One of the most important steps in injection molding is choosing the material to use during the process. The type of material you choose will determine whether your process will be efficient based on its ability to balance cost and performance. The structure of the material also affects functionality and durability. This article will provide all the necessary information you need to consider before deciding on the type of material to use for your plastic injection molding services. Take note of the pros and cons and weigh your options carefully to avoid making a bad choice.
Understanding the Key Material Properties for Injection Molding
Mechanical properties
Strength: This is the ability of a material to bear heavy loads. Strong materials are used to produce parts that bear a lot of weight and are exposed to friction such as vehicle parts. The low-strength materials are used to create packaging containers.
Flexibility: This is the ability of a material to change form without losing its functionality. Flexible materials are used to make tubing and medical instruments while rigid ones make covers for electronics and vehicle parts.
Impact resistance: This is the ability of a material to withstand sudden force. Highly resistant materials are used to make safety equipment while those with less resistance make decorative parts.
Thermal properties
This is the most important property for parts exposed to extreme temperatures. Materials with high tolerance to heat do not deform or lose their structure in high temperatures. Those with poor thermal properties melt on the slight increase in temperatures.
Chemical Resistance
This is a key characteristic of materials used to make containers to store chemicals and parts that are exposed to corrosive fluids. Some materials can be reinforced to achieve this property.
Electrical conductivity
Materials with good electrical conductivity are used in making connectors and shielding while those with poor ability to conduct electricity are used to produce insulators. You must consider this when dealing with electrical devices.
Common Types of Materials Used in Injection Molding
Thermoplastics
ABS: This is a strong and flexible material that is commonly used in the automotive industry. The cost of purchasing ABS is not so high and it can be recycled.
Polypropylene: Polypropylene is very flexible even in stressful environments. Due to its excellent ability to dissipate heat, one can use it in high temperatures. It is quite cheap and you can easily recycle it.
Polystyrene: This plastic easily breaks on the application of pressure. It is quite rigid and does not do well under high temperatures. It is very cheap and one can recycle it.
Thermosets
Epoxy: Epoxy forms tough solid plastics that can tolerate high temperatures. It easily chips off without extra support. You can use it for cementing and coating products.
Phenolic resin: Phenolic resin can be used to produce insulators. It has a high tolerance to heat and is durable.
Elastomers
Silicone: Silicone is elastic and ideal for making parts to be used in situations that require some degree of bending. This material functions optimally under high temperatures and pressure. It is durable and used to make containers to package food.
Rubber: Rubber is highly flexible just like silicone. It is a good shock absorber that is pocket-friendly. Rubber can easily be customized and tailored to your liking.
Bio-based Plastics
Bio-based plastics like PLA are derived from plants. This makes them biodegradable and thus friendly to the environment. They can be used to make non-toxic containers for food and medical equipment. They easily melt and thus have short cycle times.
Factors to Consider When Choosing a Material
End-Use Requirements
You have to consider where the final product made from the plastic you chose will be used. Manufacturers in the food industry should choose plastics that are non-toxic to the body and those that maintain their structural integrity under high temperatures. The material chosen for kitchen appliances must be easy to clean. Those in the vehicle manufacturing industry should go with plastics that are strong, durable, and flexible. Analyze your industry and pick a plastic that is best suited for it.
Cost Consideration
Any business producing parts needs to balance between cost and performance. This will determine whether you accumulate profits or losses in the long term. High-performance plastics are more expensive than other types of plastics but guarantee accurate results. When dealing with parts that require precision and durability, choose tough and high-performing plastics. You can select low-grade and less costly plastics when creating packaging containers.
Moldability and Processing Considerations
Plastics have varying melting and cooling rates. Some have even shrinkage rates while others shrink uniformly. Those with a low melting point use less energy to process than those with a high melting point thus easier to process. Materials with a fast cooling rate also form parts easily compared to those that take longer to process. It is easier to work with plastics that flow well once melted than those with high viscosity since they quickly fill the mold cavity.
Availability and Supply Chain
Availability of the Material: Materials that are produced in large numbers are widely available but those that take time to produce like high-performance plastics can be scarce. This is because only those with large sums of capital get into such businesses. Materials that are in demand can also be lacking when there are production delays.
Lead Times: Widely available materials have shorter lead times than scarce materials. Those with high melting points and slow cooling rates have long lead times compared to simple plastics. It always takes you longer to create parts made from imported raw materials than those from locally available plastics.
How to Test and Validate Your Material Selection
Prototyping
Seeking out rapid prototyping service is key because it allows you to evaluate how your parts will perform in real-world situations. Prototyping encourages innovation since you can come up with solutions to any defect you pick. It is at this stage that you can improve your part’s functionality and workability.
Material Testing
During this stage, you can test your part’s strength, flexibility, and ability to resist heat and corrosive chemicals. Testing allows you to determine if your part meets the expectations of the customers.
Collaboration with Material Suppliers
You should have a good relationship with raw material suppliers to build trust. This ensures you get enough honest information regarding the application and properties of that raw material to produce optimally functioning parts.
Conclusion
Always choose the best material to use for your injection molding process to get the best results. An ideal plastic will fall within your budget and perform optimally. Only overstretch your pockets for materials that are right for your project.
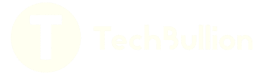