Implementing a quality management system (QMS) is important in order to maintain uniformity among all your processes, guaranteeing the quality and safety of the components in your products. But how exactly is process-based QMS implemented and why should enterprises add it to their toolkits?
What Is a Process-Based Quality Management System?
A process-based quality management system (QMS) integates several quality management workflowsinto a unified whole. This type of integrated QMS determines how the company’s quality policy is put into practice and helps the company achieves its quality and manufacturing objectives.
Benefits of Using a Process-Based QMS
The introduction of a process-based QMS has a positive impact on the overall performance of an organization, including:
- Reduce Cost of Quality: Reduce cost of quality to minimize business disruption, brand risk, and revenue impact.
- Improve Decision Velocity: Improve decision velocity by delivering trusted prescriptive and predictive information using analytics, automation, and AI.
- Improve Supplier Quality: Improve supplier quality to ensure positive business impact and enhanced customer loyalty.
- Accelerate Time to Market: Accelerate time to market by optimizing the product life cycle.
- Drive Compliance at Scale: Efficiently meet changing regulatory, compliance, customer, and market requirements at scale.
Implementing a Process-Based Quality Management System
Here are the basic steps to follow in order to implement a process-based QMS:
Design and Build
In this phase, an organization creates the framework for the quality management system, including needs assessment, critical processes to automate and a plan for deployment. It is important that the top management leads this part to ensure that the system meets both the needs of the company and the requirements of the customers.
Deployment
When it comes to QMS deployment, it can be quite effective to roll out the system in small steps. This means breaking each process down into smaller parts and educating employees on the necessary documentation, training tools and measuring success. .Nowadays, many companies are using their internal networks (intranets) to help put these quality management systems into place.
Measurement and Control
The implementation of a QMS requires regular and systematic checks of the system. The way in which these checks are carried out can vary greatly from organization to organization, depending on its size, the risks involved and the impact on the environment.
Reviewing and Improving
This last step is about what to do with the results of an audit. It is about finding out how well each process is working towards its goals and how efficient it is. It’s also about sharing these findings with employees and using the information gathered during the audit to create better procedures and processes.
To summarize,QMS systems offer companies many advantages, as they enable them to optimize their processes, offer high-quality products and services, reduce the cost of poor quality and. improve overall customer satisfaction. By implementing a robust Quality Management System (QMS), organizations can establish standardized procedures that streamline their operations, leading to increased efficiency and productivity. This structured approach not only helps in meeting regulatory requirements but also fosters a culture of continuous improvement within the company.
Read More From Techbullion
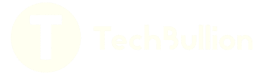