Precision manufacturing demands components to meet exact specifications consistently. Of all part features, threaded interfaces require the utmost accuracy to ensure proper fit and function. Even minute defects on critical threads can cause catastrophic failure, rendering the final product unsafe. This makes maintaining the integrity of threaded parts a top priority throughout production.
Utilizing high-performance thread gauges at multiple process checkpoints guarantees compliant parts that adhere to form, size, and accuracy standards. With so much relying upon flawless threads, investing in a reliable thread gauge solution for quality assurance is a prudent choice that yields dividends in end product safety and reliability.
Common Applications Relying on Precise Threads
Threads feature prominently in mission-critical applications spanning industries to enable joining and fastening. In automotive, properly torqued engine fasteners using threads protect against dangerous combustion leakage. Aircraft assemblies like landing gear hydraulic lines leverage threaded couplings to handle volatile pressure changes during flight. Train engines using pipe threading taps. Healthcare innovations like medical implants or MRI machines rely on precision threaded joints to avoid injury or operational failures under strain.
In all cases, manufactured threads operate under intense pressure, heat, or loading stress, where miniscule defects get amplified into big system failures. Such large-scale accidents underscore why manufacturers invest heavily in thread quality assurance across aerospace, defense, energy, and medical equipment sectors. With product reliability and human safety on the line, eliminating risks by maintaining perfect thread precision and accuracy remains imperative.
Risks from Poor Thread Quality Control
Inadequate thread inspection regimes pose serious quality threats. Faulty threads first manifest as fluid leaks or pressure drops, causing subpar system performance. Misshapen mating surfaces then exacerbate wear until components seize up or detach unexpectedly. These early signs often hide deeper microscopic cracks from stressed threads, which propagate to fracture critical support structures.
The financial toll also quickly piles up from crippled production lines. Excessive false thread rejects waste time and raw materials and congests workflows. Companies that persistently fail compliance audits for dimensional tolerance risk heavy penalties or supply chain blacklisting. However, the harshest long-term consequence stains hard-earned brand reputations, forcing even loyal big-ticket accounts to switch vendors reluctantly.
Attributes of High-Quality Thread Gauges
Thread inspection is only as reliable as the gauges themselves. Quality-conscious manufacturers select thread gauges certified against international ISO standards like ISO 1502. This baseline calibration guarantees accuracy down to millionths of an inch repeatedly, even under harsh industrial use. Durability also ranks high, so materials include wear-resistant carbides and protective coatings to withstand prolonged exposure to cutting fluids or abrasive metal chips.
Leading gauging fixture suppliers validate strength claims through extensive life cycle testing data. Other key versatile features include interchangeable anvils reaching internal threads in deep bores. Some high-precision gauges provide digital deviation output for each parameter like pitch diameter, flank angle, and lead error for granular trend analysis. This marries quality objectives with data-driven manufacturing.
Smooth production adoption requires gauges to easily integrate with existing platforms through mounting brackets or datalink conduits. Moreover, using adjustable components, the ideal gauge accommodates quick setup changes to measure a spectrum of thread types and sizes per application requirements. Automated gauging work cells further optimize throughput and consistency with programmable inspection routines.
Getting Maximum ROI from Measurement Tooling Investments
Procuring top-tier inspection hardware marks only the first step. Effective utilization best practices subsequently optimize functional gauge lifespan and sustain maximum metrological returns decade after decade.
Even with hardy materials and fine tolerances, neglect deteriorates precision. Thus, scheduling necessary preventative recalibration and validation preserves measurement reliability, especially for mission-critical quality checks. General workshops manage this internally through appropriate periodic checks against reference masters. High-stakes sectors often demand external audits by certified third-party labs to uphold the highest documentary evidence trials. Minor adjustments, then realign drifting performance metrics.
Equally vital is safeguarding metrology equipment from avoidable harm. Dedicated storage away from general tooling avoids accidental nicks and dents that distort precision alignments. Operators handle measuring instrumentation with due care, given their sensitivity. Gauges meant solely for dimensional inspection should not substitute hammers during improvised part fitting attempts – this preserves surface finish and geometric form essential for accuracy. Suitable personal protective wear while gauging also defends investments against preventable damage. Some fixtures may even require customized shielding or filtration against hostile environments.
Additional software analytics help maximize ROI by optimizing scheduling, forecasting service needs, and streamlining workflows. However, supportive, functional facilities, like temperature-controlled labs, also assist in securing stable ambient operating conditions. Ultimately, a comprehensive gauging investment program entails much more than purchasing a quality kit.
Conclusion
Strong, precise thread inspection is vital to mitigate product failures across safety-critical industries. Investing in certified, durable thread gauges and maximizing their Working lifespans through rigorous calibration protocols offers prudent future-proofing. When reputations and lives hang in the balance, unrelenting thread quality control provides returns that no enterprise can afford to ignore.
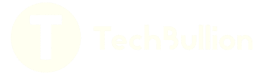