acetate, titanium, and stainless steel. Automated assembly lines handle intricate processes like hinge attachment and frame shaping, while adaptive robots manage component handling with precision.
Quality Control & Inspection Systems
AI-powered vision systems now perform detailed inspections on every lens and frame. These systems detect surface defects, misalignments, and coating inconsistencies faster and more accurately than manual checks, helping to maintain high product quality standards.
What are the Challenges of Implementing Industry 4.0 in Optical Manufacturing?
While smart factories offer significant benefits, transitioning to Industry 4.0 isn’t without its challenges, especially for legacy optical manufacturers.
Main challenges include:
- High initial investment: The upfront capital required for robotics, IoT devices, and AI platforms can be substantial.
- Integration complexity with legacy systems: Many older production lines require retrofitting to integrate with modern digital technologies.
- Skills gap: There’s a growing demand for skilled technicians and engineers capable of managing and maintaining smart systems.
- Cybersecurity concerns: As factories become more connected, the risk of cyber-attacks increases.
- Data silos: Disconnected systems can hinder the free flow of information across departments and production lines.
Tips for overcoming challenges:
- Start with pilot projects to validate ROI before full-scale implementation.
- Invest in employee training to close the skills gap and promote tech literacy.
- Partner with experienced system integrators for smoother legacy upgrades.
- Implement robust cybersecurity protocols, including network segmentation and encryption.
- Use cloud-based data lakes to break down silos and centralize insights.
What Are the Best Practices for Transitioning to a Smart Factory?
A strategic and phased approach is essential for optical manufacturers aiming to embrace Industry 4.0 without disrupting existing operations.
Actionable best practices:
- Conducting a readiness assessment to evaluate infrastructure, workforce, and digital maturity
- Starting with pilot projects focused on high-impact areas like surfacing or quality control
- Training and upskilling staff to ensure a workforce capable of managing advanced technologies
- Choosing modular and scalable solutions that can grow with production needs
- Partnering with tech vendors who specialize in optical manufacturing automation and smart factory implementation
Optical firms that follow these best practices often report faster transitions, smoother technology adoption, and quicker realization of ROI.
How Can Optometric Manufacturers Leverage AI for Competitive Advantage?
AI is no longer just a futuristic concept—it is an essential tool in today’s optical manufacturing ecosystem. Manufacturers are using AI not just for factory floor automation but for broader business optimization.
AI systems now provide insights that optimize supply chains, reduce equipment downtime, and elevate product quality. Whether forecasting demand trends or identifying process inefficiencies, AI is driving more informed and agile decision-making.
AI use cases in optical factories:
- Predictive analytics to forecast maintenance needs and production performance
- Automated defect detection using machine vision to spot microscopic flaws
- Production planning algorithms that balance workloads across lines
- Inventory management optimization based on real-time usage data and demand forecasts
These applications empower optical manufacturers to maintain high output quality while minimizing waste and production costs.
What Role Does Sustainability Play in Smart Optical Factories?
Sustainability has become a core priority for optical manufacturers adopting Industry 4.0 technologies. Smart factories enable greener operations by optimizing material use, reducing emissions, and embracing circular economy models.
Sustainable practices enabled by Industry 4.0:
- Reduced material waste through precision cutting and defect minimization
- Energy-efficient machines that consume less power during production
- Circular economy initiatives, such as recycling lens and frame materials
- Eco-friendly materials sourcing for sustainable product lines
- Reduced carbon footprint via smart logistics powered by AI-driven route optimization
These practices not only contribute to environmental goals but also enhance brand reputation and meet growing consumer demands for eco-conscious products.
What Trends Will Shape the Future of Smart Optical Manufacturing?
As Industry 4.0 technologies mature, new trends are emerging that will further redefine optical manufacturing. These innovations will not only enhance operational efficiency but also unlock unprecedented levels of customization and agility for optometric manufacturers.
