What is Plastic Molding?
Plastic molding is a process used to create multiple plastic products from a single original. The result of the initial injection molding can be anything: cups, keychains, car fenders, and bumpers, depending on the plastic material you use. Basically, the world is your oyster once you’ve got that first mold created.
1. Extrusion Molding
When you need a hollow shape to be filled, extrusion is best. Many bottles and tubes are made efficiently by this method. This process works for both long and cylindrical products.
The plastic, in this case, is pushed through a mold that determines the exact shape of the final product from start to finish. If there’s one basic rule of thumb to remember when considering the use of extrusion, it’s that the plastic must be melted into a liquid state before going through.
2. Injection Molding
All you need is some heat and pressure for this process. That’s all there is to it. The small pieces created by this molding method are most often found as tiny pieces of plastic used as a toy’s component parts.
Injection molding is done with a machine that uses two main parts: a screw and a barrel. The plastic granules go into the hopper of the machine, which heats the plastic up to its melting point.
When it reaches this point, the granule or pellets are squeezed into the barrel. Next, a screw forces it through a nozzle at high pressure to create long, thin rods of plastic. The rod is forced through a cylinder-shaped mold, where it’s held there by high pressure for a certain amount of time. This cooling process only takes about 10 seconds before the previous step can happen again and the process continues.
This type of molding is usually used for small, intricate parts that require high amounts of detail and strength. It’s commonly found in making medical devices or small consumer products like toys.
3. Rotational Molding
In rotational molding, pre-heated PVC pellets are placed in a hopper and metered by a screw. The material is then forced through an orifice to create a thin tube of plastic. This tube is cut to the right length and one end is put into the mold’s hollow core; this ensures that the part won’t fall out.
The tube is then rotated inside the mold, which heats it up and allows for the plastic to conform to the shape of the cavity. This is usually done with a centrifugal force that creates a vacuum, pulling material toward all corners of the mold simultaneously. A heating element is used to melt the PVC just before it’s injected into the mold. This allows the part to take shape without trapping any gases in its walls.
The plastic material is then injected into the cavity through a gate and runner system, which simply channels cuts into the mold for easy retrieval of the finished product. The excess material is cut away from the part after it’s ejected out of the mold, creating a molded piece that can then be painted or otherwise finished.
4. Blow Molding
The cavity of a two-piece blow molding tool is quite different from that of a one-piece tool. It has several smaller cavities instead of one large one, allowing the molten material to cool faster after it’s injected into the mold.
As the material cools, it shrinks slightly and creates stress on the mold, which causes it to separate after it ejects the finished product. Because of this, blow molding tools need to be opened carefully and slowly in order to avoid damage.
5. Compression Molding
The major benefits of compression molding are that it’s extremely quick and creates parts with very fine details.
There are several ways of compressing the mold, including applying pressure pneumatically or hydraulically or squeezing molds together between rollers. The material is fed into one side of the die cavity and compressed against a stripper plate that holds the other half of the mold shut. Then the material is injected and allowed to cool before being ejected.
Compression molds can be done almost instantly, as fast as a few seconds! This makes it a popular choice for mass production, but this type of plastic molding isn’t very detailed or accurate.
Conclusion
There are many benefits to all these methods, and which one is right for your piece will depend on what you need. If you want detailed, realistic pieces with long-lasting material that won’t warp or break upon removal from the mold, an injection mold would be a great choice.
If budget and production speed is more important than accuracy and quality, then compression molds could be just what you need.
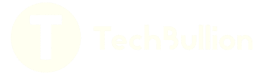