Plastic injection molding is a manufacturing process in which molten plastic is injected into a mould cavity chamber designed for the generation of the desired shape and size of the product mould. At the process level, injection molding is supposed to yield flexibility to handle different types of materials and flexibility to generate different parts for various needs in production. Injection molding is an important manufacturing process in this modern age because it overcomes many production challenges encountered in conventional manufacturing methods and the production cost remains low. Industrial applications of plastic injection molding include the automotive industry, consumer electronics industry, medical devices industry as well as the packaging industry, and this article will look at each of them.
Image source: https://frigate.ai/
1. Automotive Industry
Plastic injection molding is mainly used in the automobile industry to produce high precision parts such as dashboard components, bumpers, and engine components. In the manufacture of dashboard components, automotive injection molding helps create smooth surfaces, textured surfaces, or gloss surface finishes, while allowing creation of complex shapes and cuts, ensuring parts meet their requirements fully. Bumper production takes to account the weight, shape, size and durability of the final product which makes injection molding ideal for their production. The process allows for creation of layered parts in one process producing the desired different effects and properties all at once. For engine components production, the design needs to be able to handle high temperatures and maintain precise dimensions.
By combining different injection inputs in one mould and allowing for creation of layered coats all in one single process helps produce durable, lightweight and cost effective components while facilitating production in large quantities and ensuring quality of finished products.
2. Consumer Electronics
The use of plastic injection molding when manufacturing consumer electronics allows the use of different types of hydrocarbons to be combined onto a single process which generates plastic enclosures and housings of consumer electronics with the desired durability effects. Through molding design, consumer electronics production can be achieved with creation of custom designs featuring various shapes, sizes, open cuts and sleek edges. The process enables production of many lightweight and durable housing parts at the same time. This is a necessary and essential quality of the process which ensures protection of sensitive electronics while maintaining aesthetic appeal of the consumer products.
Some consumer electronic parts such as buttons, connectors and ports require complex geometry cuts and designs to achieve desired results. Advances in plastic injection molding technology have delivered a breakthrough in this production challenge. The process allows for the creation of parts with varying textures, key shapes, and even integrated tactile feedback features, ensuring ease of use and user comfort. Injection molding enables high volumes of uniform keypads and buttons with minimal defects and a consistent tactile feel for the user, a feature that helps promote mass production while keeping production costs minimal.
3. Medical Devices
When manufacturing medical components such as syringes, IV components and diagnostic tools, precision is the key to success. These devices are an important part of the whole patient care system, and any design, production or functional defect can cause serious issues, such as contamination, wrong dosage or wrong diagnosis. These must be precisely manufactured, so that they are fully functional and provide patient comfort. Medical injection molding plays a critical role in achieving the high precision standards needed for these components, creating tight tolerance levels that help maintain sterility and eliminate the risk of leaks or contamination.
In the medical industry, using biocompatible materials is essential to ensure patient safety, and environmental conservation. Several biocompatible materials intended for medical device applications are used in the injection molding process which is widely used because of its high performance ratings in ensuring sterility, and safety requirements of products. They include Medical-grade polypropylene used for manufacturing components with high resistance to chemical interaction process and one that can be sterilized easily; polyethylene is used for manufacturing medical tubes, connectors, packaging and implants because it is easy to sterilize and resistant to chemical reaction; polysulfone is used for manufacturing components such as dialysis filters, blood oxygenators, fluid handling systems because it is resistant to sterilization. Silicone is one of the most biocompatible materials available. It is known to resist bacterial growth and is widely used on products that provide direct contact with human tissue.
Worldwide, the medical devices development industry is heavily regulated. Regulatory agencies include; U.S Food and Drug Administration (FDA), the European Medicines Agency (EMA), and so on. High quality standards are required for the components of any medical device to be certified for use. A good example would be a syringe manufacturer that must abide by ISO 13485 (an ISO standard for medical device quality management systems). They ensure that every component (needle, syringe body, etc) is precise to the exact specs needed to perform and be safe.
4. Packaging Industry
Packaging materials are a way of marketing as well as providing a protecting barrier to enclosed food products. Through injection molding, there are several advantages in manufacturing durable and low cost packaging products that preserve the integrity of the products, extend their shelf-life and meet the regulatory requirements in packaging of food and beverages. Vacuum packs are used in packaging of many pharmaceutical products and injection molding is critical in the production of such packs.
Precisely molded containers for a broad range of food products are manufactured through the injection molding process. For example, the process can be used to create jars and tubs used for yogurt, sauces and spreads product packaging. Secure closures are often required in food packaging regulations. Caps from bottles and jars are injection molded so that they fit tightly and keep the products ‘fresh’. Injection molding can also create very detailed designs on elaborate shapes and feature embossed logos as well as create tamper proof seals.
Recently, industries are more and more looking for sustainable packaging solutions to improve the environment. Recyclable materials like PET, PP and HDPE can be used in injection molding to support sustainability. Innovation in biodegradable polymers and lightweight products also cuts back on plastic waste and extends the use of injection molding as a sustainable packaging manufacturing process.
Conclusion
Plastic injection molding is simply critical in production processes as it plays a key part in components development in the automotive industry, the consumer electronic industry, the medical devices industry and packaging industry. Precision, dealing with complex product designs, saving time and money, and achieving product appeal and safety are the key undertones to injection molding processes in all these industries. The plastic molding process has the ability to adapt to the ever changing consumer trends making it a technology of choice for any future innovations. Currently, there are no consumer trends which the technology has not been able to adjust to as efficiently and effectively as possible, maintaining product quality and keeping production cost to the minimum. This adaptability capability of the technology has ensured that future innovation and technological set up shall always be informed by the relevance of the technology thus when new inventions arise, they will be dependent on interventions and adjustments to plastic injection molding to support their cause.
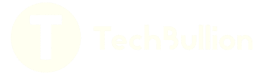