Emerging trends:
- AI-driven design automation that streamlines lens and frame design workflows
- Autonomous mobile robots (AMRs) for intra-factory material handling and logistics
- Augmented reality (AR) for remote maintenance, allowing technicians to troubleshoot equipment from anywhere
- Edge computing to process factory-floor data locally for faster decision-making
- Human-robot collaboration (cobots) that combine the precision of machines with human flexibility
- Advanced additive manufacturing (3D printing) in optics, enabling rapid prototyping and custom part production
- Hyper-personalized optical products using customer data to offer fully tailored eyewear experiences
These trends will accelerate the optical sector’s shift toward smart, flexible, and customer-centric production models.
How Does a Smart Factory Improve Customer Experience in Optometry?
Smart factories don’t just enhance manufacturing—they directly improve customer experiences. By automating key processes and leveraging data insights, optometric manufacturers can meet client expectations faster and more consistently.
Customer-facing improvements:
- Faster delivery times thanks to streamlined and agile production workflows
- Personalized lenses and frames with precision customizations based on individual preferences
- Transparent production tracking that allows customers and partners to monitor order progress
- Improved product quality and durability through advanced quality control and defect-free outputs
For B2B clients, this means more reliable order fulfillment. For end consumers, it translates to a more tailored eyewear experience with faster access to new designs and custom products.
What Are the Essential KPIs to Track in a Smart Optical Factory?
Monitoring performance is critical in smart factory environments. By focusing on key performance indicators (KPIs), optical manufacturers can optimize production efficiency and quality.
Key metrics include:
- Overall Equipment Effectiveness (OEE) to measure availability, performance, and quality
- Production yield to track the percentage of usable products from total output
- Mean Time Between Failures (MTBF) to assess equipment reliability
- Energy consumption per unit for monitoring energy efficiency
- Scrap rate to evaluate material waste and production losses
- Customer satisfaction score reflecting product and service quality
- Lead time per order for assessing supply chain and production agility
What’s the Investment Cost for Smart Factory Adoption in Optometry?
Investing in a smart factory varies depending on production size, existing infrastructure, and technology scope. However, even modest transitions to Industry 4.0 yield significant long-term gains.
Factors influencing investment costs:
- Size of facility and production volume goals
- Type of technologies adopted, such as AI platforms, robotics, or IIoT systems
- Integration with existing systems and legacy equipment upgrades
- Staff training requirements to upskill teams on new systems and workflows
While initial CAPEX and OPEX can be substantial, smart factories often realize cost savings through reduced downtime, lower defect rates, and improved resource efficiency.
What Tools and Partners Should Optometric Manufacturers Work With?
Collaborating with the right technology partners is key to successful smart factory implementation.
Recommended tools and partners:
- Industrial automation providers for robotic and automated machinery
- ERP & MES software vendors for production and resource planning
- Robotics integrators to customize robotic systems for optical manufacturing needs
- IoT hardware suppliers to connect machines and sensors across production lines
- Cloud platform partners for data management and analytics
- AI/ML solution providers for predictive modeling and intelligent process automation
What Are the Alternative Strategies If Full Smart Factory Adoption Isn’t Feasible?
Not all manufacturers can fully adopt smart factory models right away. There are alternative strategies to incrementally improve production and remain competitive.
Alternative options:
- Semi-automation of high-impact processes like surfacing and inspection
- Lean manufacturing methods to eliminate waste and optimize workflows
- Outsourcing to smart-enabled suppliers for certain production steps
- Incremental upgrades (e.g., retrofitting) to existing equipment with IoT sensors or automation modules
These hybrid strategies can provide many of the benefits of smart factories while spreading investment costs over time.
Conclusion
The optical manufacturing industry stands at the forefront of an automation-driven transformation. Industry 4.0, with its ecosystem of smart technologies, is reshaping how lenses and frames are designed, produced, and delivered. From predictive AI systems optimizing production lines to robotics performing delicate tasks with micrometer precision, smart factories are enabling optical manufacturers to thrive in an increasingly competitive and sustainability-conscious world.
As customer expectations evolve, embracing smart factory principles is no longer a luxury—it’s a strategic imperative. Optometric manufacturers looking to stay ahead should assess their current operations, explore pilot projects, and partner with the right technology providers to unlock the full potential of Industry 4.0.
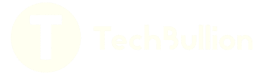